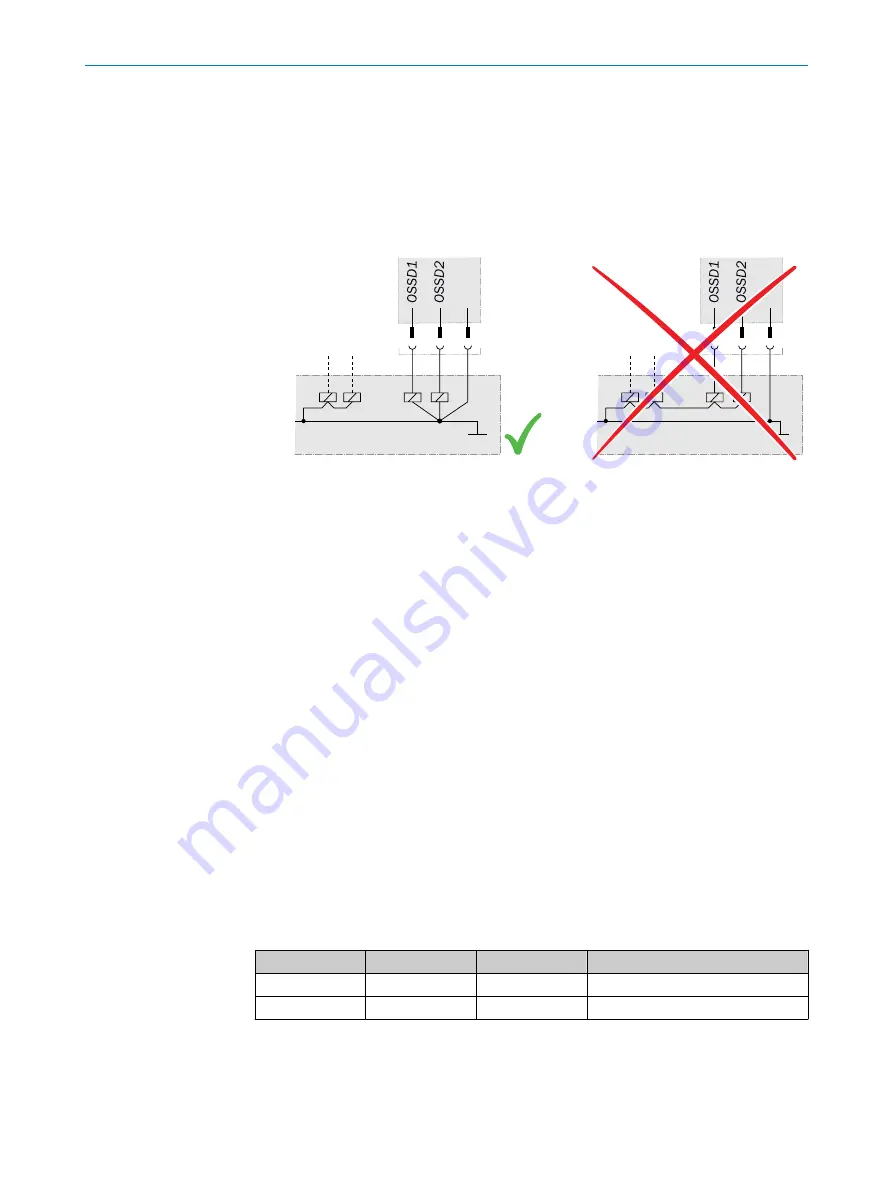
•
No potential difference can occur between the load and the protective device. The
0 V connections of the load and those of the associated protective device are
connected individually and directly to the same 0 V terminal strip. In the event of
a fault, this is the only way to ensure that there can be no potential difference
between the 0 V connections of the loads and those of the corresponding protec‐
tive device. This is particularly important for loads that switch even if they are
activated with negative voltage (e.g. electromechanical contactor without reverse
polarity protection diode).
Figure 19: No potential difference between load and protective device
NPN mode
When the protective field is clear, the OSSDs signal the ON state and the signal level
is LOW. If there are objects in the protective field or a safe multibeam scanner error
occurs, the OSSDs signal the OFF state with the HIGH signal level.
4.4.3
Static control inputs
Overview
The safe multibeam scanner has three static control inputs (IN 1, IN 2, IN 3). The static
control inputs accept signals for switching between different monitoring cases.
Prerequisites
•
The safety-related parts of the control which switch the active protective field
provide the same safety level as the safety function. In many cases, this is PL c as
per ISO 13849-1 or SIL 1 as per IEC 62061.
Signals for the monitoring cases
If only one monitoring case is configured for the safe multibeam scanner, the input
signals are not evaluated and the monitoring case is permanently active.
If exactly two monitoring cases are configured for the safe multibeam scanner, only the
input signals on the static control inputs IN 1 and IN 2 are evaluated.
Table 5: Valid combinations of input signals for two monitoring cases
IN 1
IN 2
IN 3
1
0
Not evaluated
1
0
1
Not evaluated
2
If three or four monitoring cases are configured for the safe multibeam scanner, the
input signals are evaluated on all static control inputs IN 1, IN 2 and IN 3.
4
PROJECT PLANNING
30
O P E R A T I N G I N S T R U C T I O N S | scanGrid2 I/O
8025936/2021-01-08 | SICK
Subject to change without notice