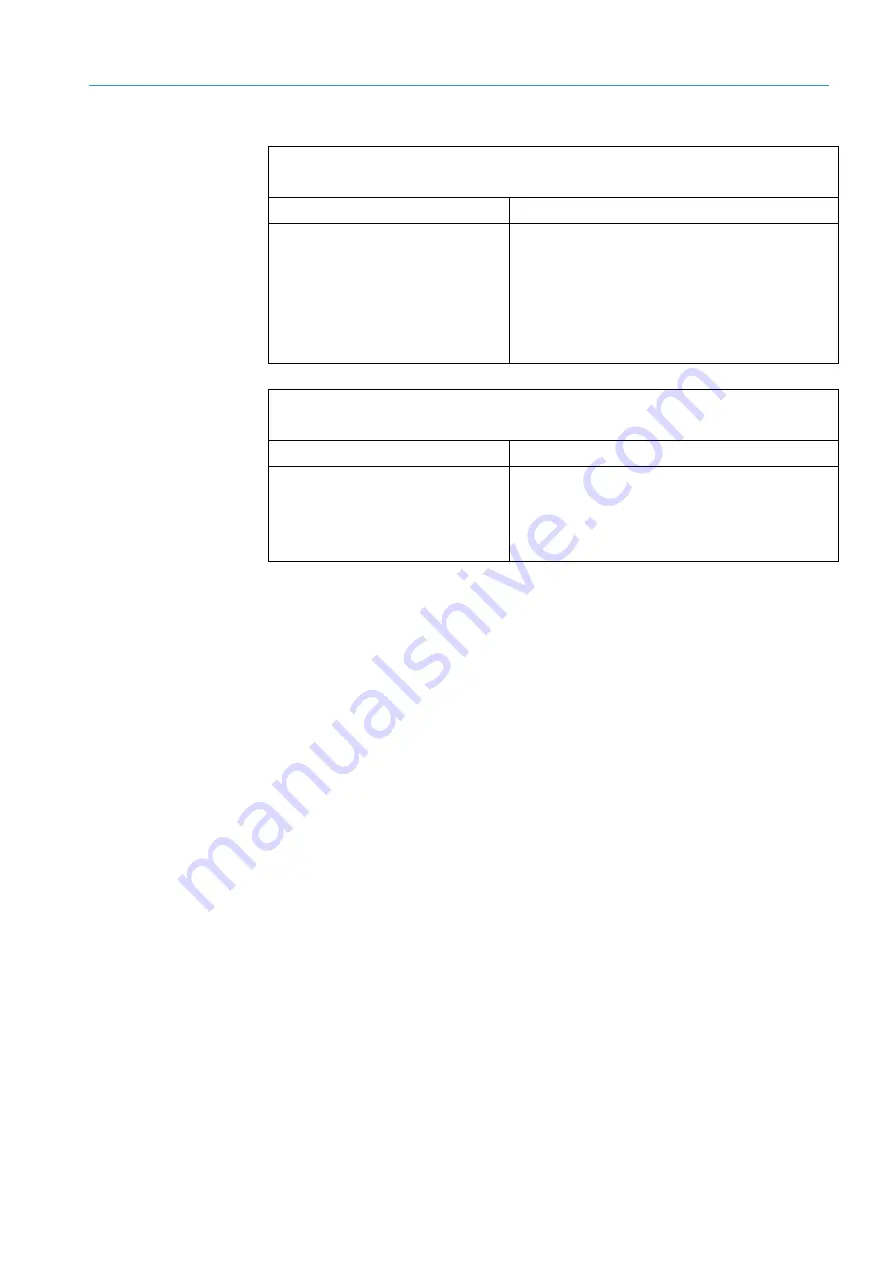
FAULT DIAGNOSIS
8
117
8026365/V1-0/2022-03|SICK
Subject to change without notice
S U P P L E M E N T A R Y O P E R A T I N G I N S T R U C T I O N S | VMS4200-x/5200-x MID
8.1.4
Fault indication on the photoelectric sensor array
Fault indication
Green LED does not light up or flickers.
Fault cause
Possible solution to the problem
Sensor is still ready for operation,
but the operating conditions are
not ideal (operating reserve factor
between 0.9 and 1.1)
▸
Check the operating conditions.
▸
Fully align the light beam (light spot) with the
reflector.
▸
Clean the optical surfaces (sensor and
reflector).
▸
Readjust the sensitivity (potentiometer)
Fault indication
Green LED does not light up.
Fault cause
Possible solution to the problem
No voltage or voltage below the
limit values
▸
Check the voltage supply, check all electrical
connections (cables and plug connections).
▸
Establish a stable voltage supply.
▸
Sensor is defective. Replace the sensor.
Tab. 20: LED display in the event of a fault with the photoelectric sensor of the array