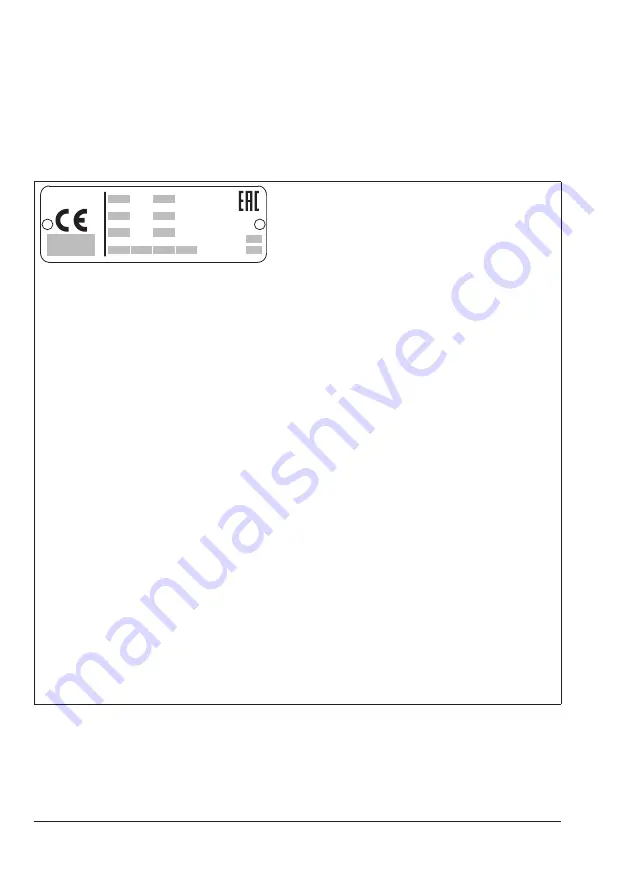
12
EB 8059 EN
Markings on the device
2 Markings on the device
2.1 Valve nameplate
6
8
12
13
10
11
14 15 16 17
1…5
9
SAMSON
20
Fig. 1:
Valve nameplate
1…5
PED (Pressure Equipment Directive), "Art. 4, Abs. 3"
ID of the notified body, fluid group and category
6
Type designation
8
Material
9
Year of manufacture
10
Valve size:
DIN: DN · ANSI: NPS · JIS: DN … A/B
11
Pressure rating:
DIN: PN · ANSI: CL · JIS: K
12
Order no. with modification index
For after-sales service orders: AA prefix
13
Position in order
For after-sales service orders: configuration ID
14
Flow coefficient:
DIN: K
VS
· ANSI: C
V
· JIS: C
V
15
Characteristic:
%: equal percentage · Lin: linear · NO/NC: quick opening
16
Seat-plug seal:
ME: metal
HA: carbide metal
ST: Stellite
®
facing
KE: ceramic
PT: soft seal with PTFE
PK: soft seal with PEEK
17
Seat code (trim material) · On request
20
Country of origin
Summary of Contents for 3259
Page 11: ...EB 8059 EN 11...
Page 33: ...EB 8059 EN 33...
Page 45: ...EB 8059 EN 45 Servicing...
Page 51: ...EB 8059 EN 51...
Page 54: ...54 EB 8059 EN...
Page 55: ...EB 8059 EN 55...