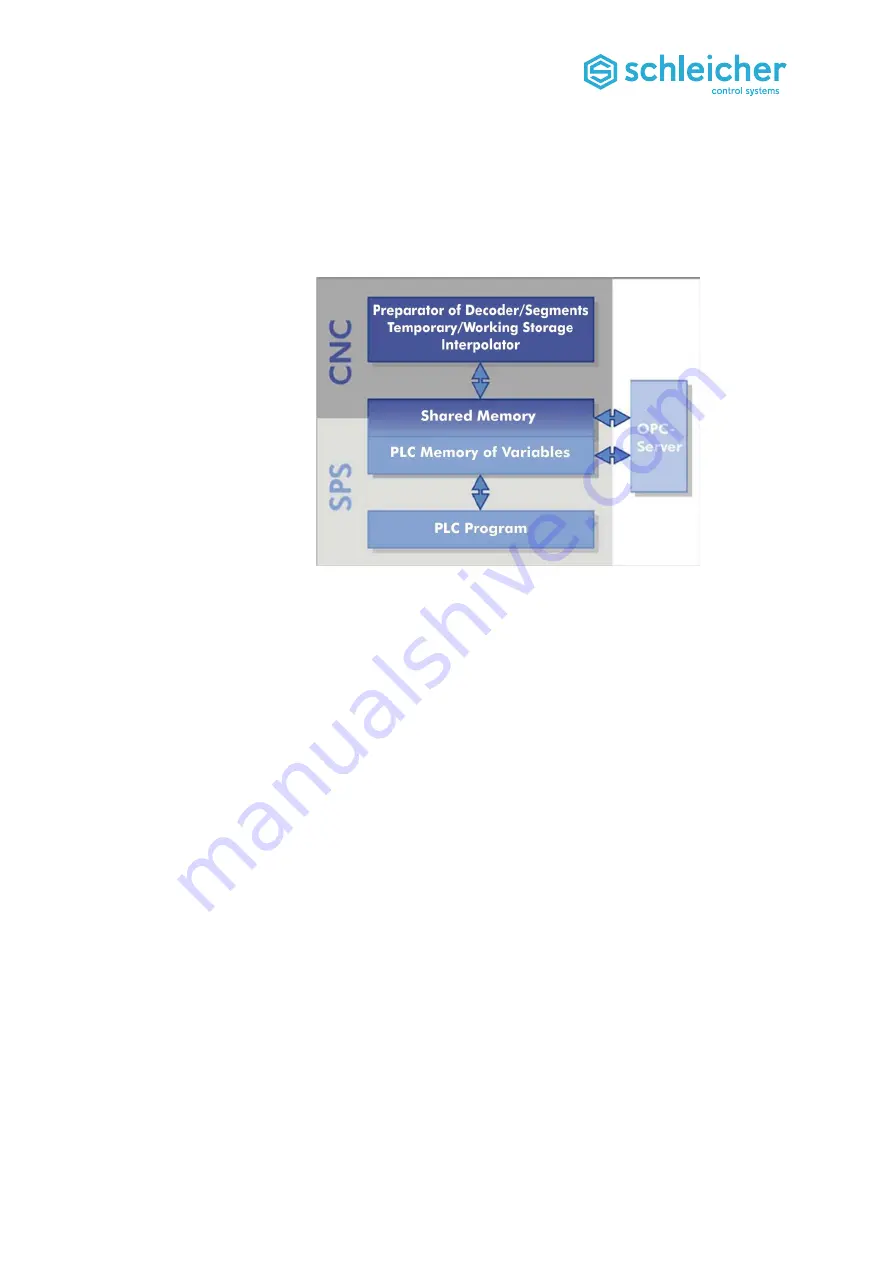
The Shared RAM
Operating Manual XCA 1100 / XCA 1200
●
Version 12/17
133
10
The Shared RAM
The shared RAM connects the sequence control of the PLC and the
motion functions of the CNC. Both controller systems operate
synchronously for data exchange on the memory and the PLC can
take on a master function. Visualisation systems are also integrated
via OPC in the communication.
Figure127:
Shared RAM as
connection of
PLC and CNC
The close link between the CNC and the PLC system now enables
you to carry out complex processes which would not be possible with
separate CNC and PLC controllers. The classic PLC interface enables
PLC functions in NC programs, e.g. the setting and requesting of PLC
flags. The synchronisation of the PLC task with the CNC position
control provides further options:
There are no waiting times or communication overhead.
The PLC can monitor all actions of the CNC
The CNC output setpoints via the PLC.
The PLC can specify the CNC management sizes in the position
control cycle
10.1
Variables and Tasks
Shared RAM data takes the form of variables as per IEC 61131-361131,
which are declared as global variables during configuring in the
MULTIPROG programming system. They are accessible to the OPC
server as standard and are displayed in the Schleicher dialog operating
tool.
In the multi-tasking operating system, PLC task 6 is synchronised with
the interpolation task of the CNC controller. The cycle time of task 6 is
then oriented on the interpolation cycle of the CNC.