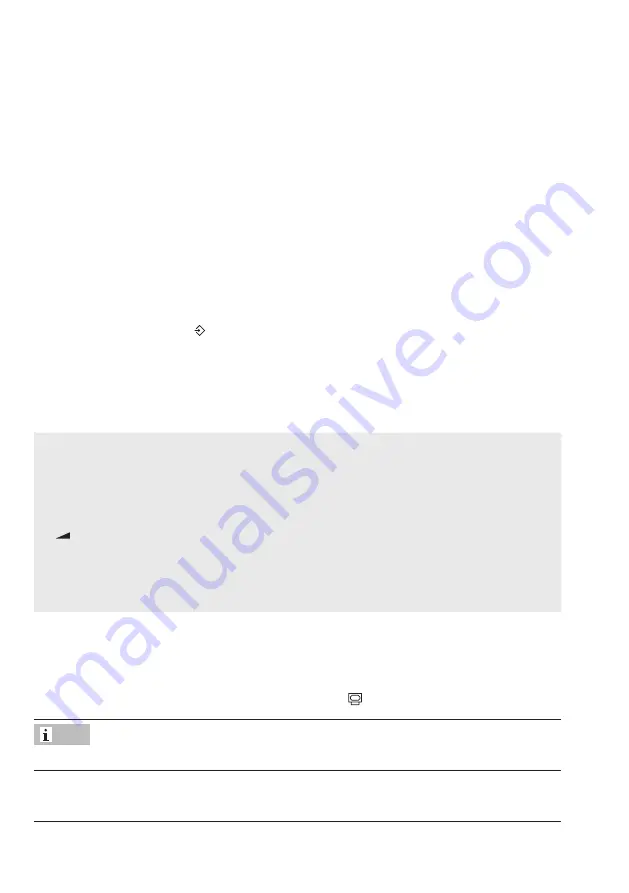
26
EB 5573 EN
Start-up
3.3
Changing parameters
Depending on the system code number selected and the activated functions, not all parame-
ters listed in the parameter list in the appendix (see section 13.2) might be accessible.
The parameters are grouped by topics:
−
PA1:
HC1 (heating circuit 1)
−
PA2:
HC2 (heating circuit 2)
−
PA4:
DHW circuit
−
PA5:
System-wide
−
PA6:
Communication parameters
1.
Turn the rotary switch to (parameter and configuration level).
Reading:
0 0 0 0
2.
Enter valid key number [
q
].
3. Confirm key number [
Û
].
Reading:
PA_
4.
Select parameter level [
q
].
5. Open parameter level [
Û
].
6. Select parameter [
q
].
7. Activate editing mode for the parameter [
Û
].
blinks.
8.
Change parameter [
q
].
9. Confirm parameter [
Û
].
Î
To set further parameters in the opened parameter level, repeat the steps 6 to 9.
10.
Select
End
[
q
].
11.
Exit parameter level [
Û
].
Î
To set further parameters in another parameter level, repeat the steps 4 to 9.
12.
Turn the rotary switch back to normal switch setting (information level).
All parameter settings are saved in a non-volatile memory in the controller.
Note
Summary of Contents for TROVIS 5573
Page 144: ...144 EB 5573 EN Key number 1732...