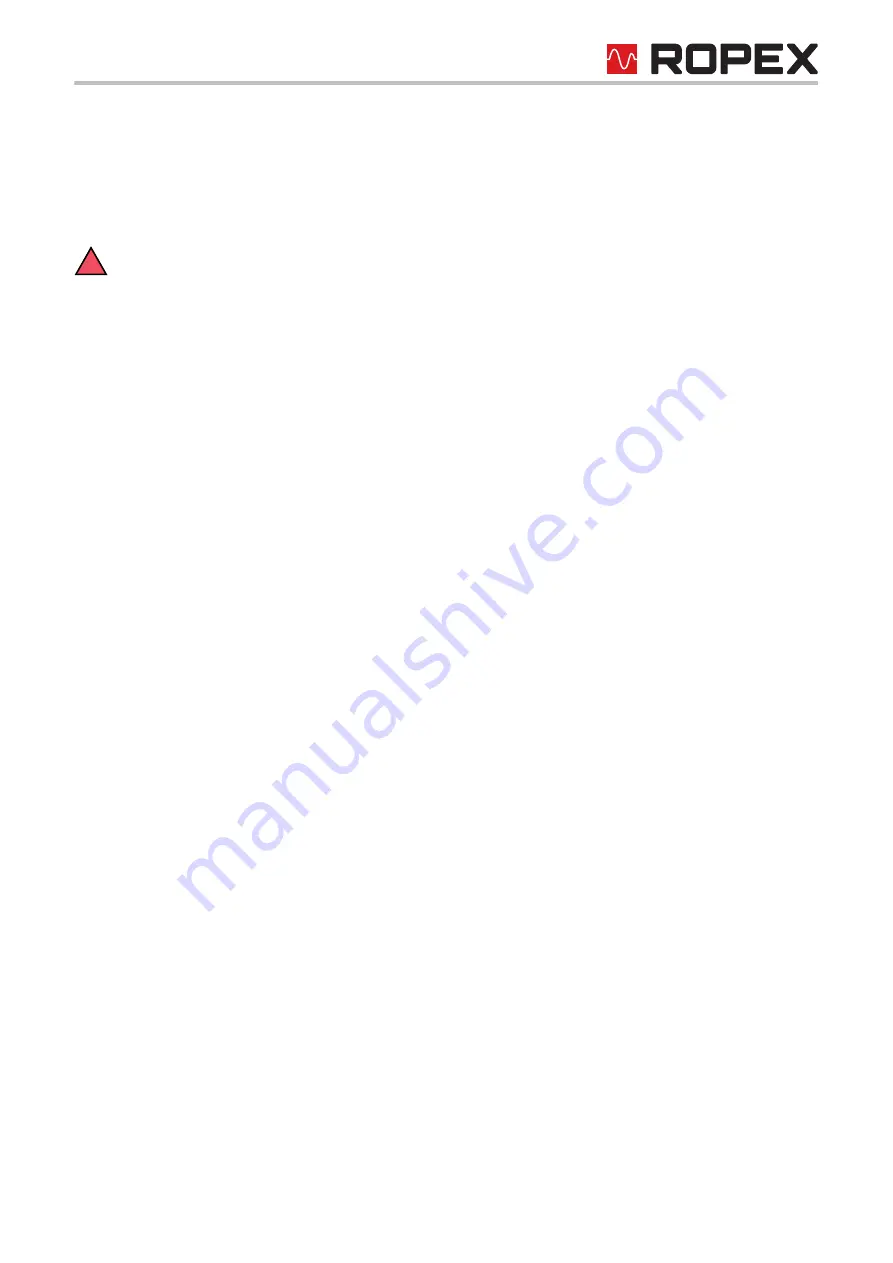
Device functions
Version 1
RES-5006
Page 35
8.7.8
Data format
The format of the cyclically replaced process data (
section 8.4 "PROFIBUS protocol" on page 22) can be
changed. Depending on the type of PROFIBUS master used, it may be necessary to switch the high byte
(bits 15…8) and low byte (bits 7…0) against each other.
For Siemens controllers, the setting “Low/high byte (Motorola)” is recommended.
8.7.9
Error number format
The length of the error number in the cyclical data is set with this parameter. Selection is possible between 4-bit
and 10-bit (
section 8.4 "PROFIBUS protocol" on page 22). The “4-bit” setting generates 2-digit error numbers
in the range 1…13. The “10-bit” setting generates more detailed 3-digit error numbers (
8.7.10 Automatic phase correction (AUTOCOMP)
In special sealing applications, it may be necessary to compensate the phase displacement between the U
R
and
I
R
measurement signals (
ROPEX application report). Use of the AUTOCOMP function can be necessary here.
The AUTOCOMP function must be released for use in the parameter data (
section 8.7 "Parameter data" on
page 32) or through the DPV1 protocol expansion (
section 8.8 "DPV1 protocol expansions" on page 40)
(standard setting: AUTOCOMP off).
The following settings are possible:
1.
“Off”
(factory setting)
AUTOCOMP function switched off.
2.
“On”
The AUTOCOMP function is carried out when the AUTOCAL function (
zeroing (AC)" on page 26) has been called up quickly twice in sequence. The pause between the end of the
first and start of the second execution of AUTOCAL must be less than 2.0 seconds. The second execution of
AUTOCAL lasts only about 2.0 seconds and contains the AUTOCOMP function.
If the pause between the two executions is longer than 2.0 seconds, the normal AUTOCAL function is carried
out the second time.
!