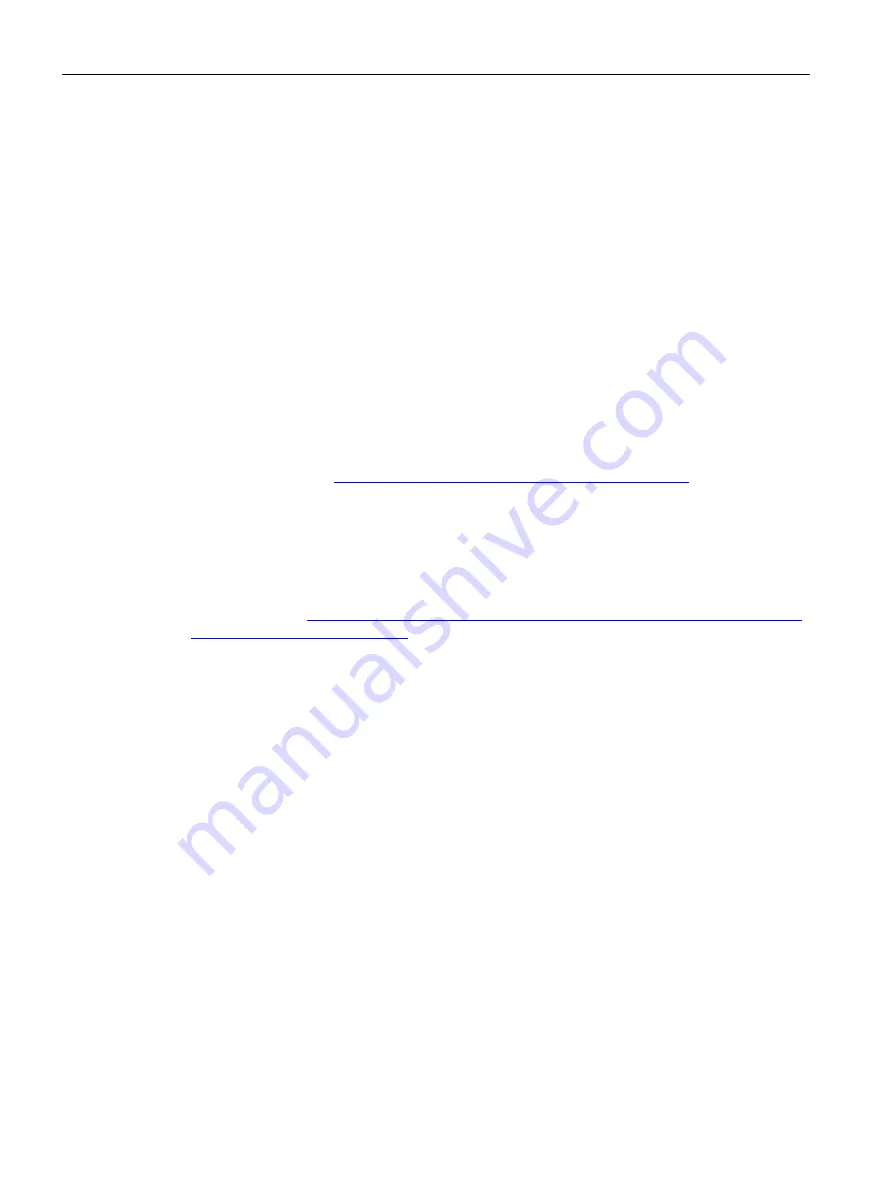
Appendix
A.2 Returns
Set CEM CERT
118
Operating Instructions, 06/2021, A5E34491309-12
Decontamination declaration
With this declaration you confirm "that the device/spare part has been thoroughly
cleaned, is free of residues, and that the device/spare part represents no danger for
mankind and environment."
If the returned device/spare part has come into contact with poisonous, corrosive,
flammable or polluting substances, you must thoroughly rinse, clean and neutralize the
device/spare part before returning it, in order to ensure that all hollow areas are free of
hazardous substances. Check the item after it has been cleaned.
SIEMENS will return devices or spare parts to you at your expense if a decontamination
declaration is not included.
SIEMENS will only service returned products or spare parts if this decontamination
declaration is enclosed which confirms that the products or spare parts have been
correctly decontaminated and are therefore safe to handle. The decontamination
declaration must be visibly attached to the outside of the packaging in a firmly secured
transparent document bag.
A form for the Declaration of Decontamination is available from Services & Support
Services & Support (
https://support.industry.siemens.com/cs/gb/en/sc
A.2.2
Return address
For quick identification and elimination of causes of error, we ask you to return the
devices. The return address responsible for your location can be found here:
Return address (
https://www.automation.siemens.com/mcms/aspa-db/en/automation-
Summary of Contents for Set CEM CERT
Page 1: ......
Page 2: ......
Page 8: ...Table of contents Set CEM CERT 6 Operating Instructions 06 2021 A5E34491309 12 ...
Page 44: ...Commissioning 7 2 Commissioning Set CEM CERT 42 Operating Instructions 06 2021 A5E34491309 12 ...
Page 112: ...Technical specifications Set CEM CERT 110 Operating Instructions 06 2021 A5E34491309 12 ...
Page 122: ...Appendix A 2 Returns Set CEM CERT 120 Operating Instructions 06 2021 A5E34491309 12 ...