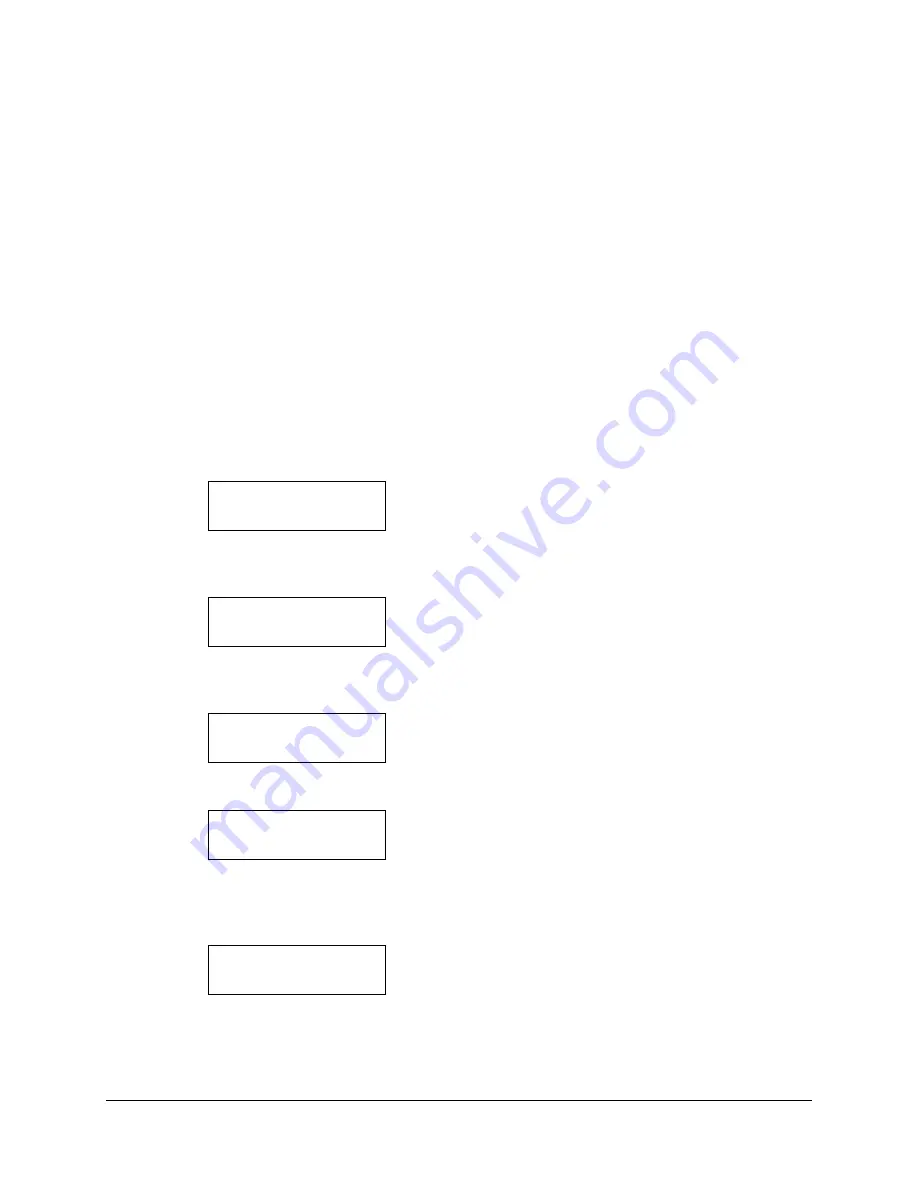
11-2
Additional Front-Panel Interface Details
Date Code 990215
SEL-351P Manual Técnico
These text label settings are set with the SET T command or viewed with the SHOWSET T
command via the serial port [see
Section 9: Setting the SEL-351P Recloser Control
and
SHO
Command (Show/View Settings)
in
Section 10: Serial Port Communications and Commands
].
The top numeral in the above example screen (SET RECLOSURES=3) corresponds to the “last
shot” value, which is a function of the number of set open intervals. There are three set open
intervals in the factory default settings, thus three reclosures (shots) are possible in a reclose
sequence.
The bottom numeral in the above example screen [RECLOSE COUNT = 0 (or = 3)] corresponds
to the “present shot” value. If the breaker is closed and the reclosing relay is reset (RESET LED
on front panel is illuminated), RECLOSE COUNT = 0. If the breaker is open and the reclosing
relay is locked out after a reclose sequence (LOCKOUT LED on front panel is illuminated),
RECLOSE COUNT = 3.
SEL-351P Recloser Control Shot Counter Screen Operation (with factory settings)
With the recloser closed and the SEL-351P Recloser Control in the reset state (front-panel
RESET LED illuminated), the shot counter screen appears as:
SET RECLOSURES=3
RECLOSE COUNT =0
The SEL-351P trips the recloser open and goes to the reclose cycle state (front-panel CYCLE
LED illuminates). The shot counter screen still appears as:
SET RECLOSURES=3
RECLOSE COUNT =0
The first open interval (79OI1 = 300) times out, the shot counter increments from 0 to 1, and the
SEL-351P recloses the recloser. The shot counter screen shows the incremented shot counter:
SET RECLOSURES=3
RECLOSE COUNT =1
The SEL-351P trips the recloser open again. The shot counter screen still appears as:
SET RECLOSURES=3
RECLOSE COUNT =1
The second open interval (79OI2 = 600) times out, the shot counter increments from 1 to 2, and
the SEL-351P recloses the recloser. The shot counter screen shows the incremented shot
counter:
SET RECLOSURES=3
RECLOSE COUNT =2
Summary of Contents for SEL-351P
Page 6: ......
Page 92: ......
Page 96: ......
Page 154: ......
Page 156: ......
Page 222: ......
Page 258: ......
Page 262: ......
Page 324: ......
Page 368: ......
Page 406: ......
Page 482: ......
Page 534: ......
Page 539: ......
Page 549: ......
Page 551: ......
Page 587: ......
Page 597: ......
Page 601: ......
Page 603: ......
Page 609: ......
Page 621: ......
Page 635: ......
Page 649: ......
Page 665: ......
Page 671: ......