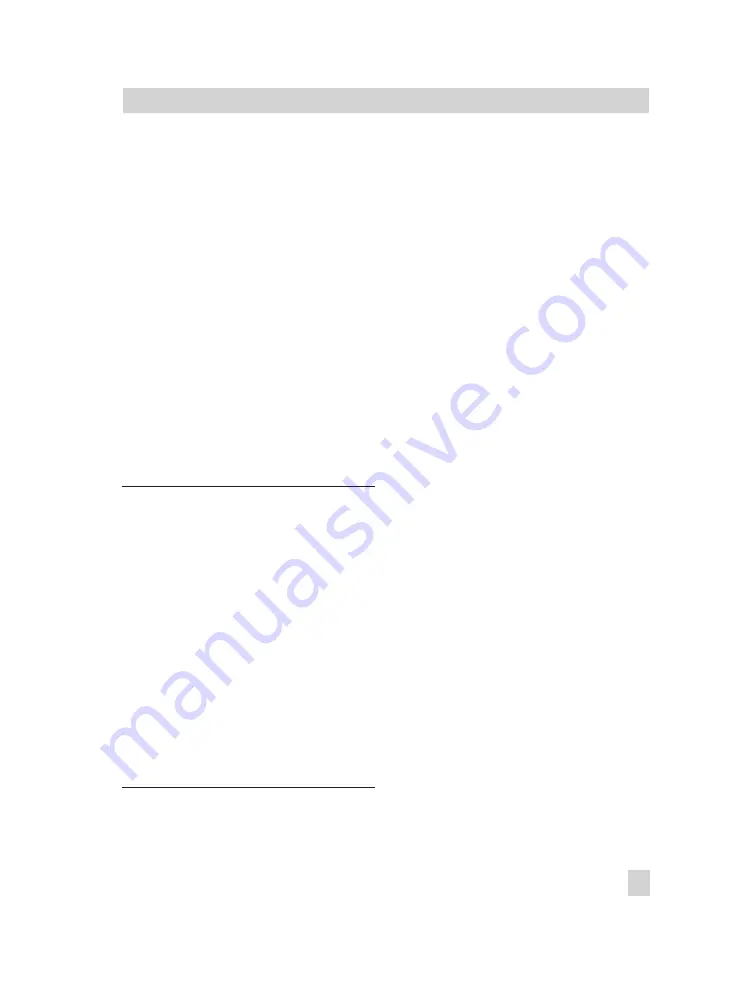
6
Maintenance
The control valves are maintenance free.
Nevertheless, they are subject to natural
wear, particularly at the seat, plug, and
packing. Depending on the operating condi-
tions, the valves need to be checked at regu-
lar intervals to avoid possible malfunctions.
If external leaks occur, check the packing or
balancing diaphragm and, if necessary, re-
place them.
If the tight shut-off of the valve is impaired,
this may be due to dirt or other foreign par-
ticles being caught between the seat and
plug or due to damaged facings.
We recommend to remove the affected com-
ponents, clean them thoroughly, and re-
place them, if necessary.
Caution!
When performing any maintenance work on
the valve, make sure the relevant section of
the plant has been depressurized and, de-
pending on the process medium, drained as
well. If necessary, allow the control valve to
cool down to reach ambient temperature.
Disconnect and lock the electrical supply as
well as any control signals to prevent any
danger posed by moving parts.
As valves are not free of cavities, remember
that residual process medium might still be
contained in the valve. This applies in par-
ticular to valve versions with a balancing
bellows.
We recommend to remove the valve from
the pipeline.
EB 5868-1 EN
13
Maintenance
Summary of Contents for 3214
Page 15: ...EB 5868 1 EN 15...