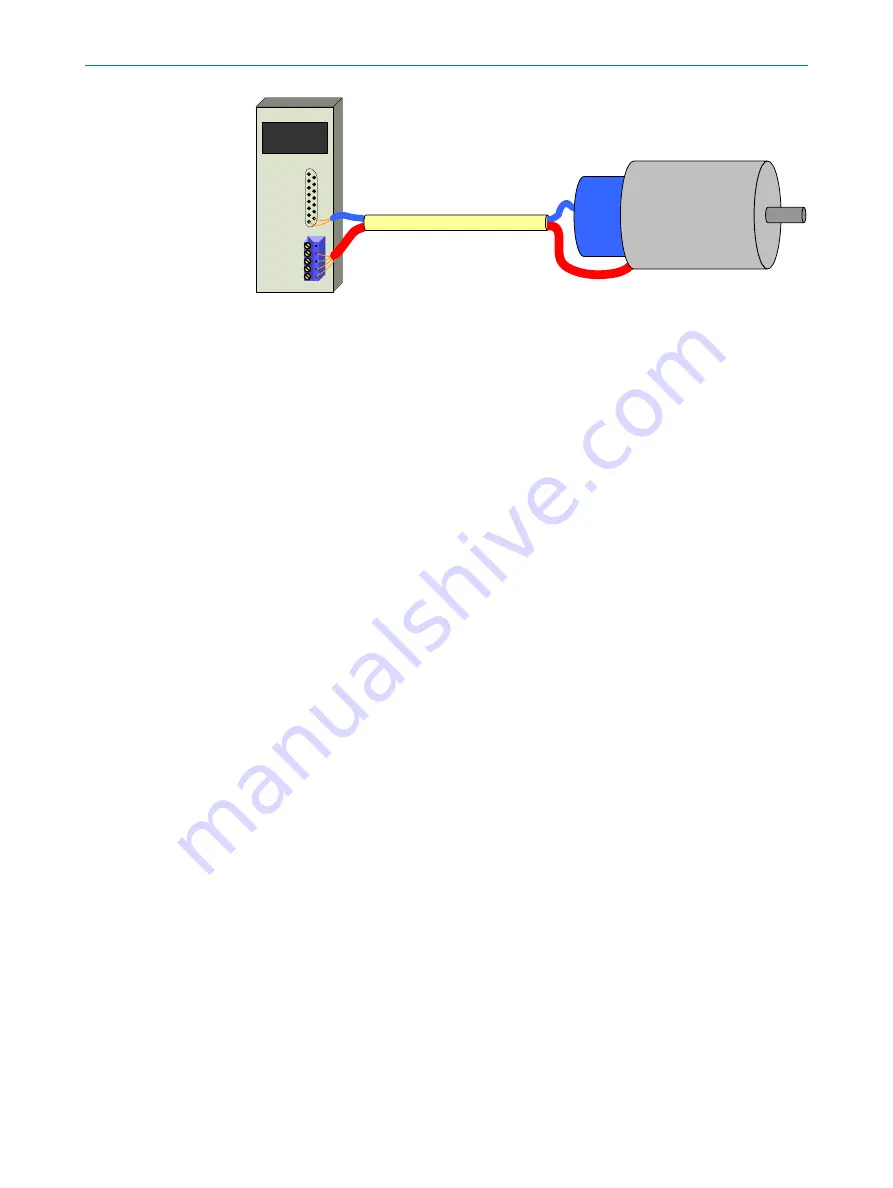
Drive
OK …
DSL connection
MFB
system
Motor
Figure 1: Drive system with HIPERFACE DSL
®
Based on the name for the predecessor protocol, the SICK HIPERFACE
®
, the name
HIPERFACE DSL
®
stands for HIgh PERformance InterFACE Digital Servo Link.
This interface takes into account all the current requirements of digital motor feedback
systems and also contains future enhancements for the manufacturers of frequency
inverters.
2.4
Features of HIPERFACE DSL
®
Some of the main advantages of HIPERFACE DSL
®
are based on the opportunity for
connection of the encoder:
•
A digital interface on the frequency inverter for all communication with the motor
feedback system. The interface complies with the RS485 standard with a transfer
rate of 9.375 MBaud.
•
Communication with the encoder via a twisted pair
•
Power supply and communication with the encoder can be carried out using the
same dual cable. This is possible by the enhancement of the frequency - inverter
with a transformer.
•
The connection cables to the encoder can be routed as a shielded, twisted- pair
cable in the power supply cable to the motor. This means that no encoder plug
connector to the motor and to the frequency inverter is necessary.
•
The cable length between the frequency inverter and the motor feedback system
can be up to 100 m, without degradation of the operating performance.
The digital HIPERFACE DSL
®
protocol can be used for a variety of frequency inverter
applications:
•
For the feedback cycle of the frequency inverter's synchronous cyclic data that
enables synchronous processing of position and rotation speed of the encoder.
•
Shortest possible cycle time: 12.2 µs.
•
Transmission of the safe position of the motor feedback system with a maximum
cycle time of 216 µs.
•
Redundant transmission of the safe position of the motor feedback system with a
maximum cycle time of 216 µs, so that suitable motor feedback systems can be
used in SIL2 applications (in accordance with IEC 61508).
•
Transmission of the safe position of the motor feedback system on a second chan‐
nel with a maximum cycle time of 216 µs, so that suitable motor feedback sys‐
tems can be used in SIL3 applications (in accordance with IEC 61508).
SCOPE OF APPLICATION OF THE DOCUMENT
2
8017595/ZTW6/2018-01-15 | SICK
T E C H N I C A L I N F O R M A T I O N | HIPERFACE DSL
®
7
Subject to change without notice