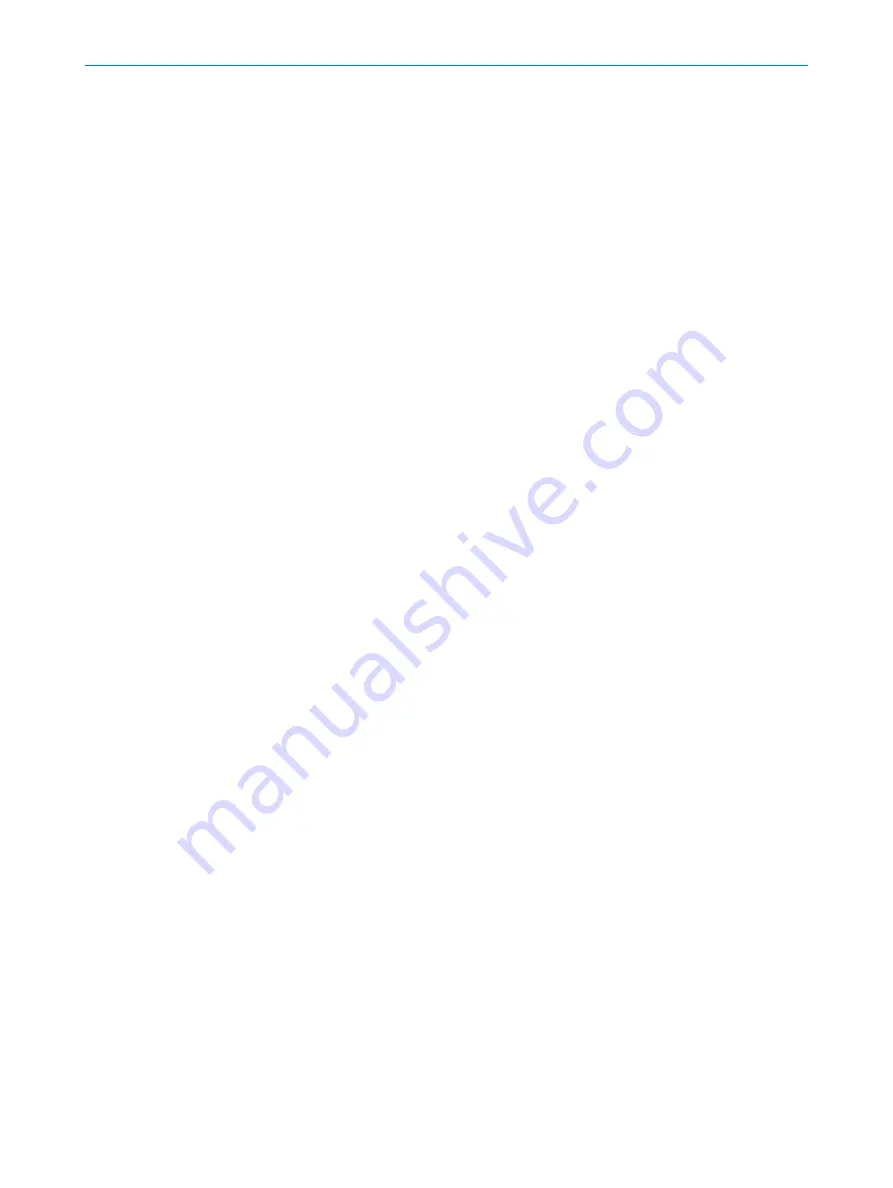
For the exact meaning for the content of these register and threshold values please
refer to
. The signal propagation delay within
the connection line will be adjusted within the HDSL-protocol frame in steps of approx.
106 ns (~10m-steps). Intended connection lengths shall be configured and tested.
Results can be compared with the content of the DELAY-register.
EMC noise impact:
With an oscilloscope and differential probes the EMC noise level on the HDSLlines can
be checked. The probes are initially connected at the HDSL-inlet point at the servo con‐
troller. Tests can be done during different servo controller operation modes like acceler‐
ation, deceleration, stand still, reverse cycling at free running or with motor load.
10.4
Recommendations on installation site
As mentioned within
also external conditions influence the proper func‐
tion of the HDSL-system. Depending on foreseeable target applications known condi‐
tions can be considered during the system design process. Nevertheless the conditions
can vary significantly between different installations sites. By reason of the great variety
of different conditions there are no single HDSLsystem configuration which will fit all
needs. In such cases the differences need to be assessed and the HDSL-system config‐
uration can be adjusted to particular requirements. The two important external impacts
to the HDSL-system performance are
•
The power supply and grounding conditions
•
Application changes and field modifications
10.4.1
Power supply and grounding conditions
Most power supply ratings for current HDSL-servo motor applications are either 400
VAC/3~ or 480 VAC/3~. The difference between these two level leads to a different
level of DC voltage for PWM controlling of the motors of either approx. 570 VDC or
approx. 700 VDC. In combination with different rising edges for the PWM this leads to
significant different EMC conditions especially within the connection line between the
servo controller and the motor. This needs to be considered when adapting a HDSLsys‐
tem configuration for one power supply system to the other one. The impact of the
grounding condition is caused either by insufficient contact qualities or wire sizes. It
leads to noise reflections instead of noise draining. Depending on noise frequencies
and cable lengths it can amplify noise amplitudes up to a disturbing level. Large dis‐
tances between controller and motor location or different ground connections points
can cause ground loops.
10
DSL COMPONENT INTEROPERABILITY
168
T E C H N I C A L I N F O R M A T I O N | HIPERFACE DSL
®
8017595/ZTW6/2018-01-15 | SICK
Subject to change without notice