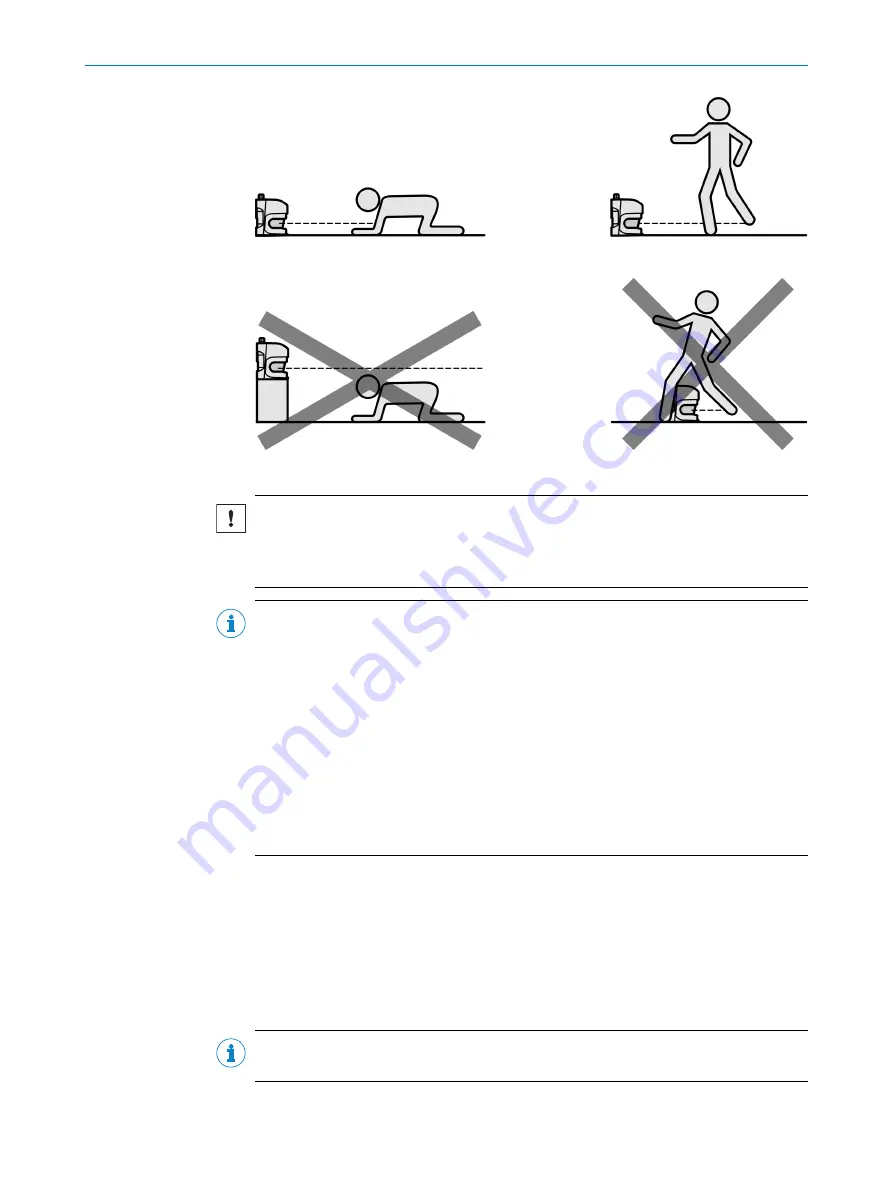
Figure 16: Prevent crawling beneath, standing behind, or climbing over
NOTICE
b
Mount the device in a dry location. Protect it from contamination and damage.
b
Avoid installing the device near strong electrical fields. These fields can be caused,
for example, by nearby welding cables, induction cables, or cell phones.
NOTE
b
Mount the device so that it is protected from moisture, dirt, and damage.
b
Mount the sensor so that the status indicators can be clearly seen.
b
Always mount the device so that there is still enough space for mounting and dis‐
mantling the system connector.
b
Avoid exposing the device to excessive shock and vibration.
b
For systems that vibrate heavily, use shock absorbers to prevent the possibility of
fixing screws unintentionally coming loose.
b
Regularly check the tightness of the fixing screws.
b
Observe the maximum permissible tightening torque for the fixing screws on the
device:
°
M6 at the rear = max. 12 Nm
°
M8 on the side = max. 16 Nm
Further topics
•
4.3.1
If several safety laser scanners are used
The device has been designed to minimize the probability of mutual interference with
other safety laser scanners. To completely rule out unintended shutdowns, the safety
laser scanners must be mounted as shown in the following examples.
NOTE
To calculate the minimum distance for any particular case, refer to ISO 13855.
PROJECT PLANNING
4
8013291/ZA19/2019-11-14 | SICK
O P E R A T I N G I N S T R U C T I O N S | S3000 PROFINET IO, S3000 PROFINET IO-OF
29
Subject to change without notice