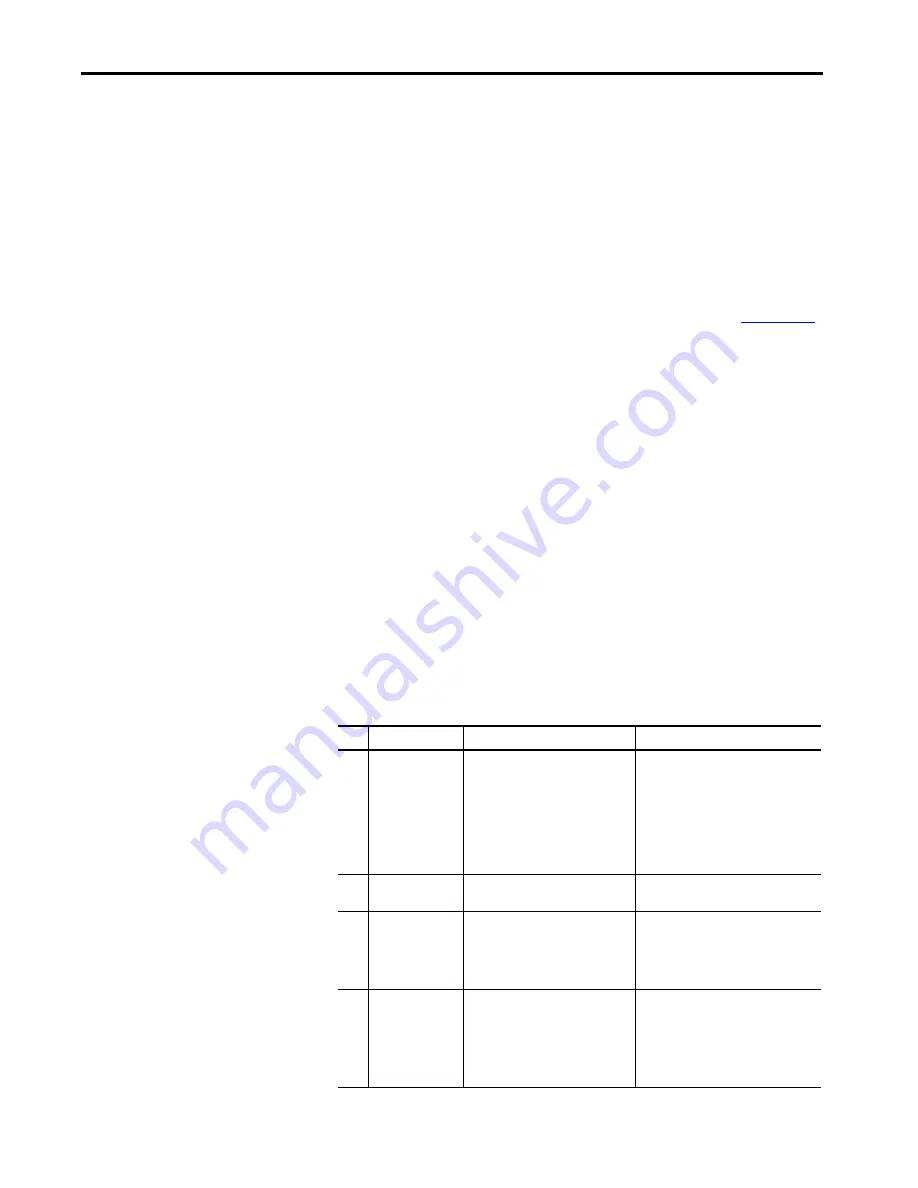
12
Rockwell Automation Publication 20Y-TG002C-EN-P - April 2017
Chapter 1
Troubleshooting and Error Codes
Create Fault Reports
Complete fault reports are critical for analysis and repair of modules that are
returned to the factory.
At a minimum, perform these tasks:
• Use an Allen-Bradley® drive configuration tool such as Connected
Components Workbench™ software, DriveExplorer
™
software, or
DriveExecutive
™
software, do perform these tasks:
– Upload all parameters from the PowerFlex Active Front End.
– Run the technical support wizard.
• Collect the AFE system application data that are shown in
• If possible, record the contents of the fault queue (faults and times of
occurrence).
• Record the following information:
– Any burn marks on the rectifying module, DC capacitors, inverter
bridge, charging resistors, balancing/precharging resistors, printed
circuit boards, bus bars, cabling, and fiber-optic cabling.
– Any liquid and condensation marks on printed circuit boards,
components, and mechanical parts.
– Amount of dust and other additional particles on drive and drive
components.
– Any mechanical damage to the drive and drive components.
• Record the size and type of main fuses.
• Record any other important marks and damage.
• Note grounding type (solid, high resistance, or floating) and source
impedance of the power distribution system.
Addressing PowerFlex Active
Front End Faults
No. Name
Description
Action (if appropriate)
1
PrechargeActv
The AFE is still in precharge, because
the charging switch is open:
• K20, K6, and K1 for AFE in IP20
2500 MCC Style enclosure
• K20, K6, and Q1 for AFE in IP21
Rittal enclosure
Faulty operation.
Component failure.
Reset the fault and restart.
If the fault reoccurs, contact technical
support.
2
Auxiliary In
The AFE control digital input interlock
is open.
Verify wiring to the digital inputs on the
AFE control board is correct.
4
DC UnderVolt
The DC bus voltage fell below the
minimum value of 333V for 400/480V
units, or 461V for 600/690V units. You
can enable/disable this fault with
parameter 120 [Fault Config].
Monitor the incoming AC line for low
voltage or power interruption.
5
DC OverVolt
The DC bus voltage exceeded the
maximum value of 911V for 400/480V
units, or 1200V for 600/690V units.
Check if the AFE was in a regenerative
current limit condition, which can indicate
an excess regenerative load.
Adjust parameter 076 [Regen Power Lmt].
Monitor incoming AC line for high voltage
or voltage transients.