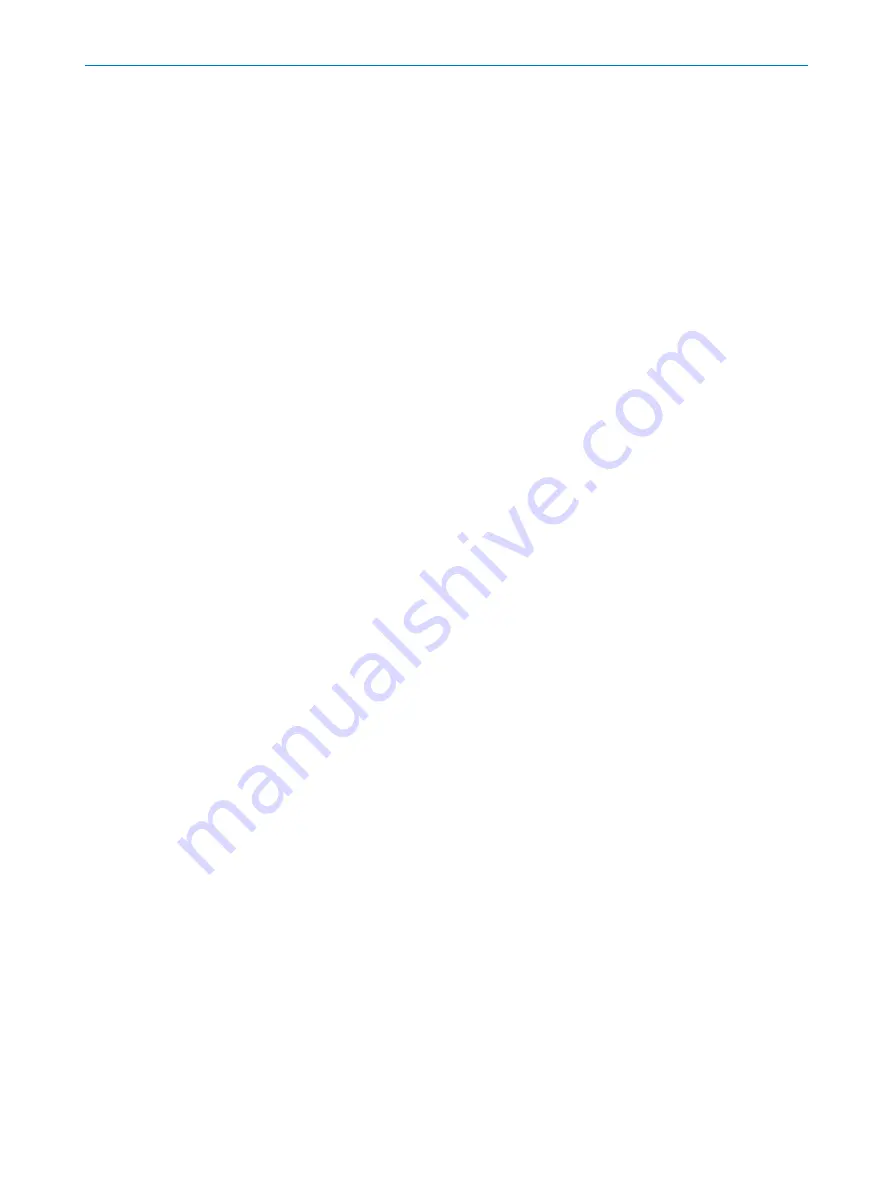
4
Project planning
4.1
Needs-based cleaning using the airWiper
Overview
To enable the airWiper to clean the optics cover using compressed air when required,
valves are located between the compressed air supply and the airWiper. A controller
opens the valves when cleaning is required. The controller can open the valves on
manual request or on a signal from the safety laser scanner.
The airWiper can only clean the optics cover effectively if the pressure system and the
activation are tailored to the specific requirements. The following examples serve as
a guide. You need to adapt the examples to the application and the compressed air
supply used, and optimize them in a targeted manner.
Prerequisites
•
The safety laser scanner is mounted with the optics cover facing down.
•
The safety laser scanner is protected from the ambient conditions during opera‐
tion. It is protected by the weather protection hood or by mounting it in a cladding,
as described in the operating instructions of the safety laser scanner.
•
The safety laser scanner is mounted so that no small objects (e.g., cables) are in
the protective field, even if the safety outputs do not switch to the OFF state as a
result.
•
There are no objects (e.g., cables) between the base and the curved part of the
optics cover that could interfere with the contamination measurement.
•
The requirements on the compressed air are met,
.
Automatic cleaning operation
You can use signals from the safety laser scanner to trigger the cleaning.
The safety laser scanner continuously measures the contamination of the optics cover.
You can use the signals
Contamination warning
and
Contamination error
to trigger the
airWiper. In addition to or instead of this, warning fields can serve as triggers.
You can evaluate the signals of the safety laser scanner using a controller. The control‐
ler activates the compressed air for the individual channels via valves. In the case of
the outdoorScan3 Core I/O, you can also directly control individual components such as
relays and valves without a controller. The electrical data of the outdoorScan3 Core I/O
can be found in its operating instructions.
Two stage cleaning
Two-stage cleaning is particularly effective in many cases and requires less compressed
air than single-stage cleaning. In two-stage cleaning, channel A first cleans the base.
Channel B is then additionally activated so that both channels clean the base and
the curved part of the optics cover together. This two-stage cleaning step is usually
repeated several times in one cleaning operation.
Stop criteria and exclusion conditions
If the airWiper is triggered automatically, then in many cases it is useful to define stop
criteria and exclusion conditions.
The cleaning process ends as soon as the triggering signal is no longer present or as
soon as the stop criterion occurs.
PROJECT PLANNING
4
8027429/2022-05-20 | SICK
O P E R A T I N G I N S T R U C T I O N S | airWiper
11
Subject to change without notice