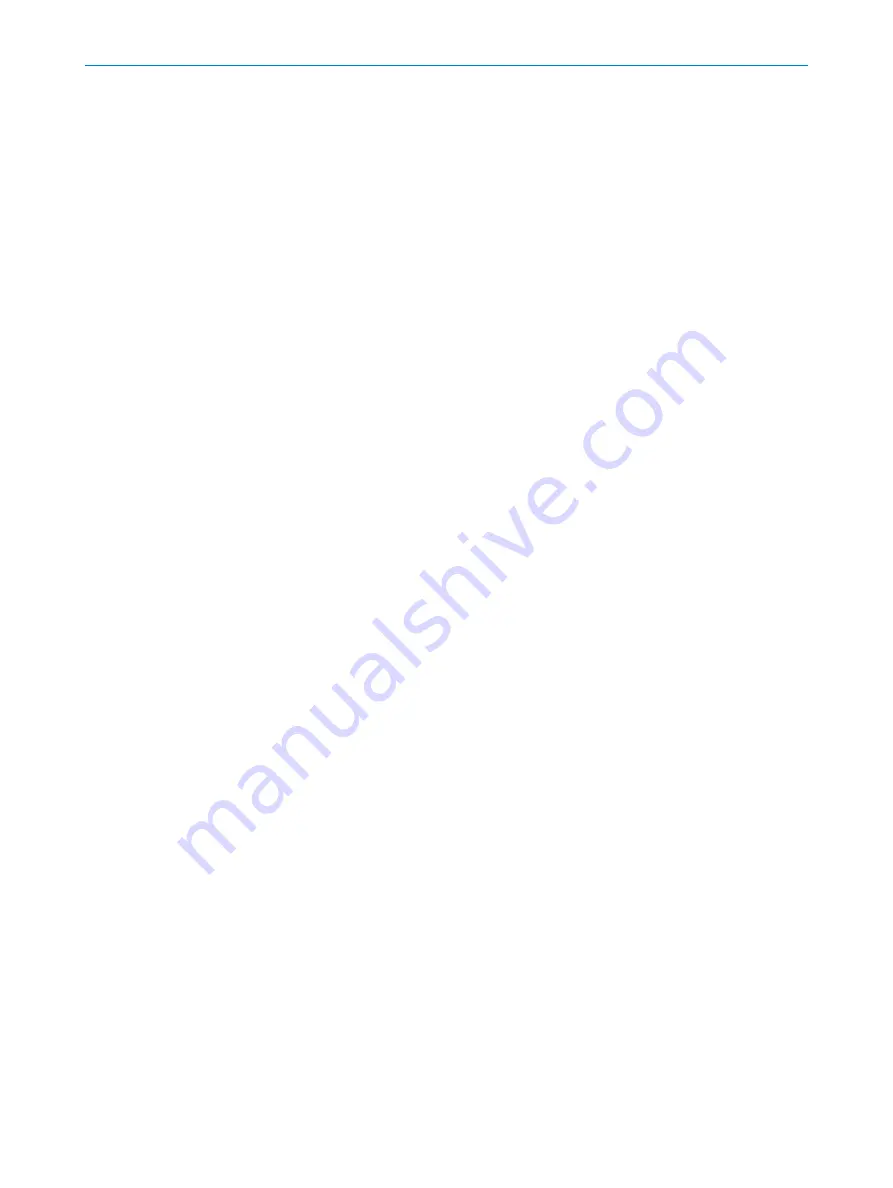
By reading these information the servo controller can automatically configure a stan‐
dard motor controlling performance with the actual connected motor. The HDSL
encoders provided an EEPROM storage area of 8 kByte for external usage organized by
file system. In this case several files can be stored there. Access to this storage area is
provided by different resources.
•
“MAKEFILE” – RID 133h – create, delete, change file
•
“LOADFILE” – RID 130h – load an existing file for access
•
“RWFILE” – RID 131h – read or write access
•
“FILESTAT” – RID 132h – information about access rights and file size
•
“DIR” – RID 134h – provides the list of existing files
For further information of the file handling please refer to section
10.2.6
Verification
For the proper encoder assembling a visual inspection is done. In case of problems
(vibrations, e.g.) acceleration sensors can be placed on the encoder and the vibration
level can be checked (in reference to the limits shown within the product information).
To check the proper mounting of the encoder to the motor shaft an external reference
encoder is used. Its position information is compared to them of the encoder within the
motor. If a potential deviation between the two positions data exceeds a certain limit
the encoder mounting needs to be checked and reworked if necessary. The proper
shielding and grounding is tested with an oscilloscope and differential probes during
different drive modes and observing the EMC noise coupling or disturbances on the
data lines.
10.3
Recommendations for connection line
The connection line part within the system configuration contains the cable between
the servo controller connection point and the motor connector as well as potential cou‐
plings within the line.
10.3.1
Cable
The combination of data lines and motor power lines within one cable is done with the
so-called hybrid cable type. Herein the data lines are protected against electromagnet‐
icdisturbances by different measures as good as possible. To be suitable for a stable
and reliable HDSL-communication the cable need to fulfill certain criteria.
Within [Whitepaper Vers. 2-03; Doc. 8018816] the basic cable performance require‐
ments are listed. Nowadays more or less all bigger cable manufacturer and supplier
have one or morehybrid cable types within their product portfolio. When choosing a par‐
ticular cable the manufacturer data need to be compared with the requirements, listed
within [Whitepaper Vers. 2-03; Doc. 8018816].
Further criteria for the cable selection are listed within [Whitepaper Vers. 1-04; Doc.
8018817]. These criteria are mainly driven by requirements and conditions of the dif‐
ferent installation sites (environmental and legal issues, e.g.).
10.3.2
Couplings
Couplings are installed to separate different equipment sections from each other
mainly for shipment and installation purposes. At coupling points the cable needs to be
opened. Thereby all the measures to protect the data line have no longer any effect.
The general recommendation is to avoid couplings within the connection line. If cou‐
pling points are necessary the number shall be kept as low as possible – one should be
suitable for most of the cases. Requirements for couplings:
10
DSL COMPONENT INTEROPERABILITY
166
T E C H N I C A L I N F O R M A T I O N | HIPERFACE DSL
®
8017595/ZTW6/2018-01-15 | SICK
Subject to change without notice