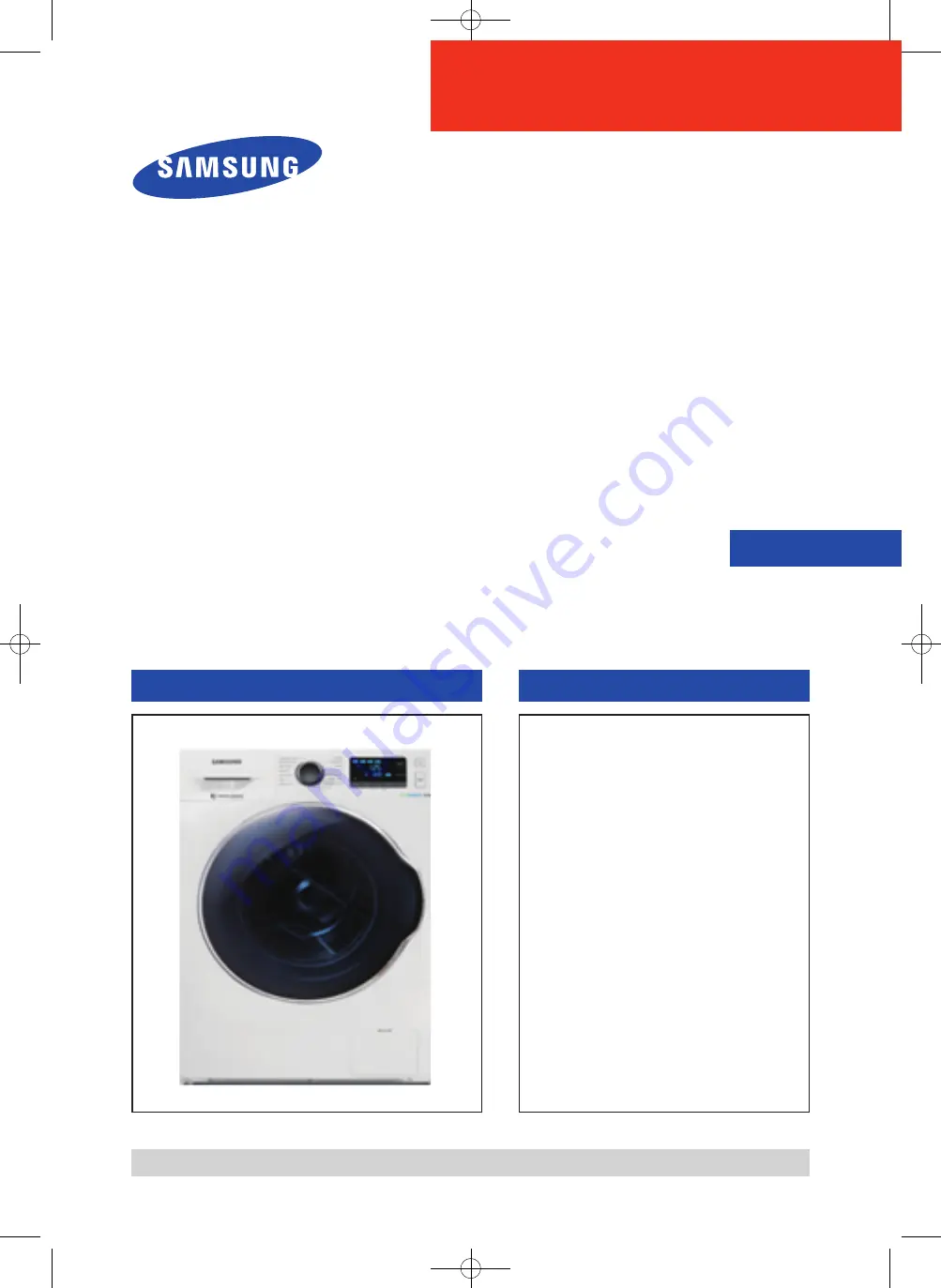
WASHING MACHINE (DRUM)
CONTENTS
SERVICE
Manual
WASHING MACHINE
DRUM TYPE
Basic Model
: WW90J6413CW/UA
(WW6000J PROJECT)
Model Name
: WW22K6800A*
Model Code
: WW22K6800AW/A2
(WW6800K PROJECT)
1. Safety Instructions
2. Features and Specifications
3. Disassembly and Reassembly
4. Troubleshooting
5. PCB Diagram
6. Wiring Diagram
7. Reference
WW22K6800AW-A2.indb 1
2015/12/3 16:08:23