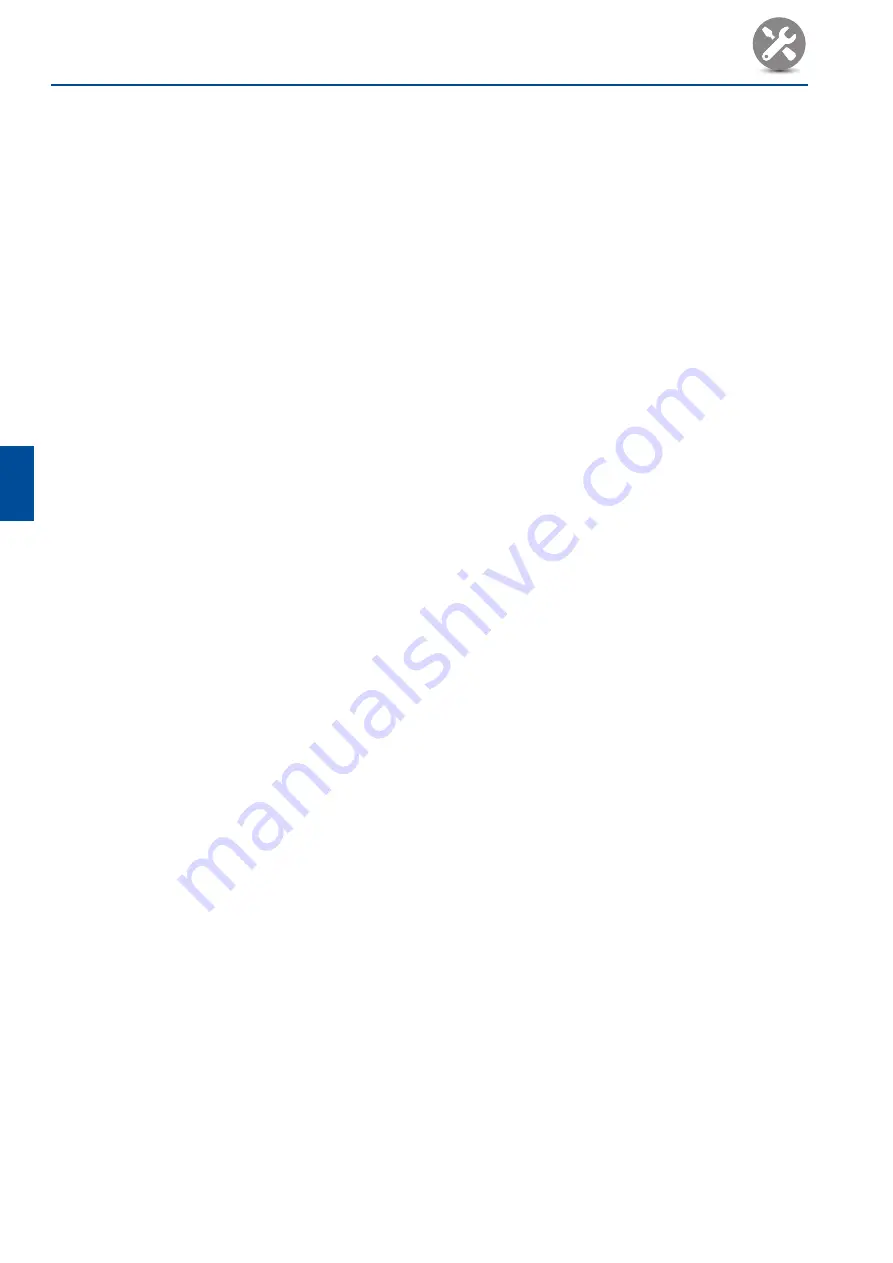
7
7‑2
OPERATIONAL MAINTENANCE
OL1D-SM-GB02D
1. Stand the vehicle on clean, level and stable ground.
2. Engage the parking brakes.
3. Select Neutral ‘N’.
4. Turn the ‘Body main’ switch to the OFF position.
Remove and retain the key.
5. Switch ignition off. Remove and retain the key.
6. Secure a sign ‘DO NOT START or OPERATE
VEHICLE’ to the steering wheel.
7. Lock all cab doors. Remove and retain the keys.
8. Thoroughly clean the area around the lamp in
which the bulb is to be replaced.
9. If necessary, place an access platform as close as
possible to the lamp.
10. Remove the lens.
11. Replace the bulb.
12. Fit the lens.
13. Check the operation of the lamp.
7
Operational maintenance
7.1
Body lamp bulb replacement
Technical data
1. Side marker lamps **
24 Volt / 3 Watt
2. Rear marker lamps **
24 Volt / 5 Watt
3. Tailgate high level lamp **
• Tail/Stop lamp
24 Volt / 6 / 24 Watt
• Turn indicator lamp
24 Volt / 21 Watt
• Rear fog lamp
24 Volt / 21 Watt
4. Tailgate rear lamp **
• Tail/Stop lamp
24 Volt / 6 / 24 Watt
• Turn indicator lamp
24 Volt / 21 Watt
• Reverse lamp
24 Volt / 5 Watt
• Rear fog lamp
24 Volt / 21 Watt
5. Number plate lamp **
24 Volt / 5 Watt
6. Warning beacon rotating
Halogen
24 Volt / 70 Watt
7. Warning beacon flashing
Halogen
24 Volt / 70 Watt
8. Work lamps
24 Volt / 24 Watt
** These lamps are LED lamps and do not feature
replaceable bulbs.
Note:
The basic procedure for replacing all the body
lamp bulbs is the same, the only differences being the
method of securing the lens to the lamp body and the
type of bulb fitted.
The appearance of lamps fitted to the vehicle may
differ from those shown in the illustrations shown on
page 7‑3.
LED lamps may be fitted in place of lamps with
replaceable bulbs.
Summary of Contents for Dennis Eagle Olympus
Page 2: ......
Page 6: ...iv CONTENTS OL1D SM GB02D This page intentionally left blank ...
Page 8: ...1 1 2 INTRODUCTION OL1D SM GB02D This page intentionally left blank ...
Page 10: ...1 1 4 INTRODUCTION OL1D SM GB02D This page intentionally left blank ...
Page 12: ...2 2 2 HEALTH AND SAFETY OL1D SM GB02D This page intentionally left blank ...
Page 26: ...3 3 2 DAILY CHECKS OL1D SM GB02D This page intentionally left blank ...
Page 50: ...3 3 26 DAILY CHECKS OL1D SM GB02D This page intentionally left blank ...
Page 52: ...4 4 2 HYDRAULIC SYSTEM OIL LEVEL OL1D SM GB02D This page intentionally left blank ...
Page 60: ...5 5 2 CLEANING OL1D SM GB02D This page intentionally left blank ...
Page 66: ...6 6 2 SCHEDULED MAINTENANCE OL1D SM GB02D This page intentionally left blank ...
Page 90: ...8 8 2 GENERAL SPECIFICATION DATA OL1D SM GB02D This page intentionally left blank ...
Page 96: ...8 8 8 GENERAL SPECIFICATION DATA OL1D SM GB02D This page intentionally left blank ...