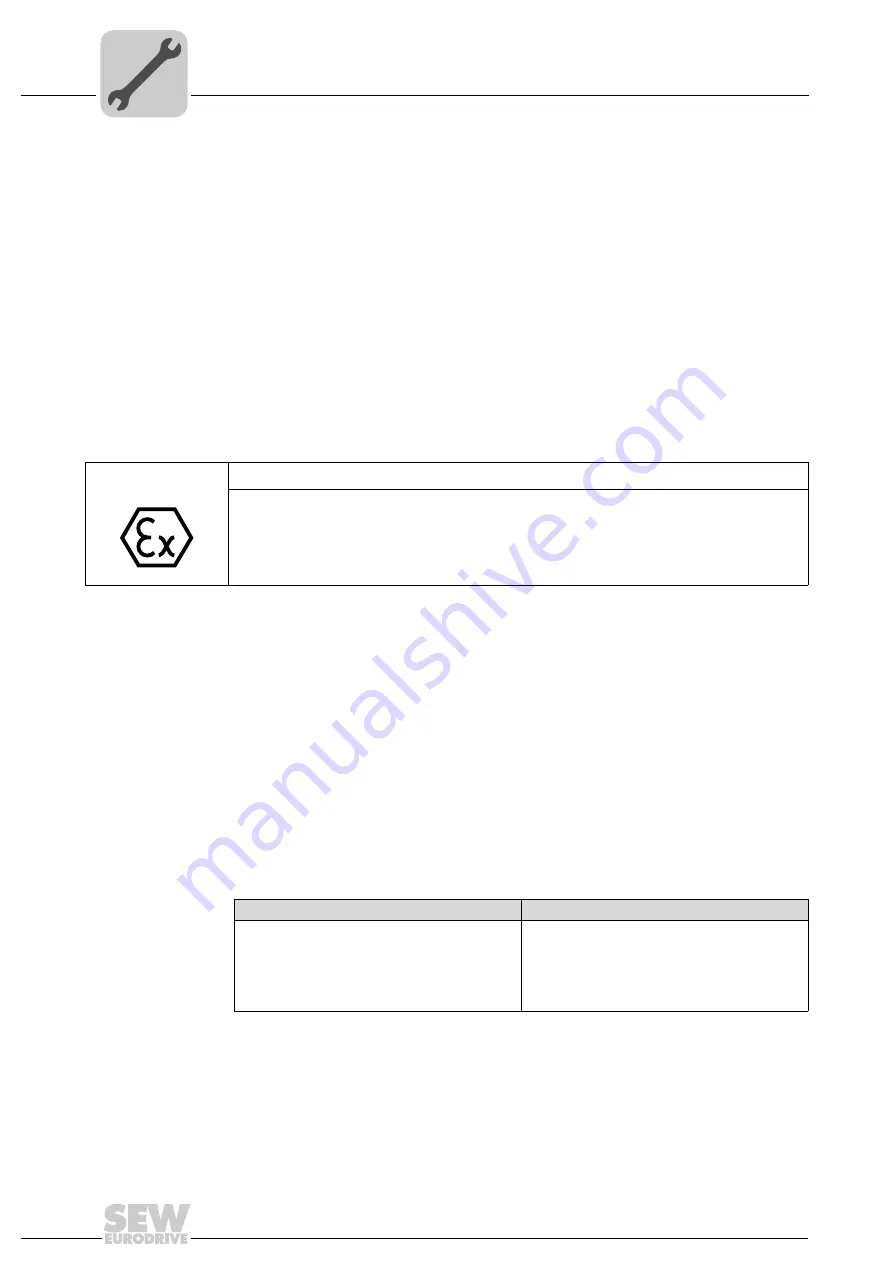
16
Operating Instructions – Explosion-Proof AC Motors – DRS/DRE/DRP 315
4
Mechanical installation
Mechanical Installation
4.2.2
Installing the motor
• The motor or gearmotor may only be mounted or installed in the specified mounting
position on a level, vibration-proof and torsionally rigid support structure.
• Clean the output shafts thoroughly to ensure they are free of anti-corrosion agents
(use a commercially available solvent). Do not allow the solvent to penetrate the
bearings and shaft seals – this could damage the material.
• Carefully align the motor and the driven machine to avoid placing any unacceptable
strain on the motor shafts (observe permitted overhung load and axial load!).
• Do not butt or hammer the shaft end.
• Ensure there is sufficient clearance around the unit to allow for adequate cooling.
Furthermore, the unit must be positioned in such a way that it does not reuse the air
warmed by other devices.
• Balance components for subsequent mounting on the shaft with a half key (output
shafts are balanced with a half key).
Installation in
damp locations or
in the open
• Use suitable cable glands for the incoming cable (use reducing adapters if
necessary) according to the installation instructions.
• Coat the threads of cable glands and screw plugs with sealant and tighten them well
– then coat them again.
• Seal the cable entry well.
• Clean the sealing surfaces of the terminal box and the terminal box cover carefully
before re-assembly; gaskets have to be glued in on one side. Replace brittle gaskets.
• Restore the anticorrosion coating if necessary
• Check enclosure according to nameplate.
4.2.3
Installation tolerances
NOTE ON EXPLOSION PROTECTION
• If using belt pulleys:
– Only use belts that do not build up an electrostatic charge.
– Do not exceed the maximum permitted overhung load.
• Use an appropriate cover to protect motors in vertical mounting positions from
objects or fluids entering (protection cowl C)!
Shaft end
Flanges
Diameter tolerance according to EN 50347
•
ISO j6 with
∅ ≤
28 mm
•
ISO k6 with
∅ ≥
38 mm up to
≤
48 mm
•
ISO m6 with
∅ ≥
55mm
•
Center bore in accordance with DIN 332, shape
DR..
Centering shoulder tolerance according to
EN 50347
•
ISO j6 with
∅ ≤
250 mm
•
ISO h6 with
∅ ≥
300 mm