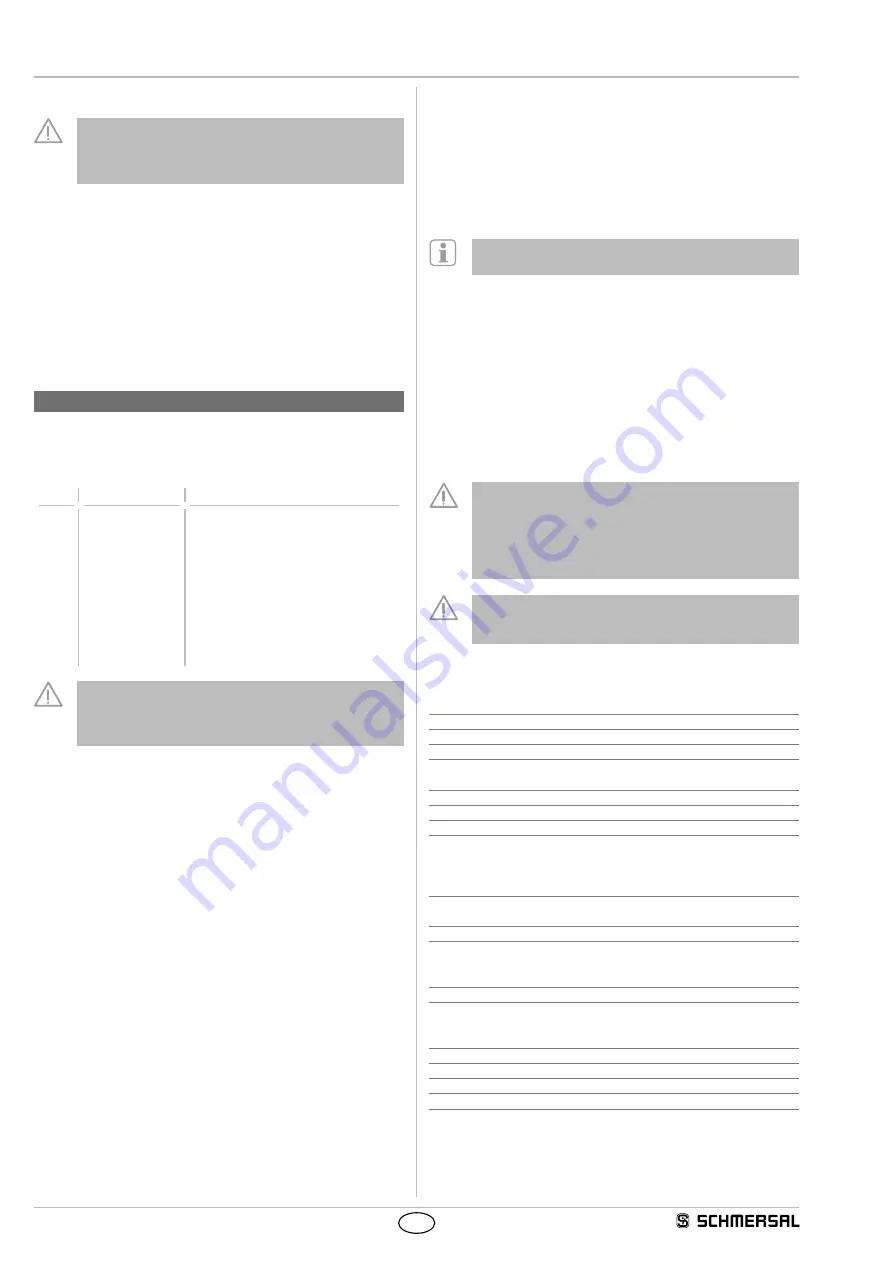
2
Operating instructions
Safety sensor
CSS 34F0
CSS 34F1
EN
1.6 Warning about misuse
In case of improper use or manipulation of the safety switch-
gear, personal hazards or damages to machinery or plant
components cannot be excluded. The relevant requirements
of the standard ISO 14119 must be observed.
1.7 Exclusion of liability
We shall accept no liability for damages and malfunctions resulting from
defective mounting or failure to comply with this operating instructions
manual. The manufacturer shall accept no liability for damages
resulting from the use of unauthorised spare parts or accessories.
For safety reasons, invasive work on the device as well as arbitrary
repairs, conversions and modifications to the device are strictly
forbidden; the manufacturer shall accept no liability for damages
resulting from such invasive work, arbitrary repairs, conversions and/or
modifications to the device.
2. Product description
2.1 Ordering code
This operating instructions manual applies to the following types:
CSS-
➀
-34
➁
-
➂
-
➃
-M-ST
No.
