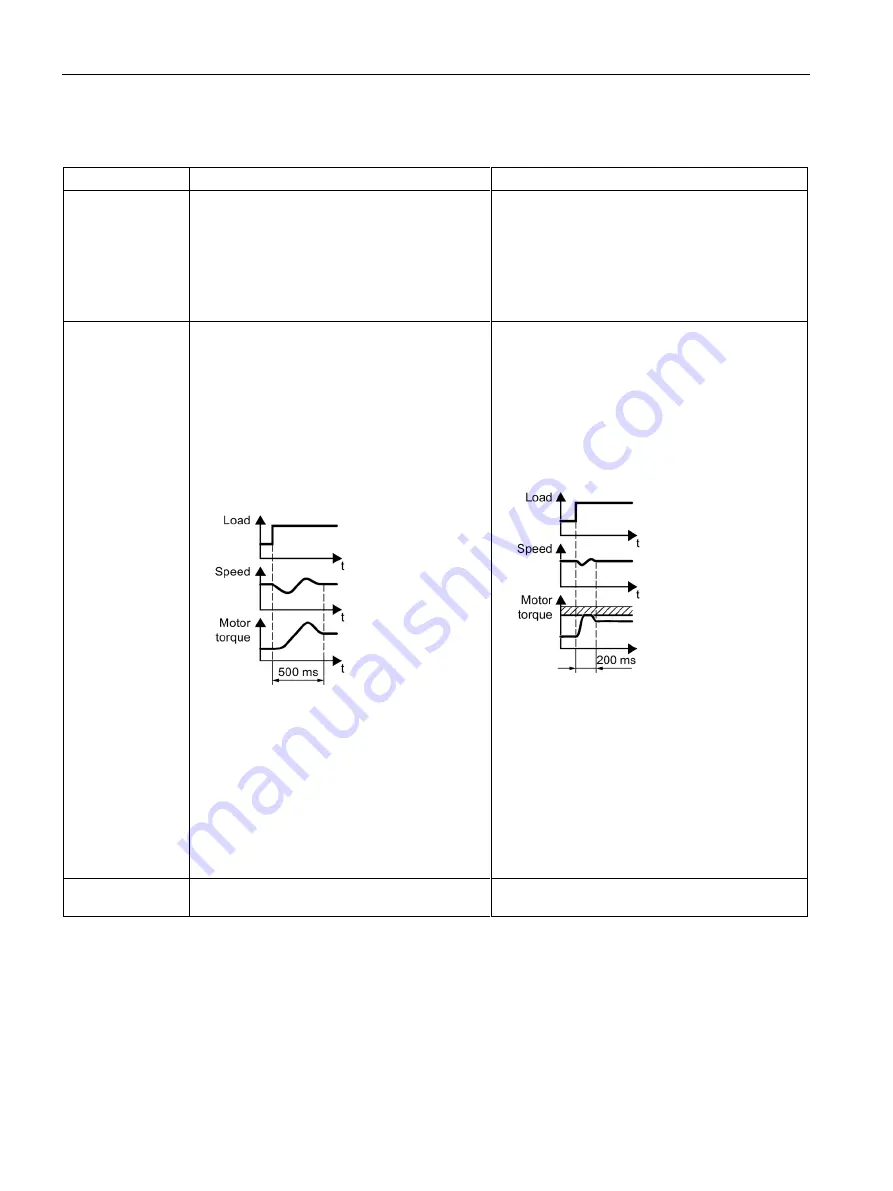
Commissioning
6.6 Quick commissioning
SIMATIC ET 200pro FC-2 converter
86
Operating Instructions, 04/2018, FW V4.7 SP10, A5E34257324B AF
Criteria for selecting either U/f control or vector control
U/f control or flux current control
Vector control without an encoder
Application exam-
ples
•
Pumps, fans, and compressors with flow
characteristic
•
Wet or dry blasting technology
•
Horizontal conveyor technology (conveyor
belts, roller conveyors, chain conveyors)
•
Basic spindles
•
Pumps and compressors with displacement
machines
•
Extruder
Properties of
closed-loop motor
control
•
The closed-loop control is insensitive to
inaccurate motor data settings, e.g. the mo-
tor temperature
•
Can be commissioned with just a few set-
tings.
•
Responds to speed changes with a typical
settling time of 100 ms … 200 ms
•
Responds to load surges with a typical set-
tling time of 500 ms
•
U/f and FCC are suitable for the following
cases:
–
For ramp-up times 0
→
rated speed > 2 s
–
For applications with increasing load
torque without load impulses
•
The vector control uses the converter, the mo-
tor and the mechanics highly efficiently (maxi-
mum motor voltage = 95% of the mains
voltage).
•
The vector control responds to speed changes
with a typical settling time of < 100 ms.
•
The vector control responds to load impulses
with a typical settling time of 20 ms.
•
The vector control is required in the following
cases:
–
For ramp-up times 0
→
rated speed < 2 s
–
For applications with fast and high load im-
pulses
–
For heavy duty starting using
≤
90% of the
stall torque of the motor
•
Vector control typically achieves a torque accu-
racy of ± 5% for 10% … 100% of the rated
speed
Max. output fre-
quency
550 Hz
240 Hz