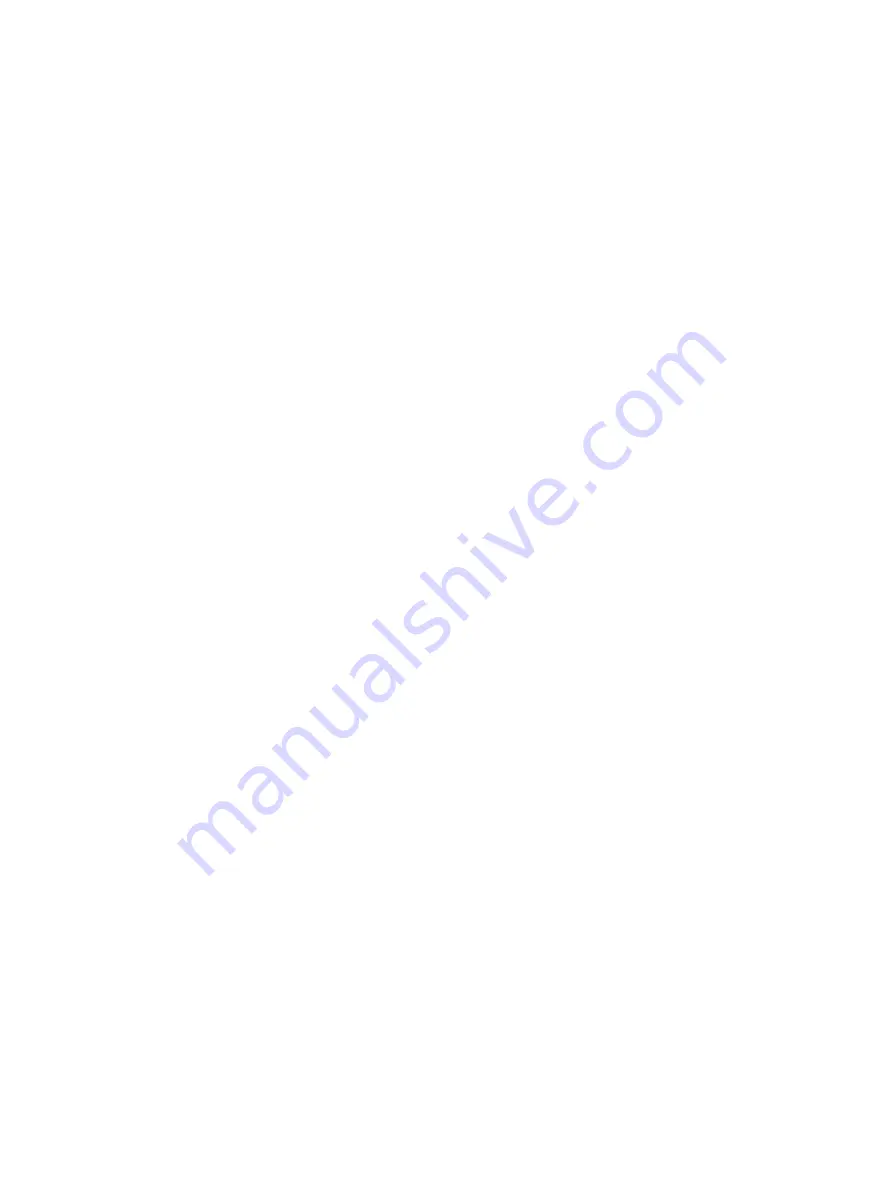
IO-Link system
Function Manual, 07/2022, A5E31637677-AC
8
System overview
2
Introduction
A continuous communication down to the lowest field level ensures enhanced use of the
functions and performance capability of sensors and actuators. Enhanced use of sensors and
actuators allows you to operate your machines and plants more productively.
No data other than the actual process value can be exchanged via the standard interfaces
(digital, analog) used at the sensor/actuator level. Sensors and actuators with integrated
intelligence are now used for increasingly complex functions and require a communication
interface tailored to these requirements.
Definition
IO-Link is an innovative, point-to-point communication interface for the sensor/actuator area
that is specified in IEC 61131-9.
IO-Link consists of the following system components:
• IO-Link master
• IO-Link device
• Unshielded 3-wire or 5-wire standard cable
• Engineering tool for configuring and assigning parameters of IO-Link
2.1
Advantages of IO-Link
The IO-Link system offers significant advantages as digital interface when connecting
sensors/actuators:
• Open standard in accordance with IEC 61131-9
– Devices can be integrated in the same way in all conventional fieldbus systems and
automation systems
• Tool supported parameter setting and central data management
– Fast configuration and commissioning
– Simple creation of current plant documentation even for sensors/actuators
• Single, uniform wiring and far fewer different interfaces at the sensors/actors
– Standardized, uniform interface for sensors and actuators independent of their
complexity (switching, measuring, multi-channel, binary, mixed signals, etc.)
– Reduction in the variety of types and inventory
– Fast commissioning
– Any combination of IO-Link devices and sensors/actuators without IO-Link at IO-Link
master