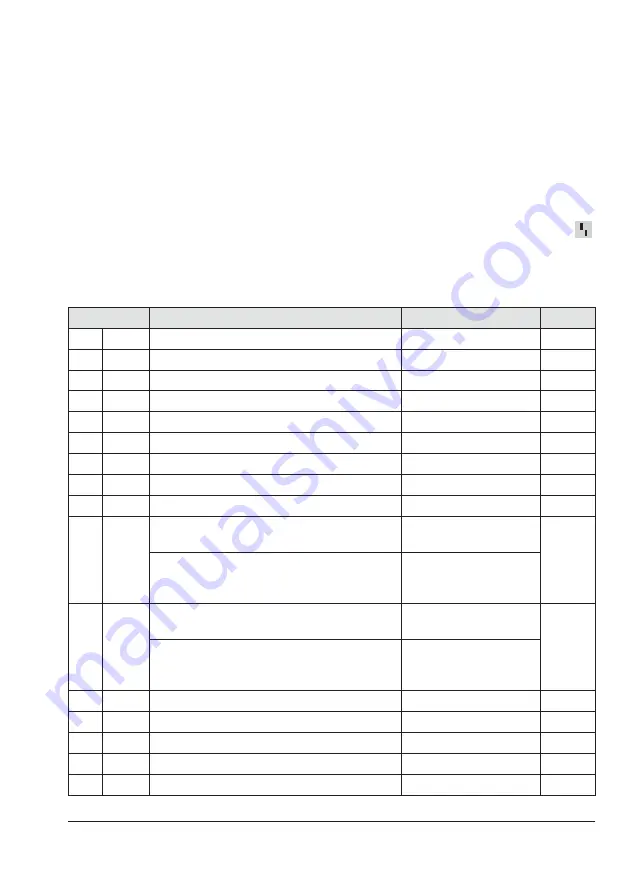
EB 8332-2 EN
9-1
Malfunctions
9 Malfunctions
9.1 Troubleshooting
9.1.1 Error messages
Active errors are added at the end of the top operating level. An error is indicated by the
display blinking and alternating between the start screen and the indicated error with the
error icon. If several errors have occurred, only the error with the highest priority is shown on
the start screen. In the operating level, the active errors appear on the display after Code 20.
Error messages in order of their priority:
Error
Message
Type of error
Priority
EF
ENDT Final test failed
Fatal error
1
E11 NTRV EEPROM error: no basic setting
Fatal error
2
E12
NCO
EEPROM error: no configuration
Fatal error
3
E08
PLAU Plausibility error
Fatal error
4
E06
MOT Motor or potentiometer not turning
Fatal error
5
E03
SWI
Both limit contacts are active
Fatal error
6
E04
SIN
Retracting of actuator stem canceled
Fatal error
7
E05 SOUT Extending of actuator stem canceled
Fatal error
8
E02
BLOC Blockage
Fatal error
9
E01
FAIL
Input signal failure
(application: positioner)
Fatal error
10
Input signal failure
(application: temperature closed-loop control
upon input signal failure)
Maintenance demanded
E07
SENS
Sensor failure
(application: PID controller)
Fatal error
11
Sensor failure
(application: temperature closed-loop control
upon input signal failure)
Maintenance demanded
E09
BUS
Bus failure
Fatal error
12
E14 NPOT EEPROM error: no potentiometer calibration
Maintenance demanded
13
E00 RUNT No initialization performed
Maintenance demanded
14
E13 NCAL EEPROM error: no calibration
Maintenance demanded
15
E15 NRUN EEPROM error: no transit time
Maintenance demanded
16
Summary of Contents for 3375
Page 6: ...Contents EB 8332 2 EN ...
Page 12: ...1 6 EB 8332 2 EN ...
Page 40: ...5 16 EB 8332 2 EN ...
Page 45: ...EB 8332 2 EN 6 5 Operation Fig 6 3 Housing cover of special version with three key operation ...
Page 46: ...6 6 EB 8332 2 EN ...
Page 63: ...EB 8332 2 EN 8 5 Setup 1 2 Fig 8 2 Manual override ...
Page 72: ...8 14 EB 8332 2 EN ...
Page 78: ...9 6 EB 8332 2 EN ...
Page 80: ...10 2 EB 8332 2 EN ...
Page 82: ...11 2 EB 8332 2 EN ...
Page 84: ...12 2 EB 8332 2 EN ...
Page 86: ...13 2 EB 8332 2 EN ...
Page 88: ...14 2 EB 8332 2 EN ...
Page 90: ...15 2 EB 8332 2 EN Certificates EU declaration of conformity ...
Page 122: ...16 32 EB 8332 2 EN ...
Page 125: ...EB 8332 2 EN 17 3 Service key number 1732 Customized key number ...
Page 126: ...17 4 EB 8332 2 EN ...
Page 127: ......
Page 128: ......
Page 129: ......