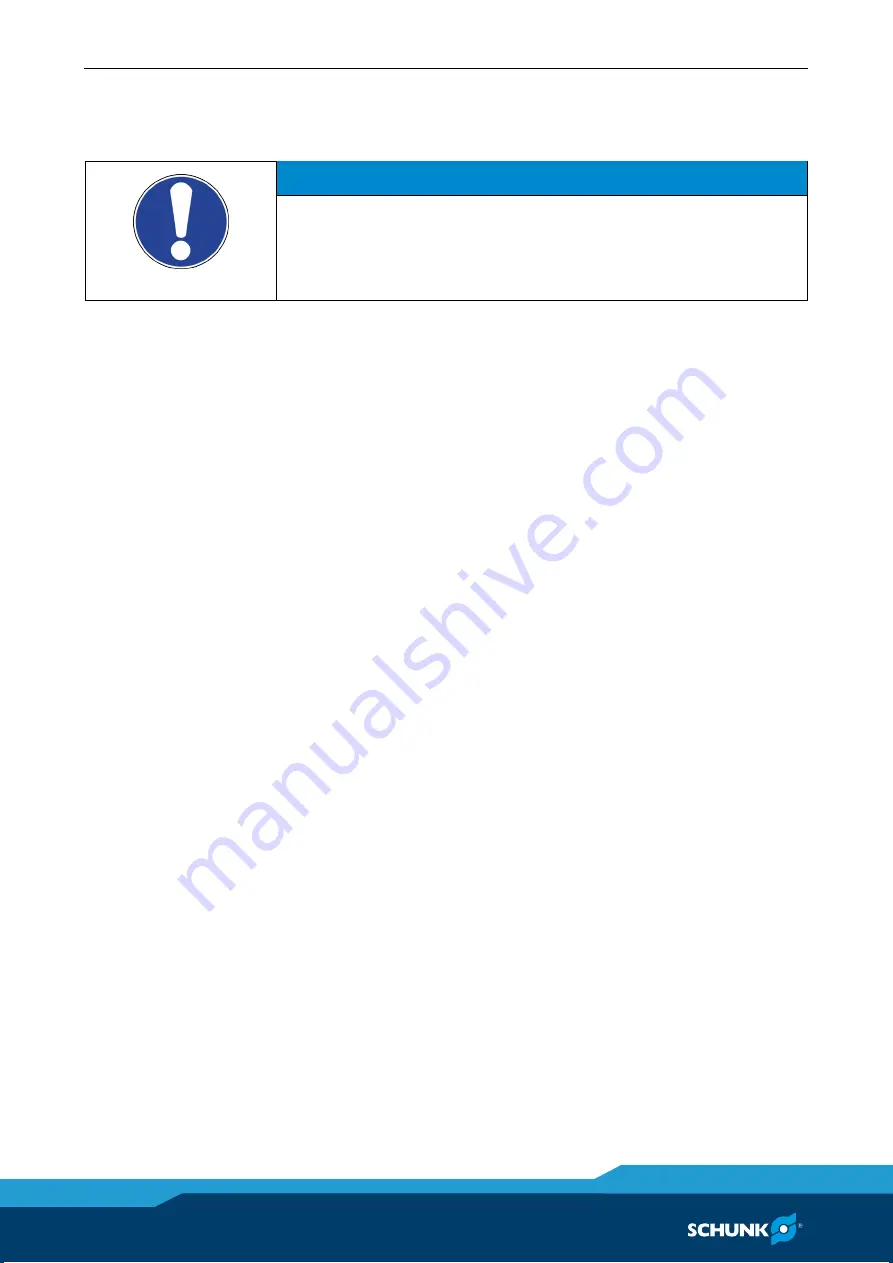
Operational Considerations
24
01.00|SWS-001 |en
Tool Stand Design
NOTICE
During coupling and lock-up, the Tool Stand must allow for
movement (float) in a plane parallel to the mating surfaces of
the SWK and SWA, and in a direction perpendicular to this
plane, towards the SWK.
In most cases, the Tools are stored in a Tool Stand when not being
used by the robot. During coupling and lock-up, the Tool Stand
must allow for movement (float) in a plane parallel with the mat-
ing surfaces of the SWK and SWA (X and Y), and also in a direction
towards the SWK (Z). Even slight misalignment between the SWK
and SWA can generate high forces during lock-up if the SWA is not
allowed to float into place during lock-up. These high forces can
cause excessive wear and even jamming of the end-effector and
robot. The degree of float required depends on the accuracy of the
robot’s positioning and the repeatability of the Tool location in the
Tool Stand during lock-up. See the following figure and table for
recommended maximum allowable float (offsets) prior to coupl-
ing. The Tool Stand should be designed to minimize misalignment
during coupling and uncoupling. In some cases, greater offsets
than shown in the following table can be accommodated by the
SWK and the SWA, but will increase wear.
Ideally, the Tool should be hanging vertically in the Tool Stand so
that gravity acts to uncouple the SWA from the SWK during un-
locking. It is possible to design Tool Stands that hold Tools in the
horizontal position, but care must be taken that the necessary
compliance is provided during coupling and uncoupling. In general,
“horizontal-position” SWA cause more wear on the locking me-
chanism and locating features of the Tool and Tool Stand.
Lock-up should occur with the SWK in the No-Touch™ locking zone
(see the following table), but not touching the SWA. When air is
supplied to the lock port, the SWK should draw the SWA into the
locked position.
7.3
Summary of Contents for SWS-001
Page 35: ...Drawings 01 00 SWS 001 en 35 Drawings Tool Changer SWS 001 Tool Changer 11 11 1...
Page 36: ...Drawings 36 01 00 SWS 001 en quick change head SWK 001...
Page 37: ...Drawings 01 00 SWS 001 en 37 quick change adapter SWA 001...
Page 38: ...Drawings 38 01 00 SWS 001 en E04 Electrical Module Electrical Module 11 2...
Page 40: ...40 01 00 SWS 001 en...