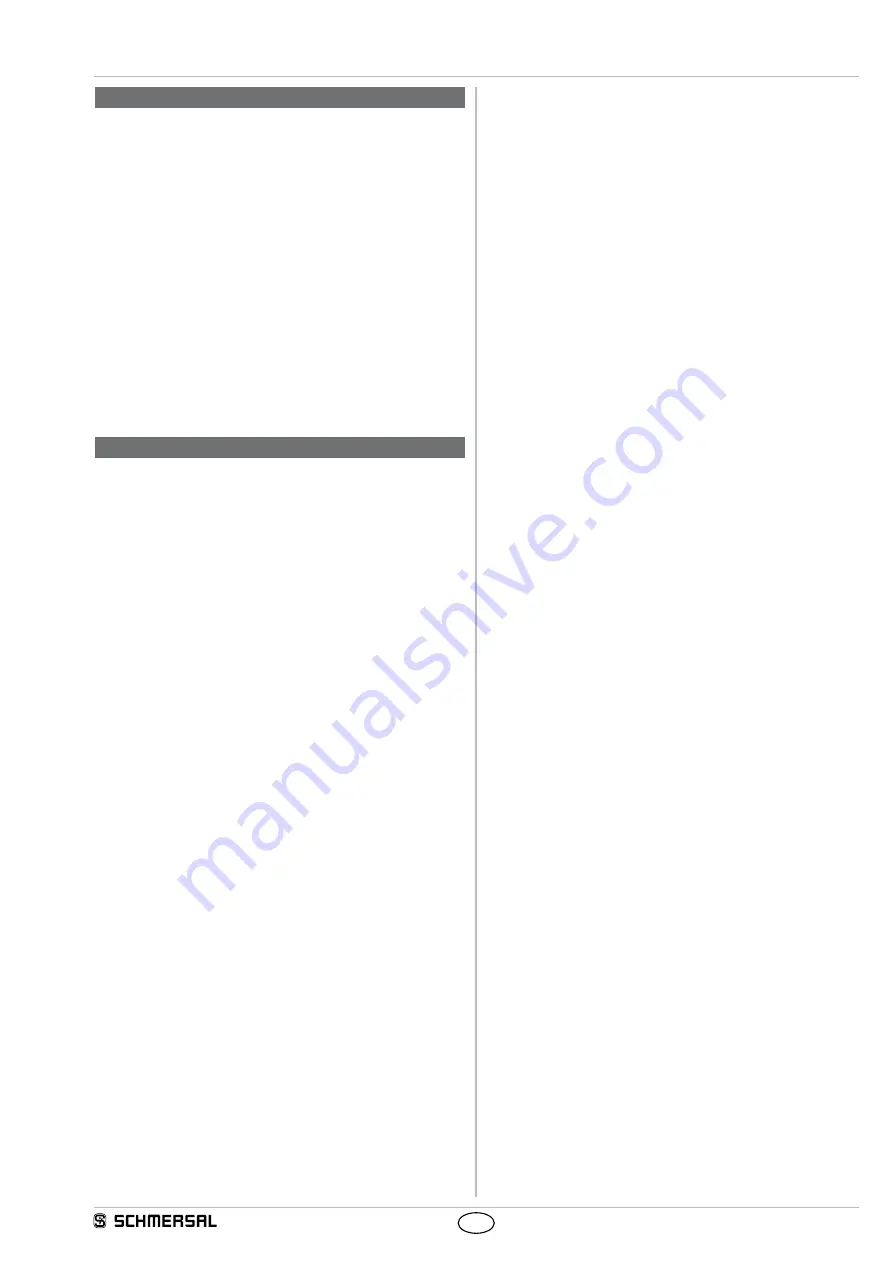
5
ZQ 700 AS
Operating instructions
Pull-wire emergency-stop switches
EN
7. Set-up and maintenance
7.1 Functional testing
The safety function of the safety components must be tested The
following conditions must be previously checked and met:
1 Check the correct fitting of the pull-wire emergency stop switch
2 Check the integrity of the cable entry and connections
3 Check the switch enclosure for damage
4 Check the functionality of the switch by actuating the wire
5 Check the cable tensioning by means of the position indicator
7.2 Maintenance
A regular visual inspection and functional test, including the following
steps, is recommended:
1 Check the functionality of the switch by actuating the wire
2 Check the cable entries and the wire connections
3 Remove particles of dust and soiling
4 Check the wire tension through the wire position indication and
check the wire and the wire guides for damages and proper fitting
Damaged or defective components must be replaced.
8. Disassembly and disposal
8.1 Disassembly
The safety switchgear must be disassembled in a de-energised
condition only
8.2 Disposal
The safety switchgear must be disposed of in an appropriate manner in
accordance with the national prescriptions and legislations