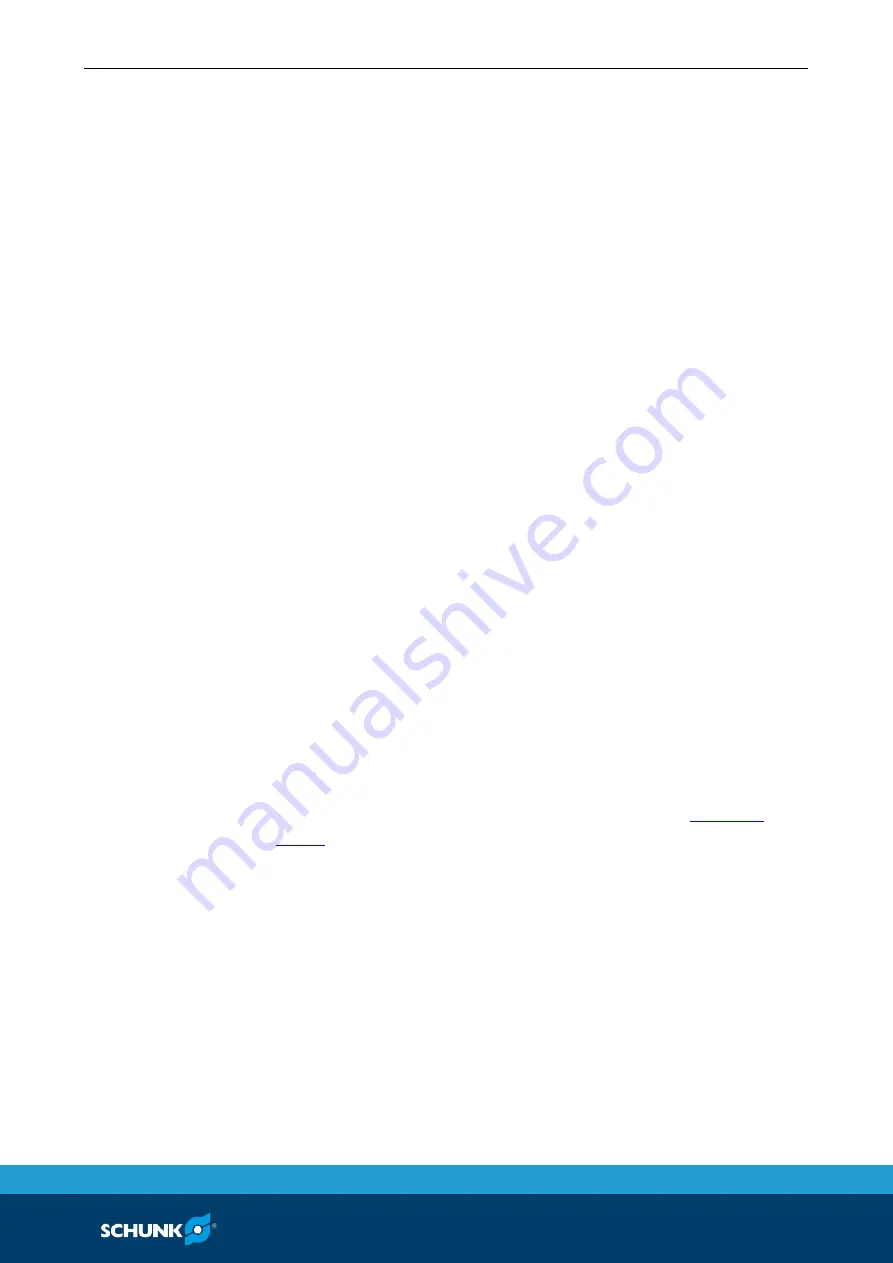
Functional description
02.00|WDB 99 |en
45
Functional description
The clamping systems of the WDB 99 modular system can be com-
bined with individual clamping pillars using change interfaces similar
to a quick-change pallet system and joined using the manual con-
necting devices of the system components. This enables a clamping
device setup for 5-sided machining of a workpiece to be joined on
several clamping pillars.
The clamping systems adapted on the clamping pillars can be actu-
ated pneumatically, manually or manually hydraulically as desired.
With the WDS 99 stacking modules, five different heights are
available. Appropriate combinations of systems enable clamping
pillars to be mounted in increments of 10 mm. The WDA 99-79
hydraulic compensation element or the WDA 99-70 pneumatic
clamping system in connection with the respectively suitable
workpiece direct clamping pins are intended for fine height
adjustments to the workpiece interface.
Function of the connecting unit in the change components
The clamping systems of the WDB 99 modular system have a special
connecting mechanism which contains a quick-change function.
The connection is transferred to a connection shaft by a tapered
screw. At the same time, a pre-tension force is applied at the
clamping point on the flat surfaces positioned against one another.
A hexagonal socket screw drive wrench size 6 mm is required to
clamp or loosen the connecting unit.
For the connecting points, the corresponding screw tightening
torques for the clamping screws of the change interface must be
adhered to (see chapter "Screw tightening torques"
).
The achievable pull-in force on the change interface varies,
depending on the screw tightening torque. The maximum torque
for the clamping screw may not be exceeded; for this reason, a
torque wrench with socket must be used.
To quickly fit the clamping structure, the WDB 99-60 base module
and the WDG 99-60 basic module include a hexagonal socket
screwdriver.
6
6.1