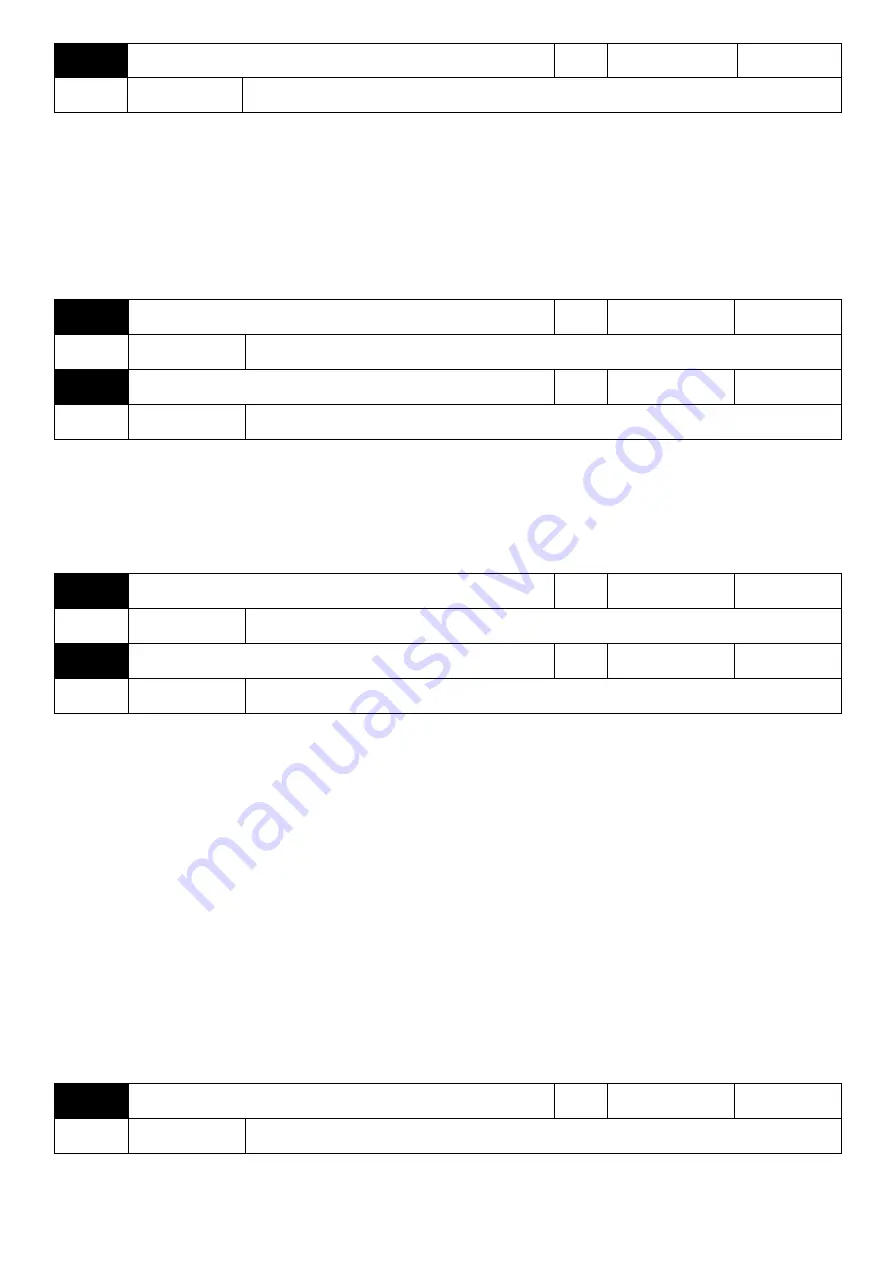
138
17-03
Torque digital setting in torque control mode
Factory setting
150.0%
Setting range -200.0%
~
200.0%
Used to select the torque setting source.
The torque setting adopts a relative value, and 100.0% corresponds to the rated torque of the inverter. Setting
range-200.0%~200.0%, indicating that the maximum torque of the inverter is 2 times the rated torque of the
inverter.
When the torque setting source is selected from 1 to 7, 100% of communication, analog input, and pulse input
correspond to 17-03.
17-05
Torque control forward maximum frequency
Factory setting
50.00Hz
Setting range 0.00Hz
~
Max frequency (00-03)
17-06
Torque control reverse maximum frequency
Factory setting
50.00Hz
Setting range 0.00Hz
~
Max frequency (00-03)
It is used to set the maximum running frequency of inverter forward or reverse in torque control mode.
When the inverter torque control, if the load torque is less than the motor output torque, it will continue to rise, in
order to prevent accidents such as speeding of the mechanical system, the maximum speed of the motor during
torque control must be limited.
17-07
Torque control acceleration time
Factory setting
0.00s
Setting range 0.00s
~
65000s
17-08
Torque control Deceleration time
Factory setting
0.00s
Setting range 0.00s
~
65000s
In the torque control mode, the difference between the motor output torque and the load torque determines the
speed change rate of the motor and the load, so the motor speed may change rapidly, causing problems such as
excessive noise or mechanical stress. By setting the torque control acceleration and deceleration time, the motor
speed can be changed gently.
However, when quick torque response is required, the torque control acceleration/deceleration time needs to be
set to 0.00s. For example, two motors are connected by a hard connection to drive the same load. In order to
ensure that the load is evenly distributed, one inverter is set as the master to adopt the speed control mode, the
other inverter is the slave and uses torque control, the actual output torque of the master As the torque command
of the slave, the torque of the slave needs to quickly follow the master at this time, then the acceleration and
deceleration time of the torque control of the slave is 0.00s.
22 Control Optimization Parameters
22-00
DPWM switching upper limit frequency
Factory setting
8.00Hz
Setting range 0.00Hz
~
Maximum operating frequency
Only valid for V/f control.When the V/f is running, the wave transmission mode is lower than this value for the
7-segment continuous modulation mode, and the opposite is the 5-segment intermittent modulation mode.
Summary of Contents for S3100A Series
Page 1: ...S3100Aseries inverter General Open loop Vector Control IM User manual User Manual ...
Page 24: ...20 Size 5 Unit mm S3100A 4T45G 55P 4T110G Size 6 Unit mm S3100A 4T110G 132P 4T160G 185P ...
Page 25: ...21 Size 7 Unit mm S3100A 4T185G 200P 4T220G Size 8 Unit mm S3100A 4T220G 250P 4T315G ...
Page 26: ...22 Size 9 Unit mm S3100A 4T315G 355P 4T400G 450P Size 10 Unit mm S3100A 4T450G 500P 4T500G ...