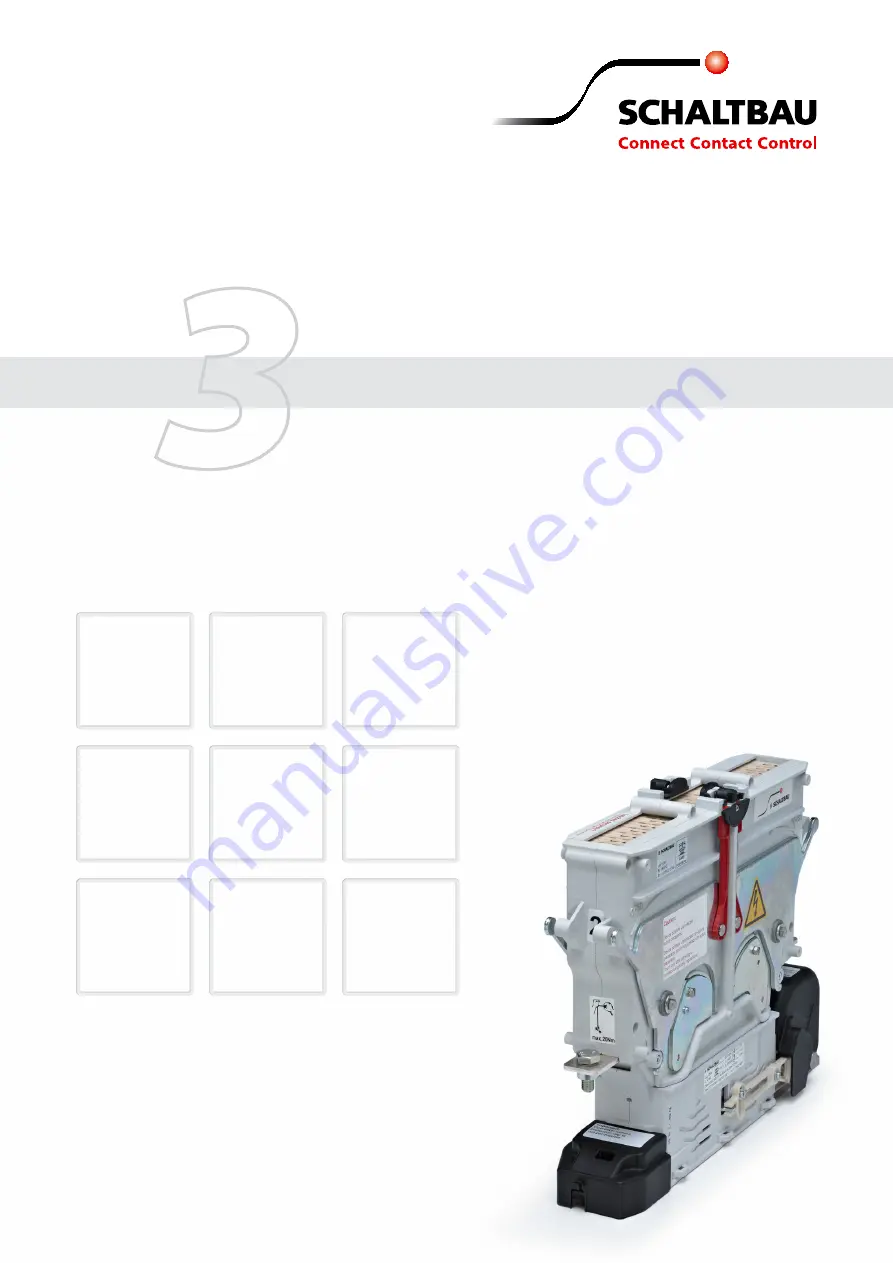
3
Inhalt
Rundsteckverbinder für Spezialanwendungen, Baureihe SB
5-polig + PE Flanschstecker, Kabeldose
6-polig Flanschdose, Kabelstecker
14-polig Flanschstecker, Kabeldose
Werkzeuge Ausdrückwerkzeuge AWZ-A und AWZ-C/H, Crimpzange CWZ-600
Kontakte Stecker: Crimpkontakte, Dosen: Lötkontakte
Contactors
Contactors
CT1115/04, CT1130/04 series
Single Pole NO
Power Contactors
for AC and DC
Manual C20/04-M.en