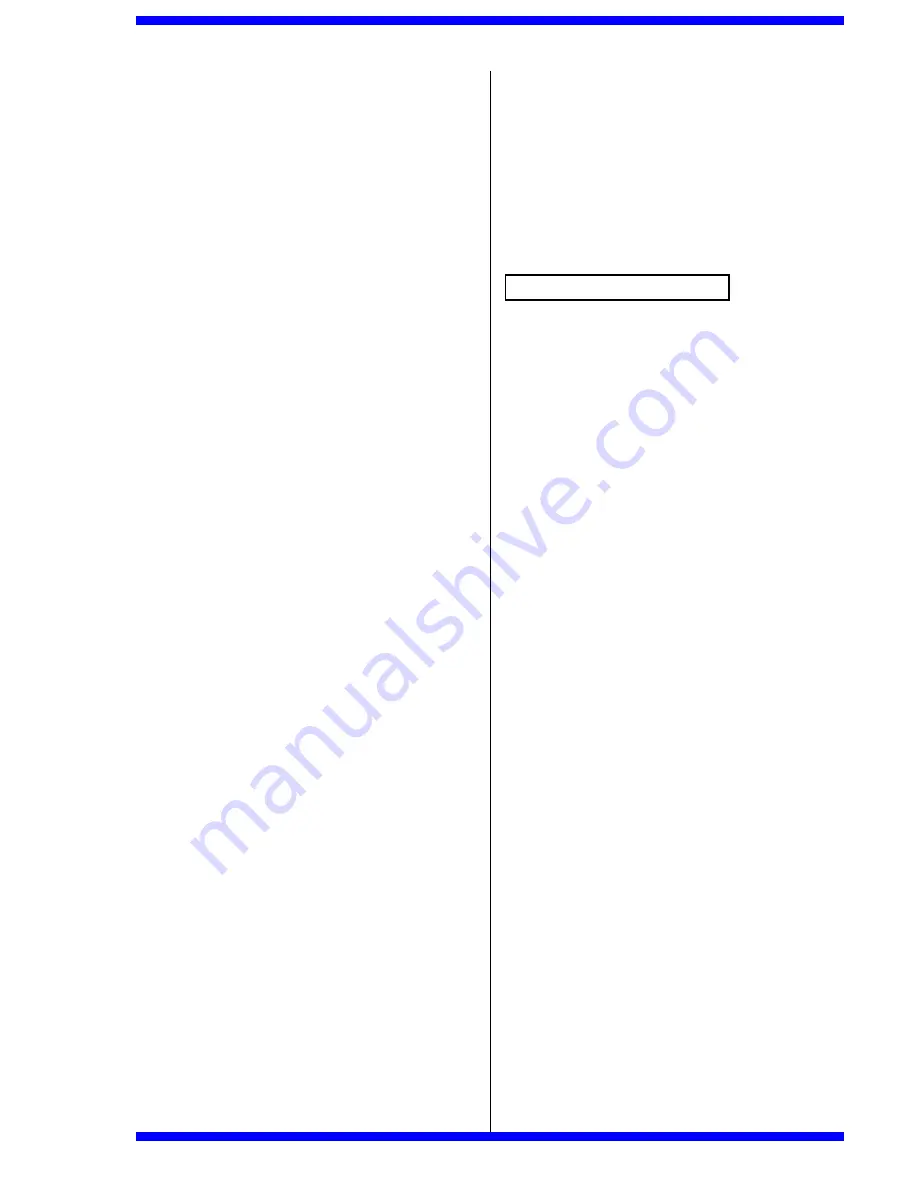
Selwood Seltorque S150 Manual
13
b) Thoroughly clean all surfaces of flushing
chamber (D33) and press new seals into
position, ensuring that they face in the correct
directions: The garter spring fitted to the lip of
the seal nearest the bearing housing, should
be visible from the bearing housing side of the
flushing chamber. The garter spring fitted to
the lip of the seal nearest the impeller, should
be visible from the impeller side of the
flushing chamber. Refer to Section 6.8.5
Assemble Flushing Chamber for disposition of
seals.
11. Replacement of the flushing chamber sub-
assembly in the bearing housing must be
undertaken very carefully to ensure that the lips of
seals (D04) are not damaged by the shoulders on
the drive shaft (D17). Use assembly tool (Part No.
0015165100) for this purpose. A generous
quantity of oil should be applied to the shaft to
assist this operation, and a new gasket (C13)
should be fitted. Replace and tighten screws
(D31) and spring washers (A06).
12. Position new gasket (C13) on studs (C14) and fit
bearing housing assembly to pump body, taking
great care to ensure that the shaft does not touch
the mechanical seal stationary seat. Replace and
tighten nuts (A11) and spring washers (A12).
13. Using lifting equipment in compliance with the
Health and Safety at Work Act, 1975, position
pump unit on chassis being careful to replace any
shims in their original positions. Replace nuts,
bolts and washers and assemble, but do not
tighten nuts.
14. Refer to Section 1.5 when refitting the pump to a
diesel engine. Refer to Section 1.7 when refitting
the pump to an electric motor.
15. Replace split guards around flexible coupling and
ensure that it is securely fastened, with nuts bolts
and washers. Also fasten to flywheel guard where
applicable with bolts and washers.
