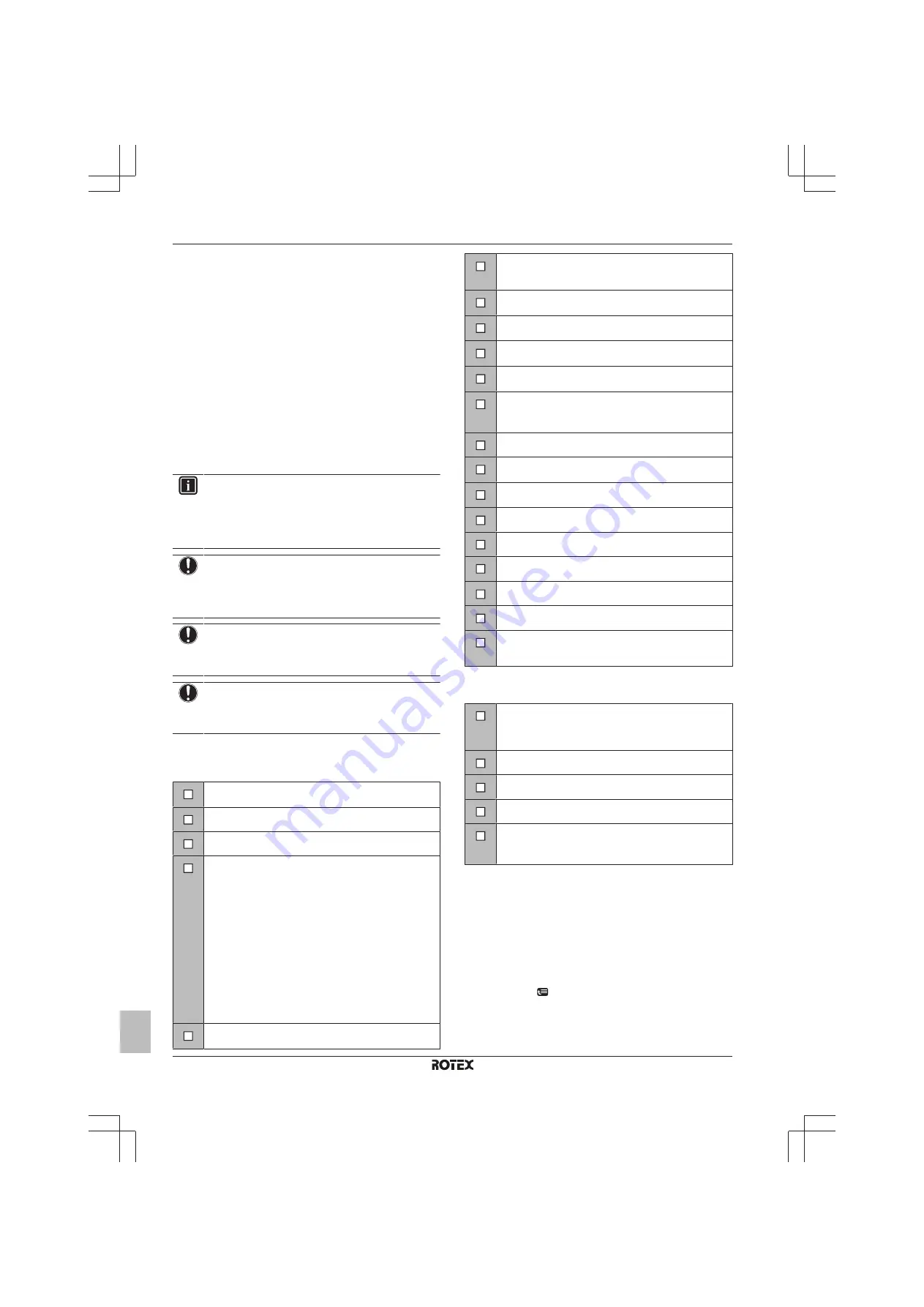
9 Commissioning
Installer reference guide
72
RRLQ004~008CA + RHBH/X04+08CB
ROTEX HPSU low temperature Bi‑bloc
4P384979-1 – 2015.01
9
Commissioning
9.1
Overview: Commissioning
This chapter describes what you have to do and know to
commission the system after it is configured.
