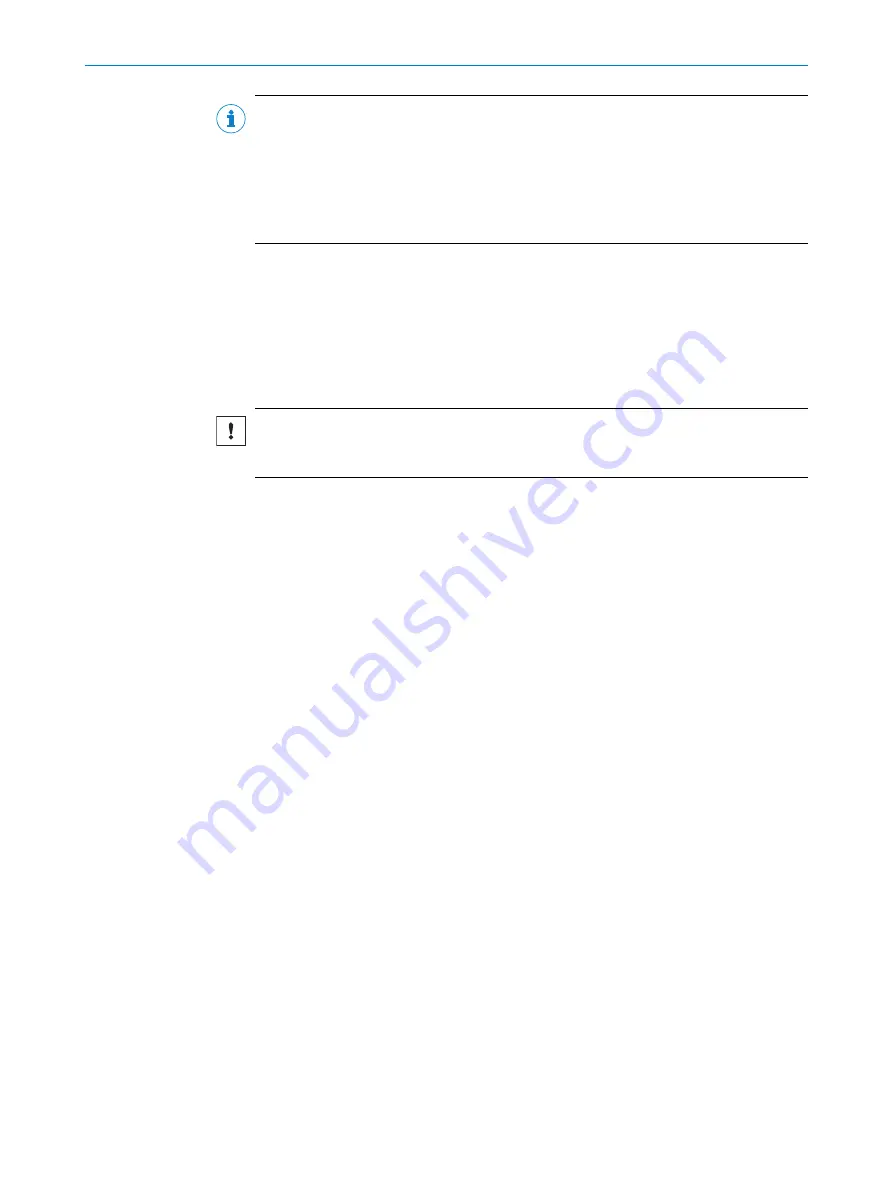
NOTE
All necessary components influence the parameters of the entire application that relate
to safety technology. The components must therefore have a MTTF
d
value that is suit‐
able for the entire application and satisfies the necessary performance level. The nec‐
essary performance level results from the risk assessment. For evaluating the perfor‐
mance level achieved, subsystems for SISTEMA are available under:
3.4.1
Requirements for hold to run device
The pushbutton must be installed outside of the hazardous area. From the position of
the pushbutton, there must be a complete view of the hazardous area. It must not be
possible for a person to enter the hazardous area while activating the pushbutton.
The pushbutton must be designed according to the following standard:
•
EN 60204
NOTICE
The pushbutton should only be operable by authorized personnel. An example of a mea‐
sure to prevent unauthorized use is a key-operated spring-back pushbutton.
The hold to run device is supplied via test output X2 of the XTIO module, which it is con‐
nected to. Test output X2 of this module must not be used for other devices.
3.4.2
Reset pushbutton requirements
Reset pushbutton requirements
The pushbutton must be installed outside of the hazardous area. From the position of
the pushbutton, there must be a complete view of the hazardous area. Activating the
pushbutton must not initiate any movement of the machine.
The reset pushbutton must be designed in accordance with the following standard:
•
EN 60204
Complementary information
The reset pushbutton resets the muting function of the safety system. If the reset push‐
button is also to be used to reset the machine, the risk assessment must show that
there is no possibility of this causing a hazard.
3.4.3
Requirements for Flexi Soft safety controller
The Flexi Soft safety controller must be installed in a control cabinet with an enclosure
rating of IP 54.
Please note the following for installation:
•
Continuous equipotential bonding via conductive connections between machine
parts and systems
•
Physically separate supply unit (voltage supply/actuator systems/inverter)
•
Do not use the shielding to conduct equipotential bonding current
•
Keep the shielding short and use the full surface
•
Use every existing or available functional earth (FE)
•
Carefully connect all available communications cables. Twisted lines are often nec‐
essary for fault-free data transmission (fieldbus).
The voltage supply for the main module and each expansion module for input and out‐
put must be limited to a maximum of 4 A, either by the power supply unit or by a fuse.
3
PRODUCT DESCRIPTION
12
O P E R A T I N G I N S T R U C T I O N S | Safe Entry Exit
8021675/ZV26/2019-05-13 | SICK
Subject to change without notice