Option
Description
➀
12
14
Switching distance S
n
(mm)
Actuation from top
Actuation from side
➁
F0
F1
Relay feedback without
edge monitoring
with detection of the trailing edge
➂
S
lateral active surface
V
frontal active surface
➃
D
With diagnostic output
SD
With serial diagnostic function
Only if the information described in this operating instructions
manual are realised correctly, the safety function and
therefore the compliance with the Machinery Directive is
maintained.
2.2 Special versions
For special versions, which are not listed in the order code below 2.1,
these specifications apply accordingly, provided that they correspond to
the standard version.
2.3 Comprehensive quality insurance to 2006/42/EC
Schmersal is a certified company to appendix X of the Machinery
Directive. As a result, Schmersal is entitled to autonomously conduct
the conformity assessment procedure for the products listed in
Appendix IV of the MD without involving a notified body. The prototype
test certificates are available upon request or can be downloaded from
the Internet at www.schmersal.com.
2.4 Purpose
This non-contact, electronic safety sensor is designed for application
in safety circuits and is used for monitoring the position of movable
safety guards. In this application, the safety sensor monitors the closed
position of hinged, sliding or removable safety guards by means of the
coded electronic CST 34 or CST 180 actuators (refer to table "Actuators
and switching distances").
The safety function consists of safely switching off the safety outputs
when the safety guard is opened and maintaining the safe switched off
condition of the safety outputs for as long as the safety guard is open.
The sensor additionally executes functions of a safety-monitoring
module. At both safety outputs, two auxiliary contactors
1)
or relays
1)
can be connected, whose safety-related function is checked by the
sensor by means of a feedback circuit. The feedback circuit includes
the series-wiring of the NC contacts of the auxiliary contactors
1)
or
relays
1)
. For the F0 version, a so-called "enabling switch" (without
safety function) can be integrated in this feedback circuit. For the F1
version, a so-called "reset button" is required, which is monitored for a
trailing edge. This function corresponds to the "manual reset function"
to ISO 13849-1.
1)
with positive-guided contacts to IEC 60947-5-1 or EN 50205
The safety switchgears are classified according to
ISO 14119 as type 4 switching devices.
Series-wiring
Series-wiring can be set up. Response and risk times remain
unchanged by series-wiring. The number of devices is limited for
safety reasons. The self-monitoring safety sensors of the CSS 34F0 or
CSS 34F1 series can replace the safety-monitoring module. Therefore,
they can only be used as first sensor of a series-wired sensor chain
(refer to operating instructions CSS 34F0 / CSS 34F1).
Series-wiring of up to 31 CSS 34F0 or CSS 34F1… SD devices with
serial diagnostics is possible. A 200 m long sensor chain can be set up.
In devices with the serial diagnostics function (ordering suffix -SD), the
serial diagnostics connections are wired in series and connected to a
SD Gateway for evaluation purposes.
The user must evaluate and design the safety chain in
accordance with the relevant standards and the required
safety level.
If multiple safety sensors are involved in the same safety
function, the PFH values of the individual components must
be added.
The entire concept of the control system, in which the safety
component is integrated, must be validated to the relevant
standards.
2.5 Technical data
Standards:
IEC 60947-5-3, ISO 13849-1,
IEC 61508 , IEC 62061
Enclosure:
glass-fibre reinforced thermoplastic
Operating principle:
inductive
Coding level according to ISO 14119:
low
Actuator and switch distances
(according to IEC 60947-5-3):
see table "Actuator / Switch distances“
Hysteresis:
max: 1.5 mm
Repeat accuracy R:
< 0.5 mm
Maximum switching frequency:
3 Hz
Series-wiring:
Unlimited number of components, please
observe external cable protection, max. 31 components
in case of serial diagnostics, CSS 34F. as first sensor and safety-
monitoring module substitute
Cable length:
max. 200 m (cable length and cable section alter the
voltage drop depending on the output current)
Connector:
M12, 8-pin in casing
Temperature resistance of the cable:
- at rest:
−30 °C … +105 °C
- in motion:
−10 °C … +105 °C
Ambient conditions:
Ambient temperature T
u
:
- Output current ≤ 0.1 A / Output
–25 °C to +70 °C
- Output current ≤ 0.25 A / Output
–25 °C to +65 °C
Storage and transport temperature:
–25 °C … +85 ºC
Resistance to vibration:
10 … 55 Hz, amplitude 1 mm
Resistance to shock:
30 g / 11 ms
Protection class:
IP65, IP67 to IEC 60529