Typical workflow
Commissioning typically consists of the following stages:
1
Checking the "Checklist before commissioning".
2
Performing an air purge.
3
Performing a test run for the system.
4
If necessary, performing a test run for one or more actuators.
5
If necessary, performing an underfloor heating screed dryout.
9.2
Precautions when commissioning
INFORMATION
During the first running period of the unit, the required
power may be higher than stated on the nameplate of the
unit. This phenomenon is caused by the compressor, that
needs a continuous run time of 50 hours before reaching
smooth operation and stable power consumption.
NOTICE
Before starting up the system, the unit MUST be energised
for at least 2 hours. The crankcase heater needs to heat
up the compressor oil to avoid oil shortage and
compressor breakdown during startup.
NOTICE
NEVER operate the unit without thermistors and/or
pressure sensors/switches. Burning of the compressor
might result.
NOTICE
Do NOT operate the unit until the refrigerant piping is
complete (when operated this way, the compressor will
break).
9.3
Checklist before commissioning
Do NOT operate the system before the following checks are OK:
You read the complete installation instructions, as
described in the
installer reference guide
.
The
indoor unit
is properly mounted.
The
outdoor unit
is properly mounted.
The following
field wiring
has been carried out according
to this document and the applicable legislation:
▪ Between the local supply panel and the outdoor unit
▪ Between indoor unit and outdoor unit
▪ Between the local supply panel and the indoor unit
▪ Between the indoor unit and the valves (if applicable)
▪ Between the indoor unit and the room thermostat (if
applicable)
▪ Between the indoor unit and the domestic hot water
tank (if applicable)
▪ Between the gas boiler and the local supply panel
(only applicable in case of hybrid system)
The system is properly
earthed
and the earth terminals
are tightened.
The
fuses
or locally installed protection devices are
installed according to this document, and have not been
bypassed.
The
power supply voltage
matches the voltage on the
identification label of the unit.
There are NO
loose connections
or damaged electrical
components in the switch box.
There are NO
damaged components
or
squeezed
pipes
on the inside of the indoor and outdoor units.
Depending on the backup heater type,
backup heater
circuit breaker
F1B on the switch box is turned ON.
Only for tanks with built-in booster heater:
The
booster heater circuit breaker
F2B on the
switch box is turned ON.
There are NO
refrigerant leaks
.
The
refrigerant pipes
(gas and liquid) are thermally
insulated.
The correct pipe size is installed and the
pipes
are
properly insulated.
There is NO
water leak
inside the indoor unit.
The
shut-off valves
are properly installed and fully open.
The
stop valves
(gas and liquid) on the outdoor unit are
fully open.
The
air purge
valve is open (at least 2 turns).
The
pressure relief valve
purges water when opened.
The
minimum water volume
is guaranteed in all
conditions. See "To check the water volume" in
"6.4 Preparing water piping" on page 24
9.4
Checklist during commissioning
The
minimum flow rate
during backup heater/defrost
operation is guaranteed in all conditions. See "To check
the water volume and flow rate" in
.
To perform an
air purge
.
To perform a
test run
.
To perform an
actuator test run
.
Underfloor screed dryout function
The underfloor screed dryout function is started (if
necessary).
9.4.1
To check the minimum flow rate
1
Confirm according to the hydraulic configuration which space
heating loops can be closed due to mechanical, electronic, or
other valves.
2
Close all space heating loops that can be closed (see previous
step).
3
Start the pump test run operation (see
4
Go to [6.1.8]:
> Information > Sensor information > Flow rate
to check the flow rate. During pump test run operation, the unit
can operate below this minimum required flow rate that is
needed during defrost/backup heater operation.