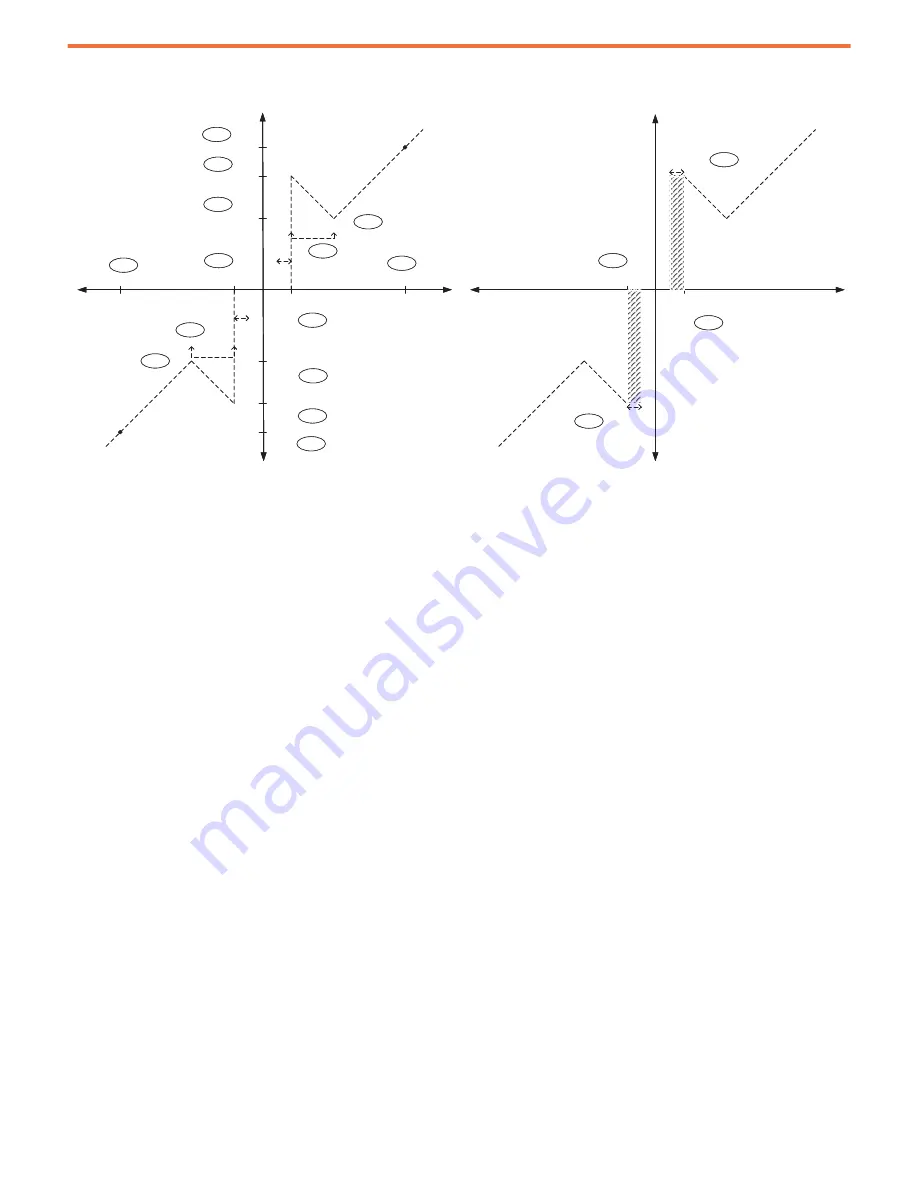
102
Rockwell Automation Publication 750-AT006D-EN-P - January 2022
Chapter 7 Applications
Figure 83 - Friction Compensation Parameters
Torque Sharing
Torque sharing applications typically use two or more motors to share torque in a master/slave configuration. The master is configured to
regulate position or velocity and the slaves are configured to regulate velocity or torque. It is also typical for the master to have an integral
gain K
I
> 0 and the slaves to have integral gains K
I
= 0 so they do not oppose the master.
Droop
Droop is used to shed load when a compliant coupling exists between the motors. The master drive regulates velocity and the followers use
droop so they do not oppose the master. The input to the droop function is the commanded motor torque. The output of the droop function
reduces the speed reference.
10:1961 [Droop RPM at FLA] – This parameter sets the velocity regulator droop. It is the amount of base speed, in rpm, that the speed
reference or velocity command is reduced to when at full load torque. For example, when 10:1961 [Droop RPM at FLA] is set to 50 rpm and the
drive is running at 100% rated motor torque, the droop function subtracts 50 rpm from the speed reference. However, use of the droop
function causes the motor speed to decrease with an increase in load.
10:1763 [PReg Droop] – This parameter sets the position regulator droop. It limits the position regulator integral gain K
PI
< 1/droop. This
parameter provides a means to fine-tune the stability for load-mounted feedback devices where compliance and backlash can cause
problems. Droop is displayed in units of seconds. Here, a 1-second droop represents a load position error equal to the change in position
counts in 1 second at nameplate motor velocity. Droop = 1/K
VP
can be used as a guideline. However, tightly coupled loads typically do not
require the use of droop. Instead, the master is configured with an integral gain K
I
> 0 and the slaves are set with K
I
= 0.
Speed
Torque
+
+
-
-
+ FrctnComp Slip
- FrctnComp Slip
+ FrctnComp Stick
- FrctnComp Stick
+ FrctnComp Rated
- FrctnComp Rated
+ Motor NP RPM
+ FrctnComp Trig
- FrctnComp Trig
FrctnComp Hyst
FrctnComp Hyst
FrctnComp Time
FrctnComp Time
-Motor NP RPM
Speed
Torque
+
+
-
-
+ FrctnComp Trig
- FrctnComp Trig
FrctnComp Hyst
FrctnComp Hyst
2051
2052
2053
2054
2055
2056
2051
2051
2052
2052
2052
2051
2055
2054
2056
2053
403
403
Speed
Torque
+
+
-
-
+ FrctnComp Slip
- FrctnComp Slip
+ FrctnComp Stick
- FrctnComp Stick
+ FrctnComp Rated
- FrctnComp Rated
+ Motor NP RPM
+ FrctnComp Trig
- FrctnComp Trig
FrctnComp Hyst
FrctnComp Hyst
FrctnComp Time
FrctnComp Time
-Motor NP RPM
Speed
Torque
+
+
-
-
+ FrctnComp Trig
- FrctnComp Trig
FrctnComp Hyst
FrctnComp Hyst
2051
2052
2053
2054
2055
2056
2051
2051
2052
2052
2052
2051
2055
2054
2056
2053
403
403
Friction Compensation Adjustments
Friction Compensation Hysteresis