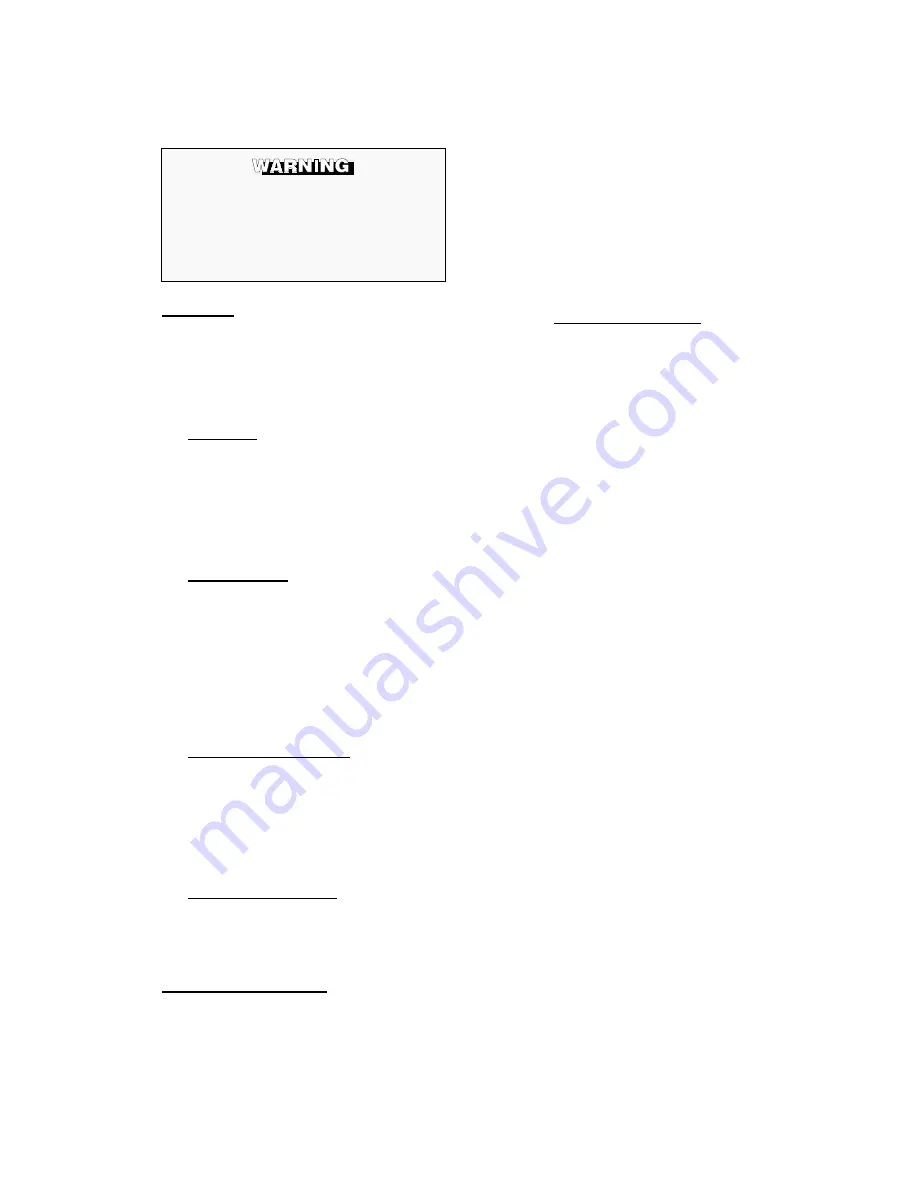
IB-106-340
5-1
SECTION V. TROUBLESHOOTING
Install all protective equipment covers
and safety ground leads after trouble-
shooting. Failure to install covers and
ground leads could result in serious
injury or death.
5-1.
GENERAL. The troubleshooting section describes
how to identify and isolate faults that may develop in
the Oxymitter 4000. Also, additional troubleshooting
information is provided in paragraph 5-5 for those units
with the optional SPS 4000. When troubleshooting the
Oxymitter 4000, reference the following information.
a.
Grounding. It is essential that adequate
grounding precautions are taken when installing
the system. Thoroughly check both the probe and
electronics to ensure the grounding quality has not
degraded during fault finding. The system provides
facilities for 100% effective grounding and the to-
tal elimination of ground loops.
b.
Electrical Noise. The Oxymitter 4000 has been
designed to operate in the type of environment
normally found in a boiler room or control room.
Noise suppression circuits are employed on all
field terminations and main inputs. When fault
finding, evaluate the electrical noise being gener-
ated in the immediate circuitry of a faulty system.
Also, ensure all cable shields are connected to
earth.
c.
Loose Integrated Circuits. The Oxymitter 4000
uses a microprocessor and supporting integrated
circuits (IC). If the electronics are handled roughly
during installation or located where subjected to
severe vibration, the ICs could work loose. Before
troubleshooting the system, ensure all ICs are fully
seated.
d.
Electrostatic Discharge. Electrostatic discharge
can damage the ICs used in the electronics. Be-
fore removing or handling the processor board or
the ICs, ensure you are at ground potential.
5-2.
ALARM INDICATIONS. The majority of the fault
conditions for the Oxymitter 4000 will be indicated
by one of the four LEDs referred to as diagnostic, or
unit, alarms on the operator’s keypad. An LED will
flash a code that will correspond to an error message.
Only one LED will blink at a time. An alarm code
guide is provided inside the screw cover for the
electronics. All alarm indications will be available
via the HART Model 275 handheld communicator
and Rosemount’s Asset Management software. When
the error is corrected and/or power is cycled, the
diagnostic alarms will clear or the next error on the
priority list will appear.
5-3.
ALARM CONTACTS.
a.
If autocalibration is not utilized, a common bi-
directional logic contact is provided for any of
the diagnostic alarms listed in Table 5-1. The as-
signment of alarms which can actuate this contact
can be modified to one of seven additional
groupings listed in Table 7-1.
The logic contact is self-powered, +5 VDC,
340 ohm series resistance. An interposing relay
will be required if this contact is to be utilized to
annunciate a higher voltage device, such as a
light or horn, and may also be required for cer-
tain DCS input cards. A Potter & Brumfield
R10S-E1Y1-J1.0K 3.2 mA DC or an equal inter-
posing relay will be mounted where the contact
wires terminate in the control/relay room.
b.
If autocalibration systems are utilized, the
bidirectional logic contact is utilized as a
“handshake” signal between the autocalibration
system (SPS 4000 or IMPS 4000) and is
unavailable for alarming purposes. The
following additional contacts are provided
through the autocalibration systems:
1. SPS 4000 and IMPS 4000, 1-4 probes.
(a)
One contact closure per probe from the
control room to the SPS 4000 or IMPS
4000 for “calibration initiate”.
(b)
One contact output per probe from the
SPS 4000 or IMPS 4000 to the control
room for “in calibration” notification.
(c)
Once contact output per probe from
the SPS 4000 or IMPS 4000 to the
control room for “calibration failed”
notification. (Includes output from
pressure switch indicating “cal gas
bottles empty”).
Summary of Contents for Oxymitter 4000
Page 19: ...IB 106 340 xv ...