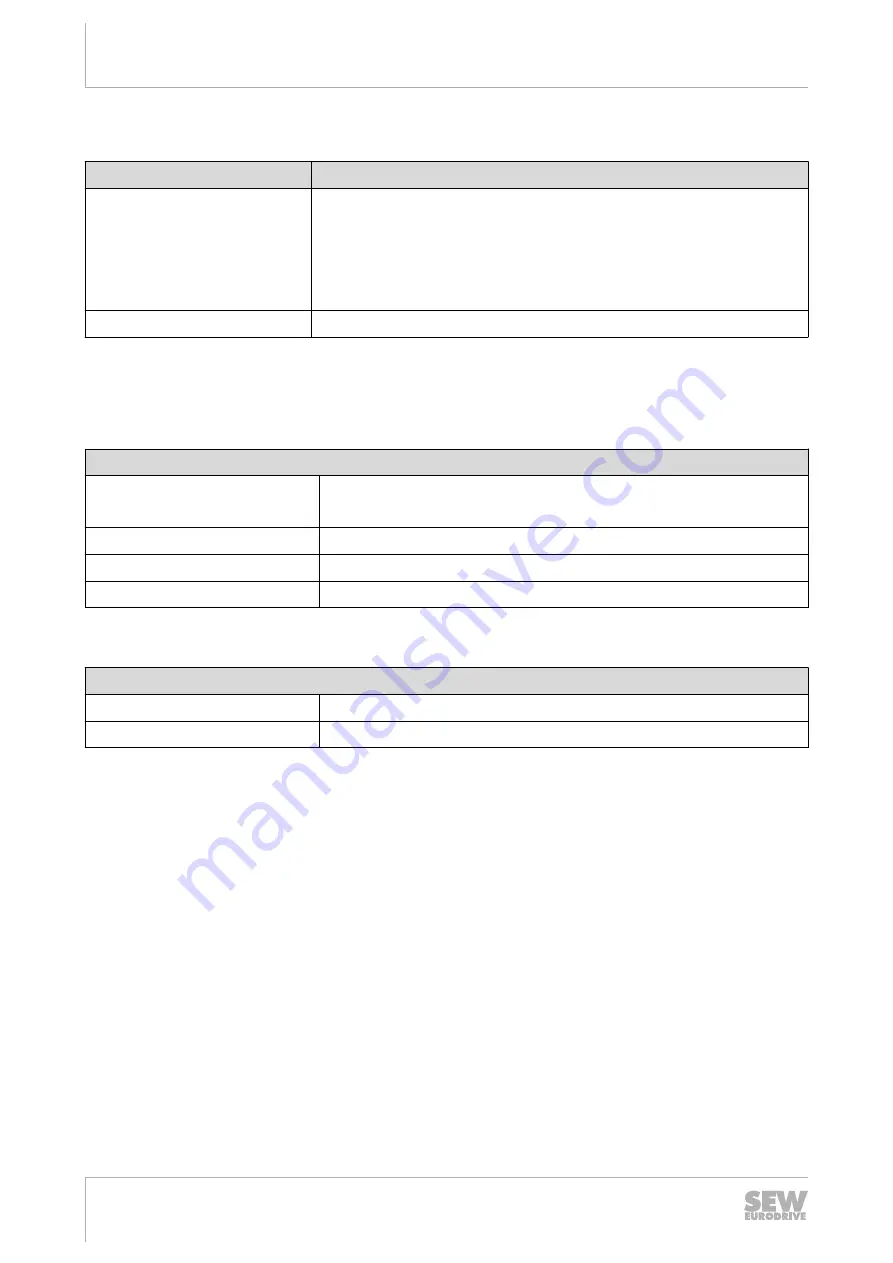
9
Technical data
Binary output DB00
Operating Instructions – MOVIFIT
®
FC
182
9.7
Binary output DB00
Digital output
Output type
PLC-compatible to EN 61131-2, interference voltage proof and short-cir-
cuit-proof
Rated current
Leakage current
Internal voltage drop
150 mA
max. 0.2 mA
max. 2 V
Potential reference
24V_C
9.8
Interfaces
9.8.1
SBus interface
SBus
SBus interface
(not with function level "Classic")
Interface to other SBUS-capable SEW units
CAN bus to CAN specification 2.0, parts A and B
Connection technology
Terminals M12
Transmission technology
according to ISO 11898
Bus termination
120 Ω terminating resistor, can be activated using DIP switch S3
9.8.2
RS485 interface
RS485
RS485 interface
Diagnostic interface, not electrically isolated from MOVIFIT
®
electronics
Connection technology
RJ10 socket
21316996/EN – 12/2014