16. Read Instructions 19 to 21 of this Section and
Section 5.4.2 Air Pump Mechanism Instructions 1
to 3, and:
a) Carefully remove any foreign matter from the
sleeve and mechanical seal components.
Smear clean engine oil on both the ‘O’ ring
(C07) and the drive shaft diameters.
b) Position the ‘O’ ring on the shaft taking care
to prevent it contacting the drive shaft's
keyway, and slide the sleeve/seal assembly
onto shaft (carbon face towards stationary
seat) and press into working position using
only the sleeve's flange.
c) Ensure that ‘O’ ring is correctly trapped in
sleeve recess.
17. Replace impeller, suction tube and separator
components in accordance with Section 5.3.1
Impeller (C04) Instructions 7 to 12, inclusively.
18. Replace bearing/seal housing assembly and
actuator neck seal in accordance with Section
5.1.5 Drive Rod Seal Assembly and Bearing (A25
and A28) Instruction 8 and Section 5.1.4 Actuator
Neck Seal (A21) Instruction 4.
19. Replace remaining air pump components in
accordance with Section 5.1.3 Actuator Seal (A18)
Instructions 6 and 10, inclusively.
20. Replace drain plug (D34) using PTFE tape as
sealant, and fill flushing chamber with new oil to
level of plug hole. Replace plug (D08) with ‘O’
ring (D07). Refer to Section 3.1 Pump Lubrication
for details of the oil required for the flushing
chamber.
21. Repeat this procedure for bearing housing
ensuring that level plug (D08) with ‘O’ ring (D07)
are replaced after the correct oil level is attained.
Should actuator (A20) fail to reciprocate when the
pump is running, or if other abnormal conditions are
suspected, the air pump mechanism should be
immediately inspected to minimise the risk of
consequential damage.
Proceed as follows:
1. Drain oil from bearing housing and flushing
chamber by removing filler caps (D08) with ‘O’ ring
(D07) and drain plugs (D13) with sealing washer
(D14) and (D34).
2. Remove air pump components in accordance with
Section 5.1.3 Actuator Seal (A18) and Section
5.1.4 Actuator Neck Seal (A21) Instructions 2 and
3 (discard actuator neck seal if it has failed).
3. Being careful not to damage the flat sealing faces
of housing (A24) carefully withdraw housing
complete with bearing and sealing components
from bearing housing (D06) and drive rod (D37).
4. Carry out Section 5.3.1 Impeller (C04) Instructions
2 to 4, inclusively.
5. Carry out Section 5.4.1 Flushing Chamber (D33)
Instructions 2 to 9, inclusively.
6. Release nut (D38) and withdraw screw (D27),
allowing fulcrum pin (D28) to be removed. Drive
rod (D37) and connecting rod (D26) may then be
withdrawn. If second priming pump is fitted,
repeat these operations, ensuring that the
connecting rod, fulcrum pin and drive rod
components are kept as sets, and can later be
reassembled in their original positions.
7. Remove circlip (D24). Eccentric (D23) can now
be removed by inserting M10 bolt in tapped hole
provided and tapping to loosen in an anti-
clockwise direction (eccentric has a right hand
thread). See Section 6.9 Remove Eccentric.
8. Examine condition of all components and renew
failed or significantly worn items. A replacement
connecting rod, complete with bushes, should be
ordered
against
sub-assembly
(Part
No.
0015908000).
9. To rebuild mechanism, ensure thread and abutting
shoulder is thoroughly clean and simply screw on
the eccentric, making sure it abuts against the
shaft (D17) shoulder. Refit circlip (D24).
10. Position connecting rod(s) (D26) on eccentric,
thoroughly degrease tapping in drive rod(s) (D37)
and assemble drive rod(s) and fulcrum pin (D28)
in connecting rod(s).
Summary of Contents for SELTORQUE S150
Page 25: ...Selwood Seltorque S150 Manual 25 THIS PAGE INTENTIONALLY BLANK ...
Page 28: ...Selwood Seltorque S150 Manual 28 ...
Page 30: ...Selwood Seltorque S150 Manual 30 ...
Page 32: ...Selwood Seltorque S150 Manual 32 ...
Page 34: ...Selwood Seltorque S150 Manual 34 ...
Page 36: ...Selwood Seltorque S150 Manual 36 ...
Page 38: ...Selwood Seltorque S150 Manual 38 ...
Page 40: ...Selwood Seltorque S150 Manual 40 ...
Page 42: ...Selwood Seltorque S150 Manual 42 ...
Page 44: ...Selwood Seltorque S150 Manual 44 ...
Page 46: ...Selwood Seltorque S150 Manual 46 ...
Page 48: ...Selwood Seltorque S150 Manual 48 ...
Page 50: ...Selwood Seltorque S150 Manual 50 ...
Page 52: ...Selwood Seltorque S150 Manual 52 ...
Page 54: ...Selwood Seltorque S150 Manual 54 ...
Page 56: ...Selwood Seltorque S150 Manual 56 ...
Page 58: ...Selwood Seltorque S150 Manual 58 9 WIRING DIAGRAMS 9 1 Isuzu 4JG1 Engine Canopy ...
Page 60: ...Selwood Seltorque S150 Manual 60 9 3 Deutz Wiring Diagram ...
Page 62: ...Selwood Seltorque S150 Manual 62 THIS PAGE INTENTIONALLY BLANK ...