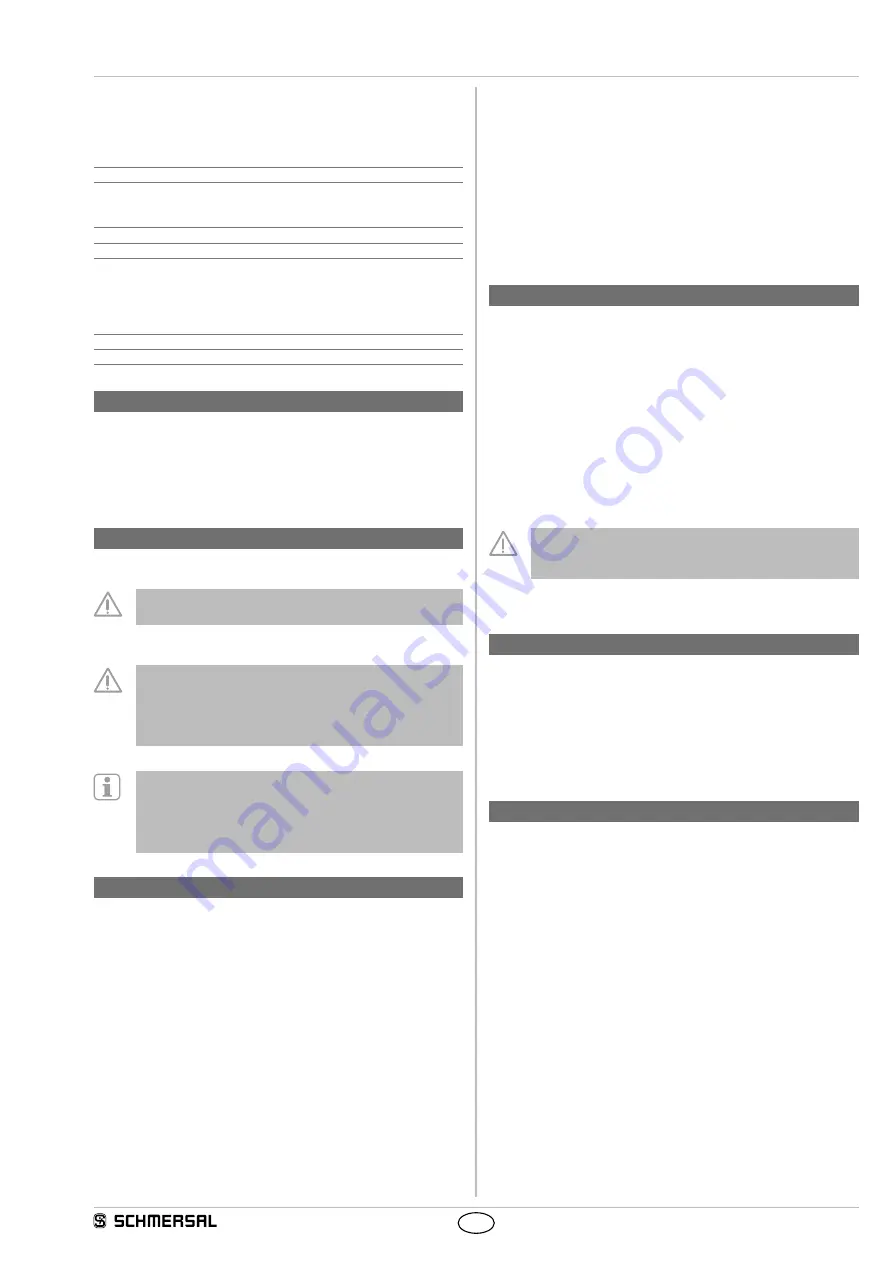
3
AES 1102
AES 1112
Operating instructions
Safety-monitoring module
EN
Weight:
AES 1102 / 1112: 120 g
AES 1102.1 / 1112.1: 160 g
AES 1102.2 / 1112.2: 160 g
AES 1102.3 / 1112.3: 125 g
AES 1102.4 / 1112.4: 160 g
Dimensions (H x W x D):
75 x 22.5 x 110 mm
2.5 Safety classification
Standards:
EN ISO 13849-1; IEC 61508
PL:
up to
Control category:
up to 1
PFH-value:
1.14 x 10
-6
/ h; applicable '
for applications with up to
max. 50,000 switching cycles / year
and max. 80 % contact load.
Diverging applications upon request.
SIL:
up to 1
Service life:
20 years
3. Mounting
3.1 General mounting instructions
Mounting: snaps onto standard DIN rails to EN 60715.
3.2 Dimensions
Device dimensions (H/W/D): 75 x 22,5 x 110 mm
4. Electrical connection
4.1 General information for electrical connection
The electrical connection may only be carried out by
authorised personnel in a de-energised condition.
Wiring examples: see appendix
As far as the electrical safety is concerned, the protection
against unintentional contact of the connected and therefore
electrically interconnected apparatus and the insulation of the
feed cables must be designed for the highest voltage, which
can occur in the device.
To avoid EMC disturbances, the physical ambient and
operational conditions at the place where the product
is installed, must meet the provisions laid down in the
paragraph "Electromagnetic Compatibility (EMC)" of
DIN EN 60204-1.
5. Operating principle and settings
5.1 Operating principle
The AES 1102 and AES 1112 have a triple redundant structure for
monitoring guard doors. A first fault can lead to a failure of one of the
three channels, whereby the two other channels maintain their safe
function. This also applies in case of a second fault. In this way, the
requirements in case of fault to EN 60947-5-3 are fulfilled. Only when
a third fault occurs, a hazardous situation can be created, when the
three accepted faults lead to the actuation of the output relay. As the
safety-monitoring modules do not automatically recognise the faults, a
regular check of the system is recommended. The test intervals must
be adjusted to the specific application (hazard level, mechanical and
electrical stress).
If the safety guard is opened, the enabling path of the safety-monitoring
module will open. The machine is stopped.
Inputs
AES 1102: C/S14/S22/S32
Connect the safety switch with two NC contacts and one
NO contact to input S14/S22/S32
AES 1112: S1- C/S14/S22/S32; S2- C/S14/S22/S32
Connect the safety switch with two NC contacts and one
NO contact to input S14/S22/S32
Outputs
Enabling paths 13-14: NO contacts for safety functions
6. Set-up and maintenance
6.1 Functional testing
The safety function of the safety-monitoring module must be tested.
The following conditions must be previously checked and met:
1. Correct fitting of the safety-monitoring module
2. Fitting and integrity of the power cable
6.2 Maintenance
In the case of correct installation and adequate use, the safety-
monitoring module features maintenance-free functionality.
A regular visual inspection and functional test, including the following
steps, is recommended:
• Check the correct fixing of the safety monitoring module
• Check the cable for damage.
The device has to be integrated into the periodic check-ups
according to the Ordinance on Industrial Safety and Health,
however at least 1x/year.
Damaged or defective components must be replaced.
7. Disassembly and disposal
7.1 Disassembly
The safety monitoring module must be disassembled in the de-
energised condition only.
7.2 Disposal
The safety monitoring module must be disposed of in an appropriate
manner in accordance with the national prescriptions and legislations.
8. Appendix
8.1 Wiring examples
The application examples shown are suggestions. They however do not
release the user from carefully checking whether the switchgear and its
set-up are suitable for the individual application.
The wiring diagram is shown with guard doors closed and in a de-
energised condition. Inductive loads (e.g. contactors, relays, etc.) are
to be provided with suitable interference suppression circuitry. Do not
connect additional loads to terminal S..