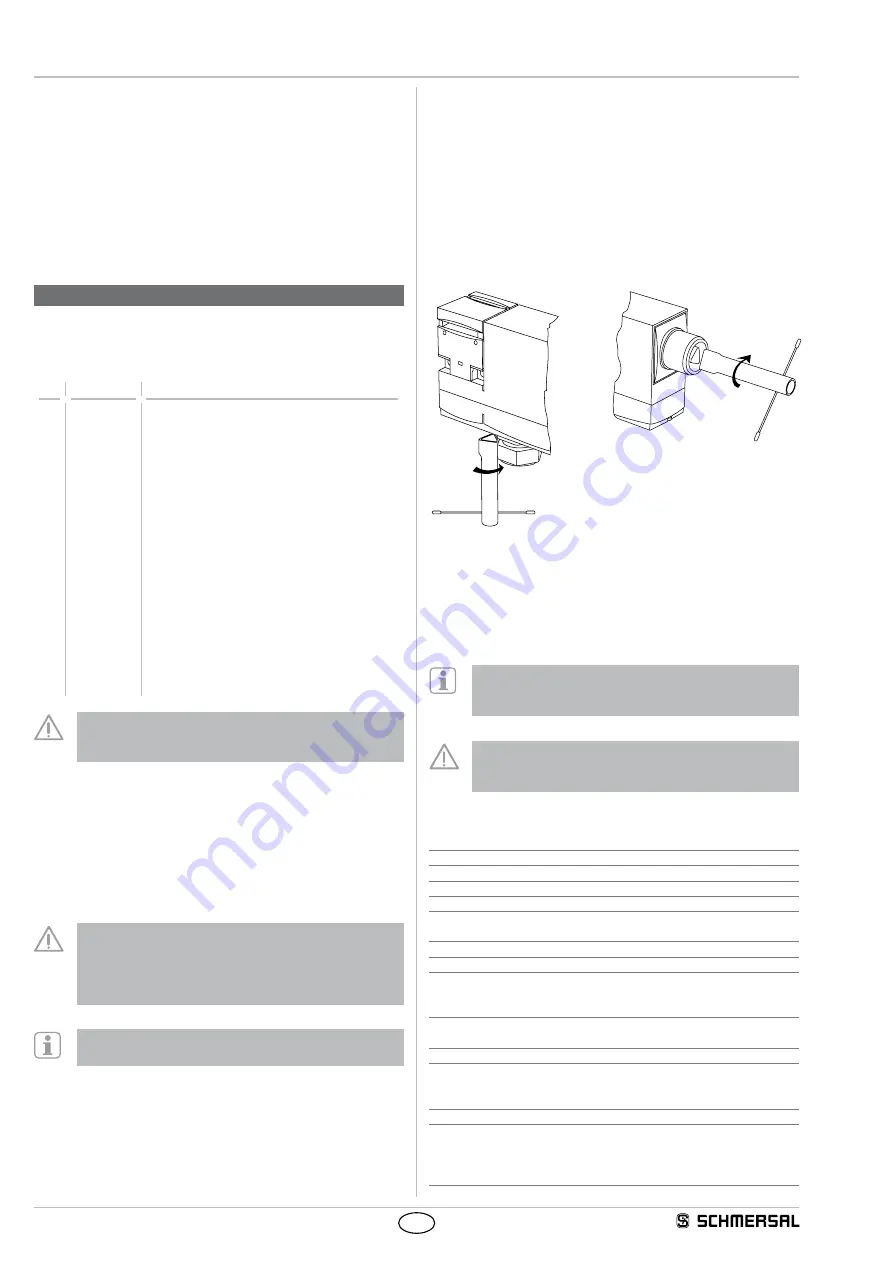
2
Operating instructions
Solenoid interlock
AZM 170
EN
1.7 Exclusion of liability
We shall accept no liability for damages and malfunctions resulting from
defective mounting or failure to comply with this operating instructions
manual. The manufacturer shall accept no liability for damages result-
ing from the use of unauthorised spare parts or accessories.
For safety reasons, invasive work on the device as well as arbitrary re-
pairs, conversions and modifications to the device are strictly forbidden;
the manufacturer shall accept no liability for damages resulting from
such invasive work, arbitrary repairs, conversions and/or modifications
to the device.
2. Product description
2.1 Ordering code
This operating instructions manual applies to the following types:
AZM 170
➀
-
➁
Z
➂
K
➃
-
➄
-
➅
-
➆
No.
Option
Description
➀
Cut clamps
SK
Screw connection
➁
11
1 NO / 1 NC
02
2 NC
➂
Latching force 5 N
R
Latching force 30 N
➃
Power to unlock
A
Power to lock
➄
Cable gland
ST
M12 x 1 connector
ST-2431
M12 connector, separated magnet monitoring
➅
24 VAC/DC
U
s
24 VAC / DC
110 VAC
U
s
110 VAC
230 VAC
U
s
230 VAC
➆
1637
Gold-plated contacts
➇
Manual release
2197
Lateral manual release (default in the
connector and power-to-unlock version)
2405
Emergency exit
Only if the information described in this operating instructions
manual are realised correctly, the safety function and therefore
the compliance with the Machinery Directive is maintained.
2.2 Special versions
For special versions, which are not listed in the order code below 2.1,
these specifications apply accordingly, provided that they correspond to
the standard version.
2.3 Destination and use
The solenoid interlock has been designed to prevent in conjunction
with the control part of a machine, movable safety guards from being
opened before hazardous conditions have been eliminated.
Solenoid interlocks with power to lock principle may only
be used in special cases after a thorough evaluation of
the risk of accident, since the safety guard can be opened
immediately on failure of the power supply or upon
activation of the main switch.
The safety switchgears are classified according to
ISO 14119 as type 2 interlocking devices.
Manual release
A manual release is available as a mounting tool and in the event of
a power failure in case the power to unlock principle is used. If the
triangular key is turned 180°, the locking bolt is pulled into the unlocking
position. Please ensure that jamming by external influence on the
actuator is avoided. The normal locking function is only restored after
the triangular key has been returned to its original position. After being
put into operation, the manual release must be secured by installing the
sealing plug, which is included in delivery.
Manual release
Manual release from side
Ordering suffix -2197 or ST
Triangular key TK-M5 (101100887) available as accessory.
Emergency exit
Fitting and actuation only from within the hazardous area.
To activate the emergency exit, turn the red lever in the direction of the
arrow to the end stop. Please ensure that jamming by external influence
on the actuator is avoided.
The user must evaluate and design the safety chain in
accordance with the relevant standards and the required
safety level.
The entire concept of the control system, in which the safety
component is integrated, must be validated to the relevant
standards.
2.4 Technical data
Standards:
IEC 60947-5-1, ISO 14119, BG-GS-ET-19
Enclosure:
glass-fibre reinforced thermoplastic, self-extinguishing
Actuator and locking bolt:
stainless steel 1.4301
Contact material:
Silver
Holding force F:
1000 N
Latching force:
5 N
- Ordering suffix R:
30 N
Coding level according to ISO 14119:
low
Protection class:
IP67
Contact type:
change-over contact with double break, type Zb
or 2 NC contacts, with galvanically
separated contact bridges
Switching system:
A
IEC 60947-5-1; slow action,
NC contact with positive break
Cable entry:
M20 x 1.5
Connection:
Cut clamps,
screw terminals or
M12 connector
Cable type:
flexible
Cable section:
- Cut clamps:
0.75...1.0 mm²
- Screw terminals:
0.25...1.5 mm²
(incl. insulated conductor ferrules)