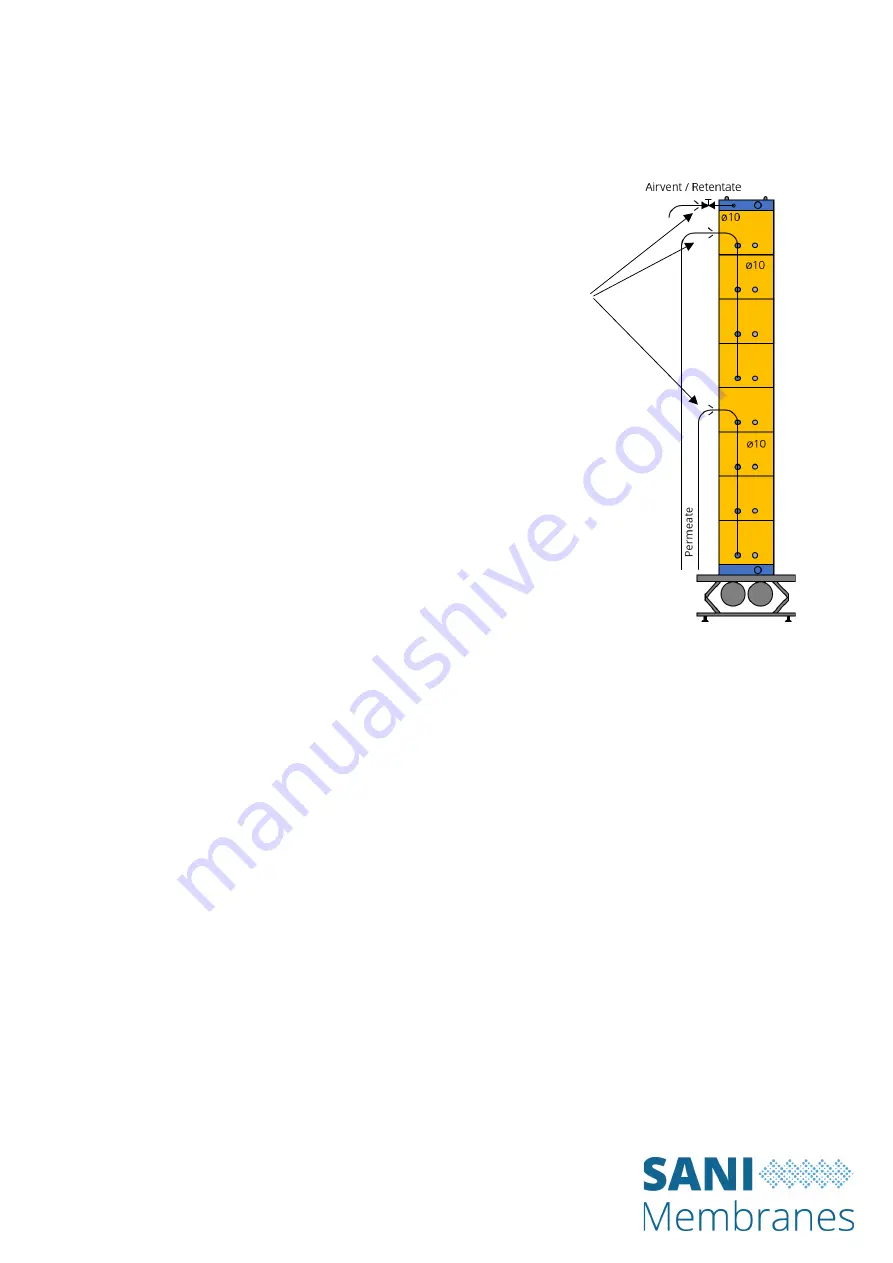
19
Version: 20221219
B.
Permeate system
The manifold is designed to avoid negative
transmembrane pressure (TMP) as this can cause
damage to the membrane modules. A negative TMP can
occur when reducing the feed pressure dramatically or
stopping the feed system quickly.
In microfiltration applications it is often key to have a
low, uniform TMP. To facilitate this the manifold for
microfiltration systems leads the permeate up along the
modules, as shown in the illustration to the right. To
enable drainage of the permeate side a drain valve can
be included at the bottom of the permeate manifold.
The permeate rate may be controlled by using a positive
displacement type pump on the permeate line. This will
restrict the permeate flow and will enable unique process control at low uniform TMP during
microfiltration. Read more about this in Section E below (
“
Examples of membrane filtration
process configurations
”
).
For ultrafiltration applications the pressure conditions are less critical and the manifold can
instead be designed to lead the permeate down along the modules. A vent valve can
optionally be included at the top of the manifold to assist draining of the permeate side.
In general it is recommended to reduce the pressure drop in the permeate system by using a
larger diameter tubing between the Vibro-I and the collection tank.
Avoid
pressure
drop using
larger
diameter
tubing to
the
collection
tank