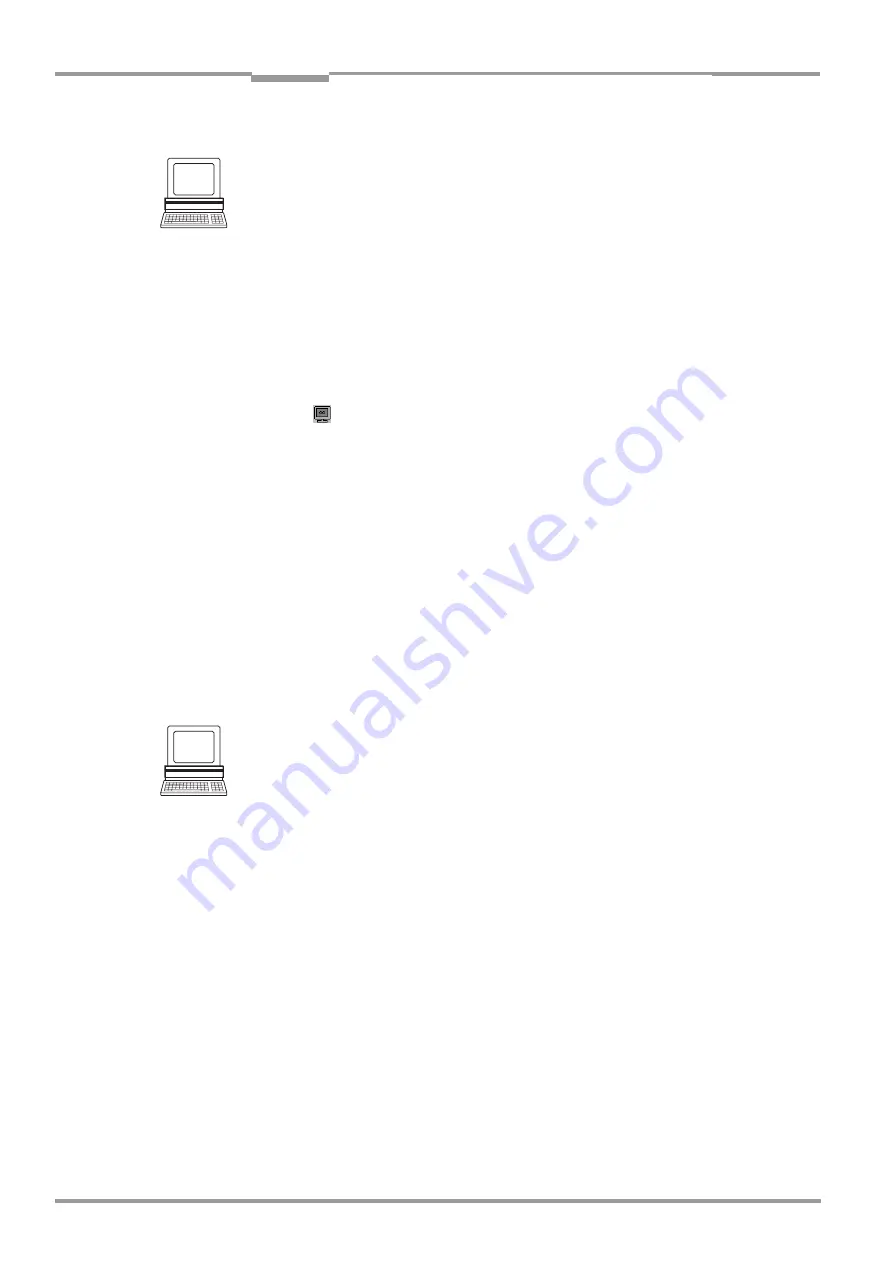
Chapter
6
Operating Instructions
CLV 490 Bar Code Scanner
6-42
©
SICK AG · Division Auto Ident · Germany · All rights reserved
8 009 993/O824/20-12-2004
Operation
Triggering the reading pulse via the Terminal Emulator
In the default setting the "Sensor" switching input is the (external) trigger source of the
reading pulse. The reading pulse can also be triggered directly via the Terminal Emulator of
CLVSetup for test purposes. To do so, a different trigger source must be selected
temporarily in the CLV.
1.
Choose D
EVICE
C
ONFIGURATION
tab.
2.
In the R
EADING
T
RIGGER
M
ODE
section click the S
ERIAL
I
NTERFACE
option.
3.
Perform a download to the CLV.
To do so, click the S
ERIAL
I
NTERFACE
option again with the right mouse button and choose
D
OWNLOAD
P
ARAMETER
in the context menu.
CLV-Setup copies the parameter to the CLV temporarily.
The serial interface has been activated as the trigger source of the reading pulse and
is ready to receive appropriate commands (until the CLV is switched off).
4.
Click
in the toolbar.
The Terminal Emulator window is then displayed.
The CLV is in the Reading mode.
5.
Click the SW-T
RIGGER
O
N
button or press [F7].
CLV-Setup sends a start command to the CLV.
The "Sensor" LED lights up and the red scan line appears.
6.
Present the bar code pattern from
to the CLV.
7.
Click the SW-T
RIGGER
O
FF
button or press [F8].
CLV-Setup sends a stop command to the CLV. The "Sensor" LED is extinguished. The
CLV switches off the laser diode. The CLV displays the reading result in the output
window of the Terminal Emulator. The "Read Result" LED lights up for a duration of
100 ms (default setting).
6.5.2
Percentage evaluation
In the Percentage evaluation mode, the quality of the reading function is assessed (no
conveyor movement).
The CLV performs continuously 100 scans in the free running mode and evaluates the
reading quality. It outputs the reading result every 2 s via the
terminal interface
. The
reading results can be displayed in the Terminal Emulator of CLV-Setup. The "Result 1" to
"Result 4" switching outputs do not become live in the Percentage evaluation mode.
The
standard
decoder
has to be set temporarily for the percentage evaluation.
The Percentage evaluation mode can be called up by choosing V
IEW
in the menu bar, as a
device function via CLV 490 (interactively), or via the Terminal Emulator.
Note
Autofocus mode:
If the CLV operates with autofocus in stand-alone configuration, the Percentage evaluation
mode can only be started in the Autofocus mode "Minimum distance" or "Differential
background". The CLV fixes the timeout of the automatic focus position switchover to 30
ms, the preferred focus position is set to the last recognised object.
If the CLV operates with autofocus in OTS mode ("Differential background and tracking"),
the CLV switches automatically to the autofocus mode "Differential background“ during the
the Percentage evaluation mode.