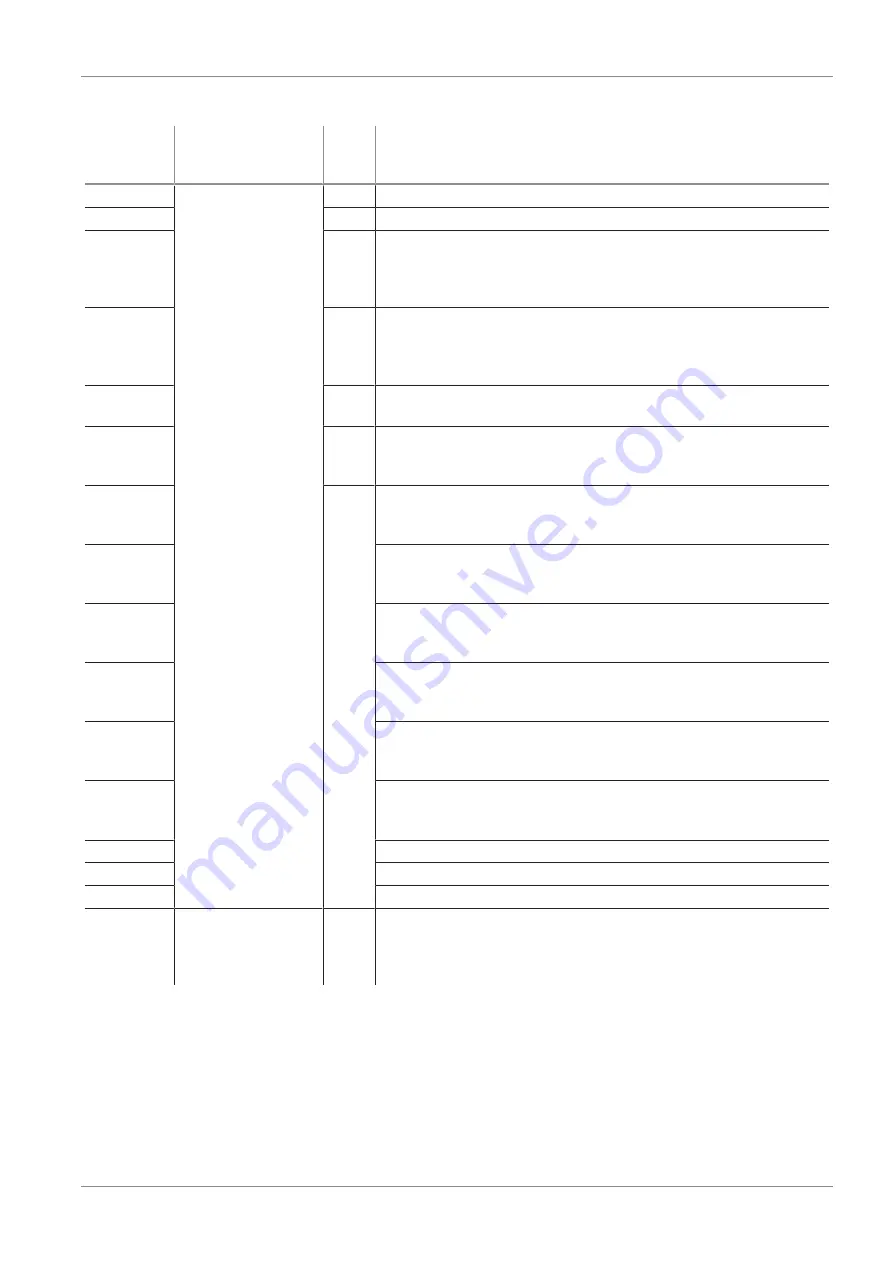
Installation
EN-US · 30.30.01.02599 · 00 · 07/21
21 / 40
6.4.3 Use of the Different Ports
PLC termi-
nal
number
Connection
Type
Application
01
Open cable end
24 V
02
Mass
03
DI
24 V = close gripper
The gripper closes according to the gripper position selected
manually on the control panel (position -2 to 3). Default set-
ting: -1 (close 38.5 mm)
2)
04
DI
24 V = open gripper
The gripper opens according to the gripper position selected
manually on the control panel (position -2 to 3). Default set-
ting: 1 (25 mm open)
2)
05
AI
0 to 10 V analog input
The gripper is infinitely variable for opening/closing
06
DO
Feedback from the valve
24 V = pressure reached
0 V = pressure changed/movement to new position
AI6
DI
24 V = the gripper position goes to “-2” (can be selected in in-
crements of 1 between 25 and 50)
3)
Default setting: 40 (43 mm open)
2)
AI7
24 V = the gripper position goes to “-1” (can be selected in in-
crements of 1 between 25 and 50)
3)
Default setting: 43 (38.5 mm open)
2)
AI8
24 V = the gripper position goes to “0” (fixed gripper position
in neutral position)
3)
Default setting: 50 (neutral position)
2)
AI9
24 V = the gripper position goes to “1” (can be selected in in-
crements of 1 between 50 and 100)
3)
Default setting: 80 (38.5 mm closed)
2)
AI10
24 V = the gripper position goes to “2” (can be selected in in-
crements of 1 between 50 and 100)
3)
Default setting: 90 (42 mm closed)
2)
AI11
24 V = the gripper position goes to “3” (can be selected in in-
crements of 1 between 50 and 100)
3)
Default setting: 100 (45 mm closed)
2)
DI0
24 V = neutral position
DI2
1)
24 V = vacuum suction cup active
DI3
1)
24 V = blow-off active
USB inter-
face
USB-B
USB
USB-B interface for connecting the controller to the software
via the computer. The use of the USB connection and the soft-
ware is described in chapter 6.6.
Accessories, connection cable: Part no. 21.04.05.00828
1)
Only 10.01.51.00011 controller for OFG…SPB4-30. The signal should be maintained until the next
change.
2)
Position of the diagrams in chapters 4.3 and 4.4
3)
The designation of the gripper positions depends on the designation within the software and the con-
trol panel on the control unit