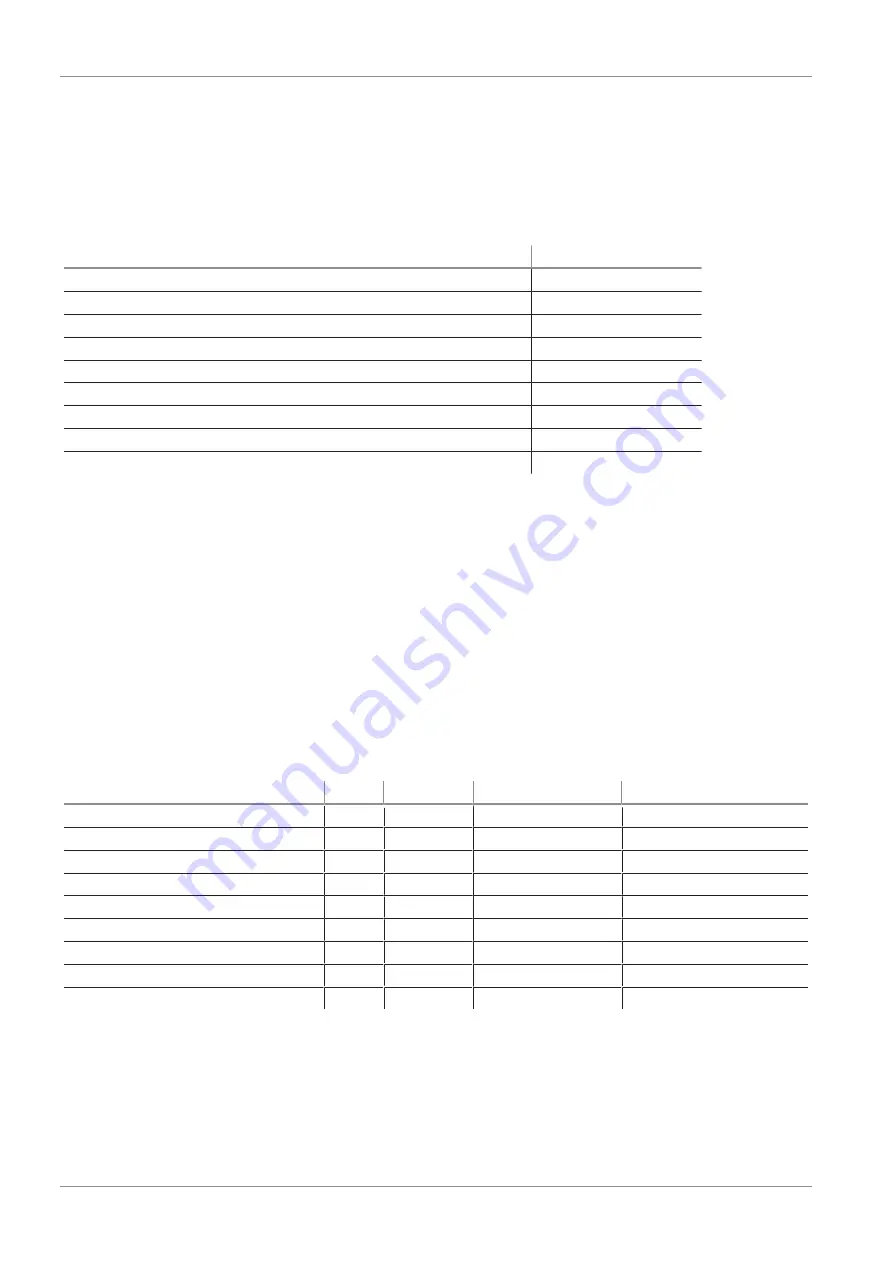
Technical Data
26 / 94
EN-US · 30.30.01.02237 · 00 · 04/20
The letter “a” stands for the number of IO-Link modules installed in the terminal.
The letter “b” stands for the number of DI modules installed in the terminal.
All dimensions given in millimeters [mm].
4.3.3 Terminal Mass
The mass of a terminal is determined by the masses of the individual components:
Individual components
Mass [g]
ProfiNet-D bus system
150
IO-Link class B bus system
150
EtherNet/IP bus system
150
EtherCAT bus system
150
IO-Link master
160
DI module for Ethernet
130
Ejector disc
240
Cover and clamping elements for 1 to 9 ejector discs
Approx. 230
Cover and clamping elements for 10 to 16 ejector discs
Approx. 350
The approximate mass of one terminal amounts to:
•
with up to 9 ejector discs
m = approx. 230 g + 150 g + (n*240) g + (a*160) g + (b*130) g
•
with 10 to 16 ejector discs
m = approx. 350 g + 150 g + (n*240) g + (a*160) g + (b*130) g
The letter “n” stands for the number of ejector discs installed in the terminal.
The letter “a” stands for the number of IO-Link modules installed in the terminal.
The letter “b” stands for the number of DI modules installed in the terminal.
The order confirmation indicates the exact mass of the respective terminal.
4.3.4 Factory Settings
The factory settings relate to the particular ejector of the Compact terminal SCTSi.
Parameter
(dec)
(hex)
Value
Description
Limit value switching point H1
100
0x0064
–750 mbar
—
Hysteresis h1
101
0x0065
150 mbar
—
Limit value switching point H2
102
0x0066
-550 mbar
—
Hysteresis h2
103
0x0067
10 mbar
—
Blow-off pulse duration
106
0x006A
200 ms
—
Permitted evacuation time
107
0x006B
2000 ms
—
Permitted leakage
108
0x006C
250 mbar/s
—
Air saving function
109
0x006D
0x02
Control active
Blow-off mode
110
0x006E
0x00
Externally controlled