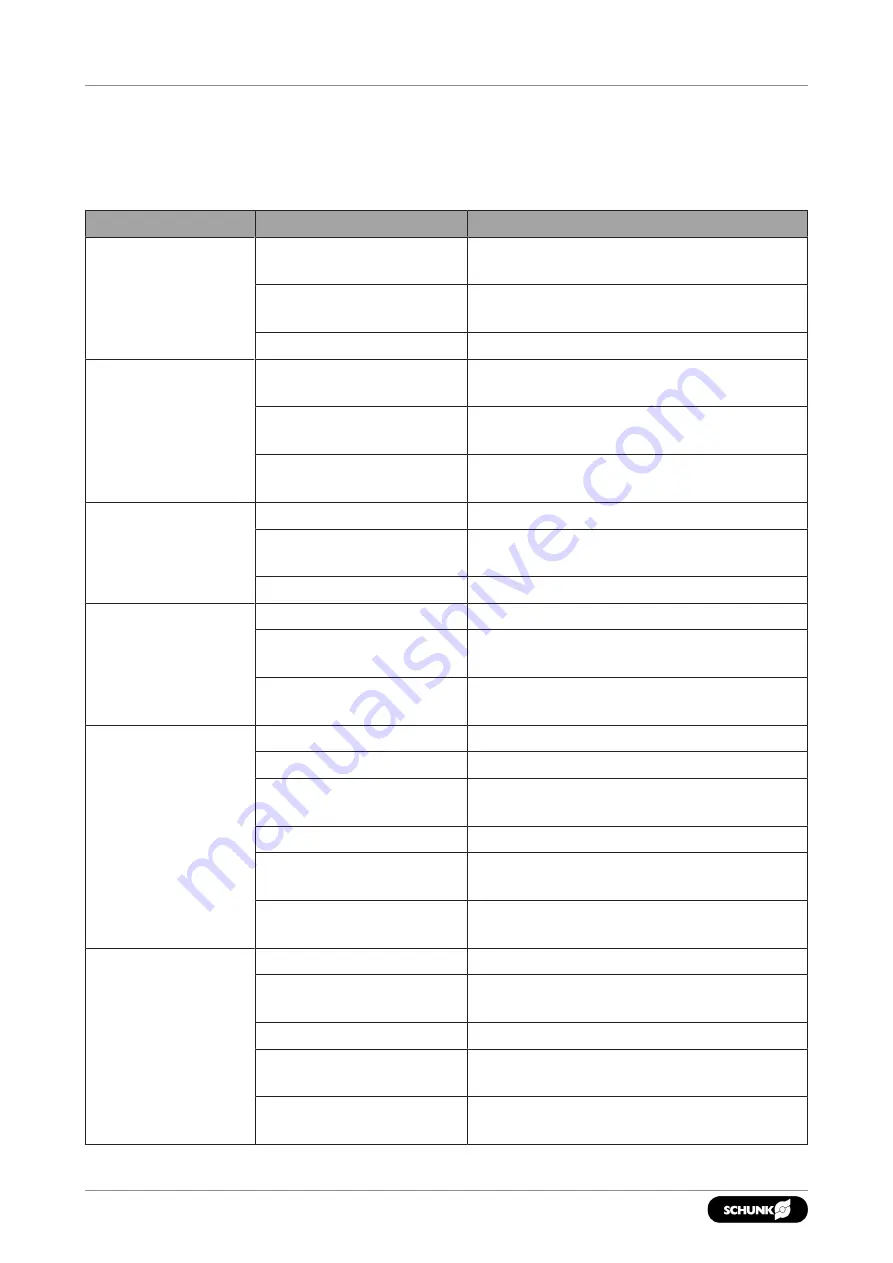
Troubleshooting
30
04.00 | FDB | Assembly and Operating Manual | en | 389072
7 Troubleshooting
Deburring process development is an iterative, learning task. The
following table is presented to assist in solving deburring
problems.
Symptom
Cause
Resolution
Burr Wear
Hard work material
Use better grade burr material add
coating (TiAlN)
Too heavy a cut
Decrease width of cut/make multiple
passes
Feed rate is too slow
Increase feed rate
Burr Breakage
Too heavy a cut
Decrease width of cut/make multiple
passes
Deflection at corner
Climb mill/do not begin path at sharp
corner
Impacting part
Decrease feed rate at contact/ enter part
at an angle
Unequal compliance Pivot bearing worn
Replace pivot bearing,
Compliance preload
screw not set properly
Worn ring cylinder
Poor finish on work
piece
Feed rate is too fast
Reduce feed rate
Burr is worn
Inspect burr if worn,
replace.
Motor bearings are worn Inspect spindle shaft, if shaft feels loose
Burr Chattering
during cut
Feed rate is too fast
Reduce feed rate
Lack of rigidity
Increase radial compliance pressure
Too heavy a cut
Decrease width of cut/make multiple
passes
Improper Burr selection
Choose burr designed for work material
Burr is worn
Inspect burr if worn,
replace
Motor bearings are worn Inspect spindle shaft, if shaft feels loose
Secondary Burrs
created on work
piece after cut
Incorrect feed rate
Reduce feed rate
Too heavy a cut
Decrease width of cut/make multiple
passes
Improper Burr selection
Choose burr designed for work material
Burr is worn
Inspect burr if worn,
replace
Motor bearings are worn Inspect spindle shaft, if shaft feels loose