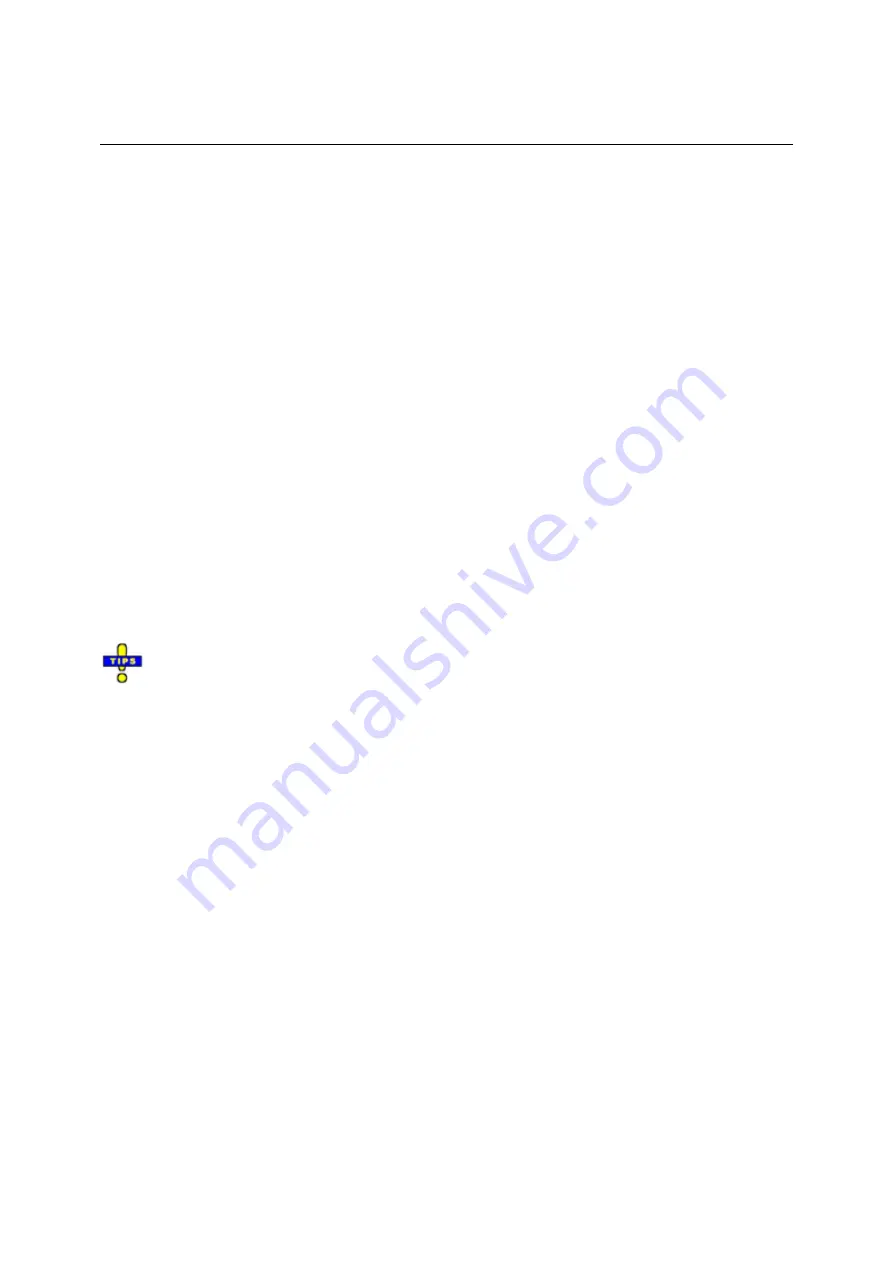
Calibration Overview
R&S
®
ZVA/ZVB/ZVT
1145.1084.12 3.36
E-1
Calibration Overview
Calibration is the process of eliminating systematic, reproducible errors from the measurement results
(system error correction). The process involves the following stages:
1. A set of calibration standards is selected and measured over the required sweep range. For
many calibration types the magnitude and phase response of each calibration standard (i.e. its
S-parameters if no system errors occur) must be known within the entire sweep range. In some
calibration procedures (TRL, TNA, TRM), part of the characteristics of the standards can be
auto-determined due to implicit redundancy (self-calibration).
2. The analyzer compares the measurement data of the standards with their known, ideal
response. The difference is used to calculate the system errors using a particular error model
(calibration type) and derive a set of system error correction data.
3. The system error correction data is used to correct the measurement results of a DUT that is
measured instead of the standards.
Calibration is always channel-specific because it depends on the hardware settings, in particular on the
sweep range. The means that a system error correction data set is stored with the calibrated channel.
The analyzer provides a wide range of sophisticated calibration methods for all types of measurements.
Which calibration method is selected depends on the expected system errors, the accuracy
requirements of the measurement, on the test setup and on the types of calibration standards available.
Due to the analyzer's calibration wizard, calibration is a straightforward, menu-guided process.
Moreover, it is possible to perform the entire calibration process automatically using the
Calibration Unit
(accessory ZV-Z51)
.
The system error correction data determined in a calibration procedure are stored on the
analyzer. You can read these correction data using the remote control command
[SENSe<Ch>:]CORRection:CDATa.
You can also replace the correction data of the analyzer by
your own correction data sets.
In addition to the system error correction described in this section the analyzer supports source and
receiver power calibrations using external power meters and generators. Refer to the help system for a
comprehensive overview and comparison of the calibration types, including their use, properties and
advantages.
Calibration Standards and Calibration Kits
A calibration kit is a set of physical calibration standards for a particular connector type. The
magnitude and phase response of the calibration standards (i.e. their S-parameters) must be known
or predictable within a given frequency range.
The standards are grouped into several types (open, through, match,...) corresponding to the different
input quantities for the analyzer's error models. The standard type also determines the equivalent circuit
model used to describe its properties. The circuit model depends on several parameters that are stored
in the cal kit file associated with the calibration kit.
As an alternative to using circuit models, it is possible to describe the standards by means of S-
parameter tables stored in a file.
Summary of Contents for 1145.1010.04/05/06
Page 10: ......
Page 20: ......
Page 22: ......
Page 48: ......
Page 70: ......
Page 72: ......
Page 90: ......
Page 92: ......
Page 108: ......
Page 156: ......
Page 162: ......
Page 406: ...Display Menu R S ZVA ZVB ZVT 1145 1084 12 4 244 E 6 Stack Tile Horizontally Tile Vertically...
Page 450: ...Status Reporting System R S ZVA ZVB ZVT 1145 1084 12 5 18 E 1...
Page 462: ......
Page 766: ......
Page 772: ......
Page 792: ......
Page 794: ......
Page 808: ......