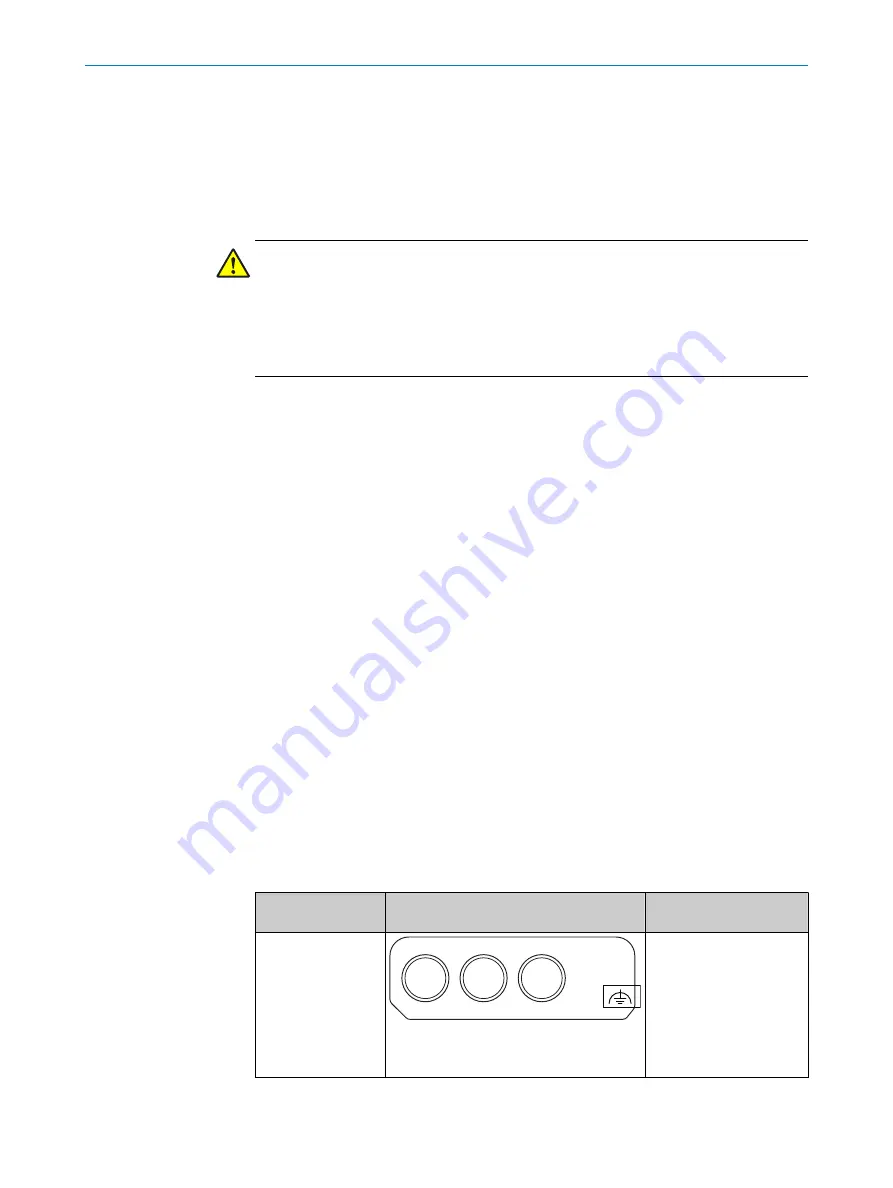
5
Electrical installation
5.1
Important notes
Information on the requirements that must be met for safe integration of the localiza‐
tion controller and 2D LiDAR sensors into the control and electronics of the machine,
see the corresponding operating instructions.
DANGER
Hazard due to electrical voltage
Hazard due to unexpected starting of the machine
b
Make sure that the machine is (and remains) disconnected from the power supply
during the electrical installation.
b
Make sure that the dangerous state of the machine is (and remains) switched off.
b
Carry out the electrical installation work in conformity with EN 60204-1.
b
Use suitable power supply.
b
Check that all earthing points are connected with the same ground potential.
b
Connect the shielding of all data lines (Ethernet, CAN, serial) directly to the func‐
tional earth (FE) at the control cabinet entry point.
5.2
MicroScan3
The electrical installation is described in detail in the operating instructions:
•
8021911
The examples are given for microScan3 EFI-pro variant but are also applicable for Ether‐
Net/IP™ and PROFINET.
5.2.1
Electrical setup
Supply voltage and power consumption
Supply voltage:
•
24 V DC (16.8 … 30 V DC) (SELV/PELV) according to IEC 60364441
•
Must be able to bridge a brief power outage of 20 ms with a starting voltage of
≤ 3 A
The microScan3 consumes the following:
•
Power consumption ≤ 11 W (typ. 7.2 W)
•
Power consumption Standby typical 7 W
System plug and connections
Table 2: Position of the electrical connections
Safety laser scan‐
ners
Suitable system plug
Plug connector
microScan3 – Ether‐
Net/IP™
XD1
XF1
XF2
MICSX-BANNZZZZ1 (part number:
2086102)
•
XD1: voltage supply,
•
XF1, XF2: 2 × Ethernet
for EtherNet/IP –
CIP Safety, data output,
configuration, and diag‐
nostics.
5
ELECTRICAL INSTALLATION
10
T E C H N I C A L I N F O R M A T I O N | LiDAR Localization Hardware Integration
8024819/2019-09-02 | SICK
Subject to change without notice