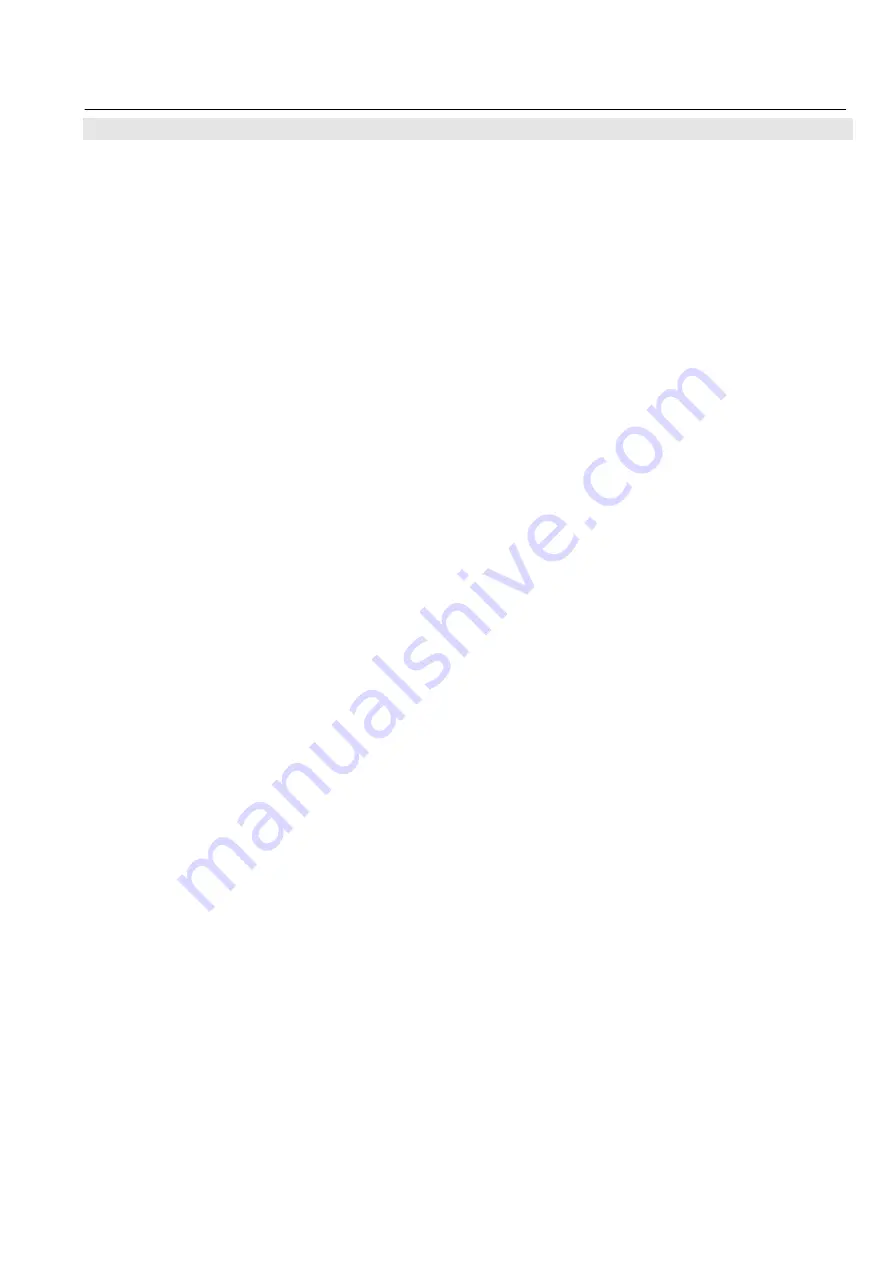
Technical Manual
Absolute Single/Multiturn Encoders
Profibus
R.000.000
5-7 of 22
5
5
Characteristics
of
the
Multiturn
Encoder
on
the
Profibus
Characteristics of the Multiturn Encoder on the Profibus
PNO
‐
Ident
‐
Number
The
Sendix
Absolute
Singleturn/Multiturn
Encoder
has
the
PNO
‐
Ident
‐
Number
5868
(Hex).
This
number
is
registered
at
the
PNO
(Profibus
User
Organization)
as
an
unique
identification.
The
according
GSD
‐
Files
are
named
as
follows:
•
Multiturn
Series
5868,5888
KUEB5868.GSD
•
Singleturn
Series
5858,5878
KUEB5868ST.GSD
Start
phase
of
the
encoder
on
the
PROFIBUS
When
the
encoder
starts
up
it
is
in
the
‘Baud
‐
Search’
state.
Once
the
baud
rate
has
been
recognized,
it
switches
to
the
WAIT_PRM
state
and
waits
for
the
parameter
data
from
the
DP
‐
Master.
The
parameterisation
occurs
automatically
when
the
DP
‐
Master
starts
up.
The
following
parameters
are
transmitted
to
the
encoder:
count
direction
and
the
measuring
length
in
steps
(for
more
details,
see
the
Encoder
Profile
from
the
PNO).
When
the
correct
parameter
data
have
been
successfully
transferred,
the
encoder
switches
to
the
WAIT_CFG
state.
The
PROFIBUS
Master
then
sends
a
configuration
byte
to
determine
the
number
of
inputs/outputs.
If
the
configuration
byte
is
correct,
the
encoder
switches
to
the
state
DATA_EXCHANGE
.
Configuration
and
Parameterisation
The
parameterisation,
i.e.
the
transfer
of
the
parameters
for
count
direction,
encoder
resolution
etc.,
normally
occurs
within
the
configuration
programme
for
the
PROFIBUS
Master
used.
To
do
this,
the
type
file
or
GSD
(device
file)
should
be
copied
to
the
respective
directory
for
type
or
GSD
files.
With
some
programmes
such
as
COM
PROFIBUS
or
STEP7
Manager,
an
update
of
the
internal
device
list
(hardware
catalogue)
must
be
carried
out
within
the
software.
For
more
information
about
integrating
field
devices,
please
refer
to
the
documentation
for
the
software
you
are
using.
The
two
steps
described
below
are
normally
necessary
for
integrating
and
parameterising
the
encoder
in
a
Master
system.
Configuration
For
configuration
purposes,
i.e.
to
input
the
length
and
type
of
the
I/O
on
the
PROFIBUS,
the
configuration
programme
normally
provides
an
input
mask
(screen),
in
which
–
independently
of
the
desired
configuration
–
the
identifier
has
normally
already
been
set
as
a
default,
so
that
only
the
I/O
addresses
remain
to
be
entered.
Depending
on
the
required
configuration
that
is
desired,
the
encoder
allocates
a
varying
number
of
input
and
output
words
on
the
PROFIBUS.
The
following
parameters
described
are
also
dependent
on
the
required
configuration.
The
GSD
device
file
(e.g.
KUEB5868.GSD)
contains
five
required
configurations
for
PNO
Class1
and
2,
each
with
16
‐
and
32
Bit
resolution.