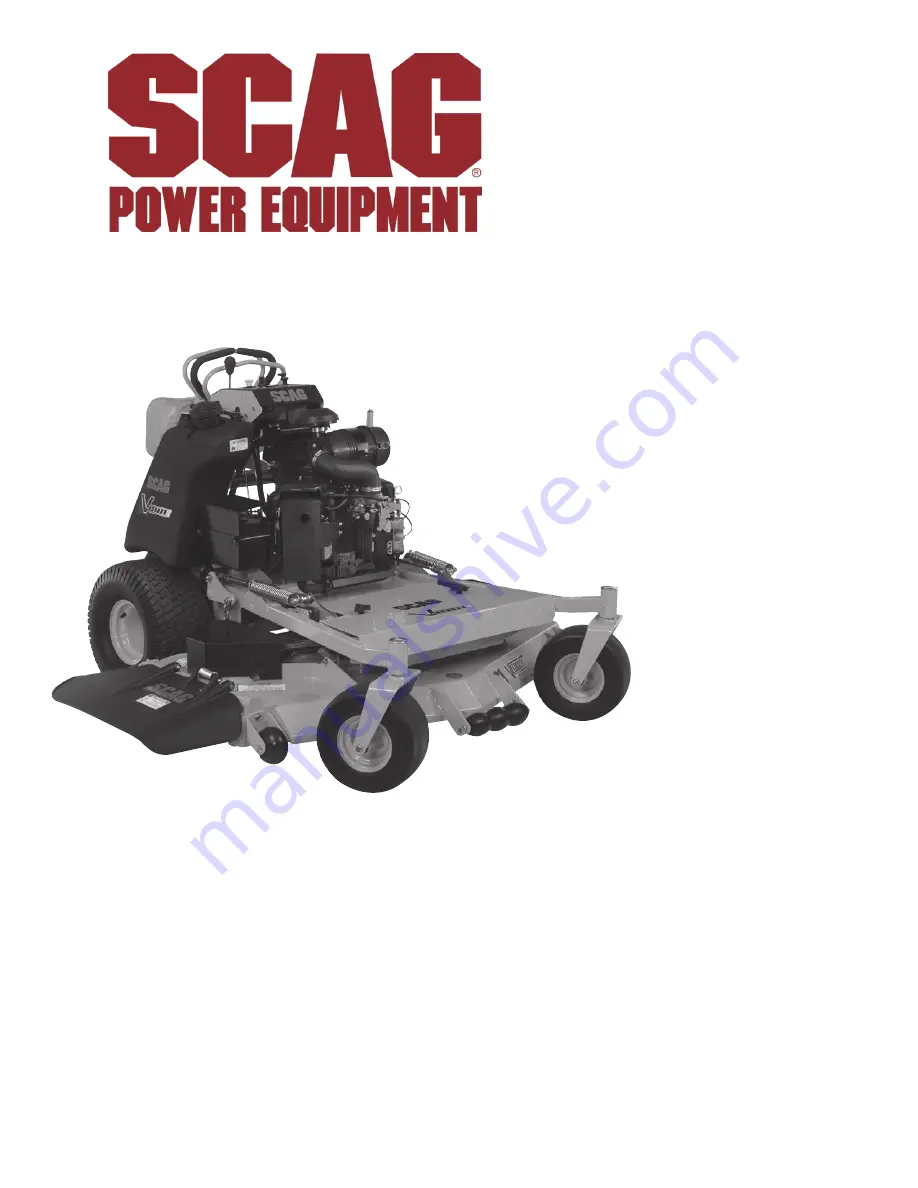
OPERATOR’S
MANUAL
Part No. 03321
Printed 9/12
Printed in USA
© 2012
Scag Power Equipment
Division of Metalcraft of Mayville, Inc.
Congratulations on owning a Scag mower! This manual contains the
operating instructions and safety information for your Scag mower. Reading
this manual can provide you with assistance in maintenance and adjustment
procedures to keep your mower performing to maximum efficiency. The
specific models that this book covers are listed on the inside cover. Before
operating your machine, please read all the information enclosed.
V-Ride
Model:
SVR36A-600FX
SVR48V-691FX
SVR52V-730FX
SVR61V-801FX
Summary of Contents for SVR36A-15FS
Page 45: ...41 R Section 7 NOTES...
Page 47: ...43 R Section 8...
Page 74: ...2012 Scag Power Equipment Division of Metalcraft of Mayville Inc...