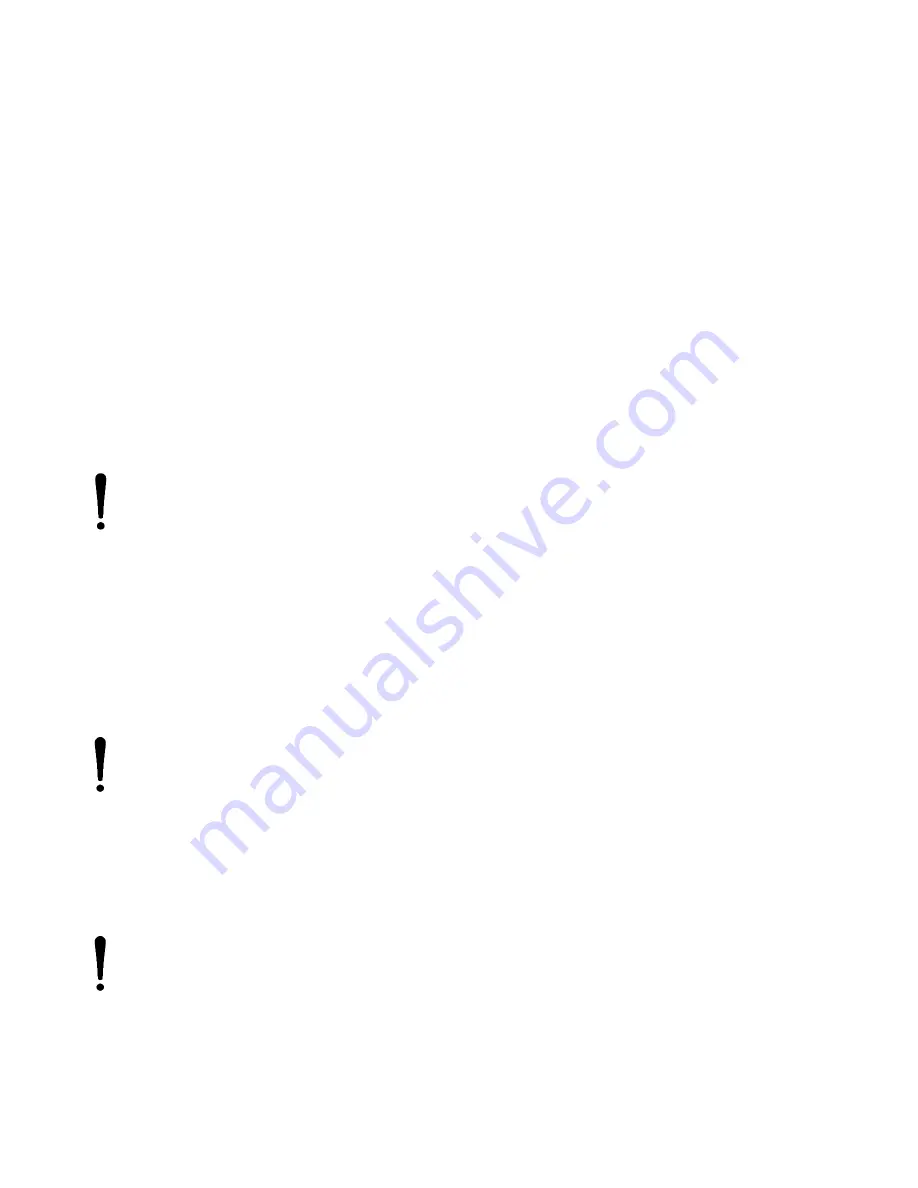
7.
Push the films with a leader panel (C) into the nip using slow mode (B).
Note:
Use a leader panel of the same material, thickness and width as the panels to process.
Use a release board when processing thin images.
5.4.4 Presetting the tension
To enable the film to unwind without wrinkles tension (brake) can be set to the roll.
On the right-hand (control panel) side of the machine you will find a tension control ring on each
shaft. Turn the tension control ring counter-clockwise (top to rear) to set the tension or clockwise
(top to front) to release the tension.
When the film is webbed, it is recommended to set a low tension to each shaft by turning the ring
counter-clockwise until you feel some resistance. This will prevent film from unwinding without
tension.
5.4.5 Pressure setting
Thin images
When processing thin images (printer output, posters, etc.) pressure is preset when the upper and
lower material is webbed. When the leader panel or release board is through the nip, the nip is set
to zero and pressure is preset. The best pressure setting for thin films is about 80%. During
processing the pressure can be adjusted.
CAUTION:
Soft panels (Foam) require less pressure. Set the pressure proportional to the rigidity
of the foam between 40% and 80% to avoid permanent compression marks.
Panels
When processing panels, a leader panel is used to web the film(s). This leader panel is at the same
time used to preset the pressure.
Use a leader panel of the same material, thickness and width as the panels to process.
1.
Set the nip to the thickness of the panel.
2.
Feed the leader panel into the nip in slow mode.
3.
When the edges of the film(s) are through the nip, set the pressure to approximately 80% for full-
width panels.
CAUTION:
For narrower (or soft) panels set the pressure proportional to the width (rigidity)
between 40% and 80%. E.g. half width equals 60%.
Mounting boards
Use a leader panel of the same material, thickness and width as the panels to process.
1.
Set the nip to the thickness of the panel.
2.
Feed the leader panel into the nip in slow mode.
3.
When the panel is halfway in the nip, set the pressure between 70 and 80% for full-width panels.
CAUTION:
For narrower (or soft) panels set the pressure proportional to the width (rigidity)
between 40% and 80%. E.g. half width equals 60%.
4.
Back-up the panel out of the nip
Note:
The image will add approximately an additional 5 to 10% to the pressure.
Summary of Contents for 54Base
Page 1: ...62 54Base Mounter and Laminator User Manual A Version Models Rev C December 2017...
Page 10: ......
Page 35: ...25 English...