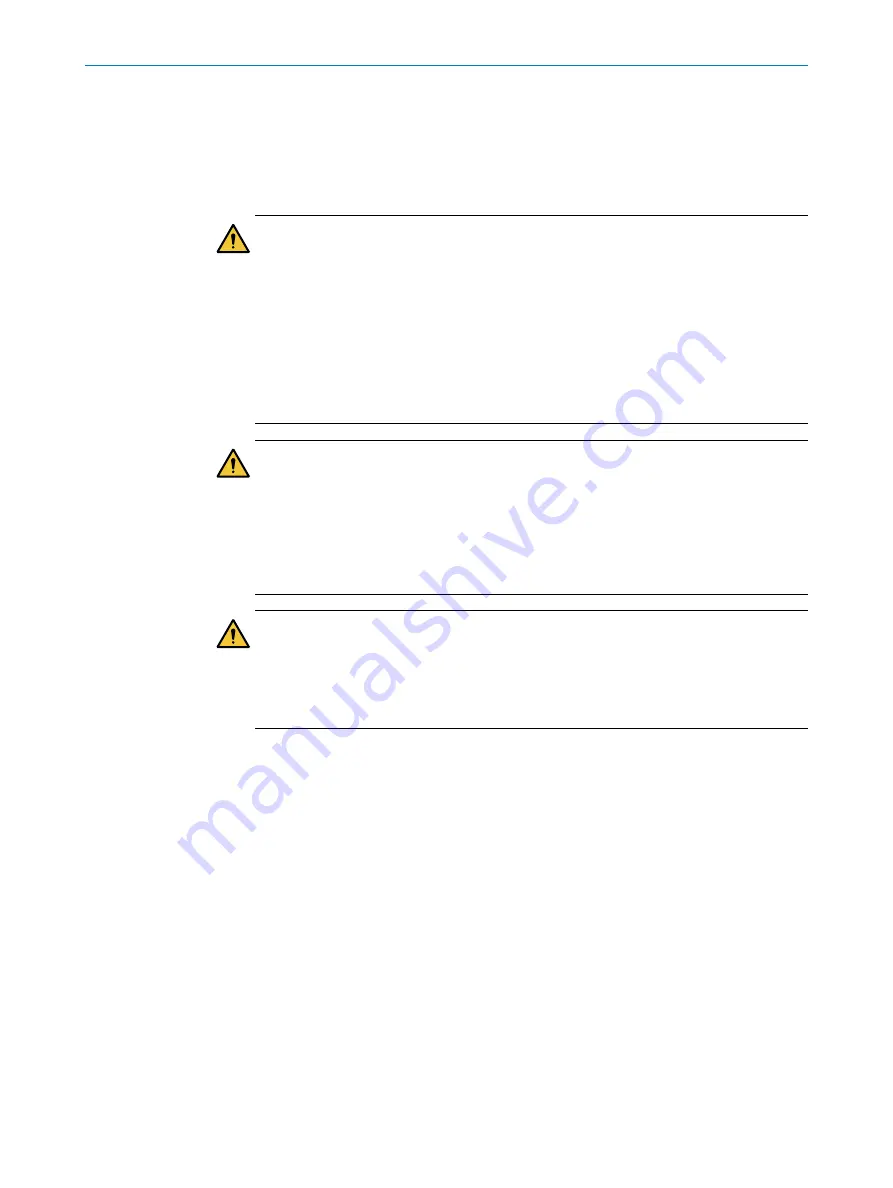
6
Electrical installation
6.1
Safety
Important information
DANGER
Hazard due to electrical voltage
Hazard due to unexpected starting of the machine
b
Make sure that the machine is (and remains) disconnected from the voltage
supply during the electrical installation.
b
Make sure that the dangerous state of the machine is (and remains) switched off
during electrical installation.
b
Make sure that the outputs of the safety light curtain have no effect on the
machine during the electrical installation work.
b
Use a suitable voltage supply.
DANGER
Hazard due to lack of effectiveness of the protective device
The dangerous state may not be stopped in the event of non-compliance.
b
Always connect the two OSSDs separately. The two OSSDs must not be connected
to each other.
b
Connect the OSSDs such that the machine controller processes both signals
separately.
DANGER
Hazard due to lack of effectiveness of the protective device
The dangerous state may not be stopped in the event of non-compliance.
b
Prevent the formation of a potential difference between the load and the protec‐
tive device.
Prerequisites
•
The safety light curtain has been safely integrated into the control system and the
electrical system of the machine.
•
Mounting has been correctly executed.
ELECTRICAL INSTALLATION
6
8014276/1DCM/2022-10-27 | SICK
O P E R A T I N G I N S T R U C T I O N S | deTec2 Core
41
Subject to change without notice