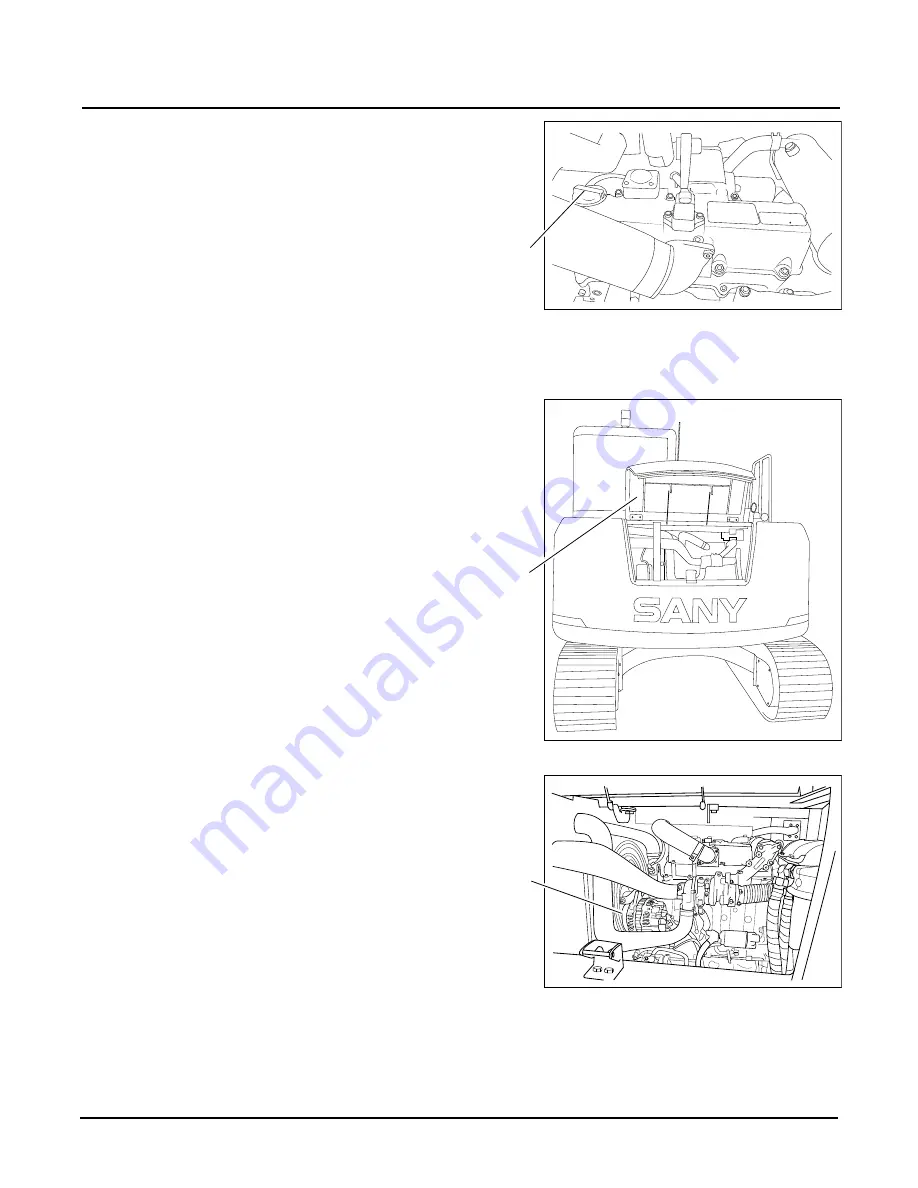
Maintenance Procedures
SY75C Excavator OMM
5-42
Operation and Maintenance Manual — 0220
SANY
5. If necessary remove oil filler cap (d), add oil as needed,
then reinstall the cap.
6. Close the engine cover.
Engine V Belts - Check
1. Open engine cover (a).
2. Locate V belts (b).
NOTE:
There are two V belts, one driving the alternator
and the other driving the air conditioning
compressor.
3. Compare the information here with the actual belt.
a. Abrasion
: The belt appears shiny, glazed or fabric is
exposed. This is a sign that the belt is in contact with
an object such as a flange or bolt.
b. Chunk out
: Chunks of rubber material have broken
off from the belt. At this stage, the belt can fail at
any moment. Heat, age and stress are the primary contributors.
NOTICE!
Do not overfill the engine with oil. Failure to
observe and follow this directive may result in
severe damage to the engine.
Fig. 5-52
d
a
Fig. 5-53
Fig. 5-54
b
Summary of Contents for SY75
Page 2: ......