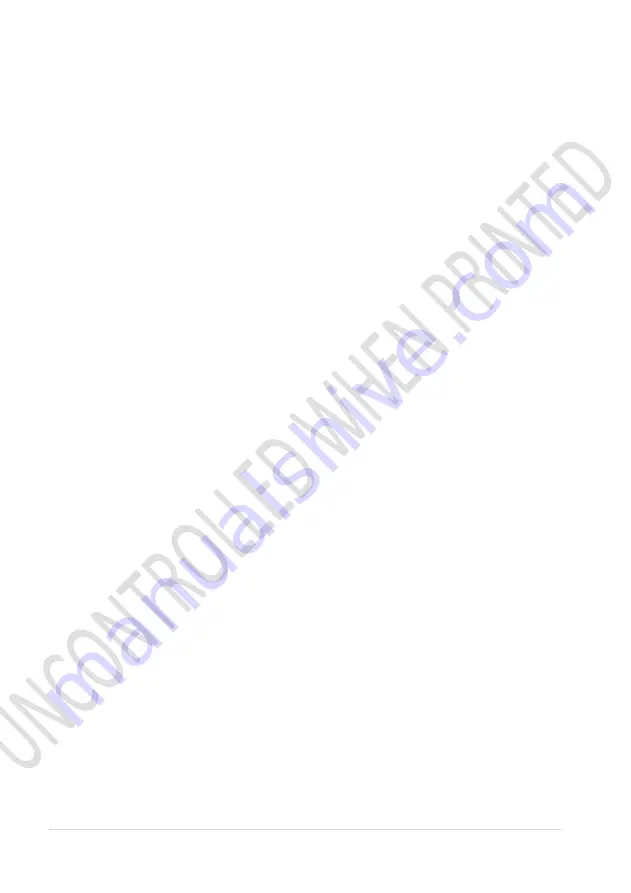
Operating and Maintenance Manual
20 |
P a g e
D e c a p p e r O & M M a n u a l R e v D
Prior to use, all components should be wiped clean, and all traces of oil /
grease removed using degreaser and a clean, lint free cloth.
➢
Pre-Start Checks
Prior to use, the following checks should be done.
•
Visual inspection, check the power lead is in good condition and is
clear of any rotating equipment, check the connecting hose is
straight with no kinks.
•
The Decapper has the correct calibre conversion installed, the drop
tube is adjusted correctly and the casefeeder, connecting hose and
Decapper are clear of any cases.
•
Check the power supply is safe and circuit breakers are functioning
correctly.
•
The gearbox does not have any oil leaks.
•
The switch turns the Decapper on / off / reverse as required.
•
The drop tube and flexible hose is clear of rubbish, tumbling media
or stuck cases.
•
The case feeder has the correct cases for the conversion and is
operating in accordance with the
manufacturer’s
manual.
•
Put a few drops of light machine oil on the spherical bearings and
guide rails
➢
Gearbox and Motor Maintenance
In normal domestic use applications, the gearbox or motor is unlikely to ever
require any maintenance. The gearbox is sealed for life and in non-
commercial applications is not expected to require oil changes for many
years.
The Decapper motor is fitted with carbon brushes, and these are a normal
wear item and are expected to require replacement at after processing
around 1,000,000 cases (give or take a few
…. lol
), replacement brushes are
available from Rollsizer.com. With normal domestic use the brushes should
last for years if not decades.