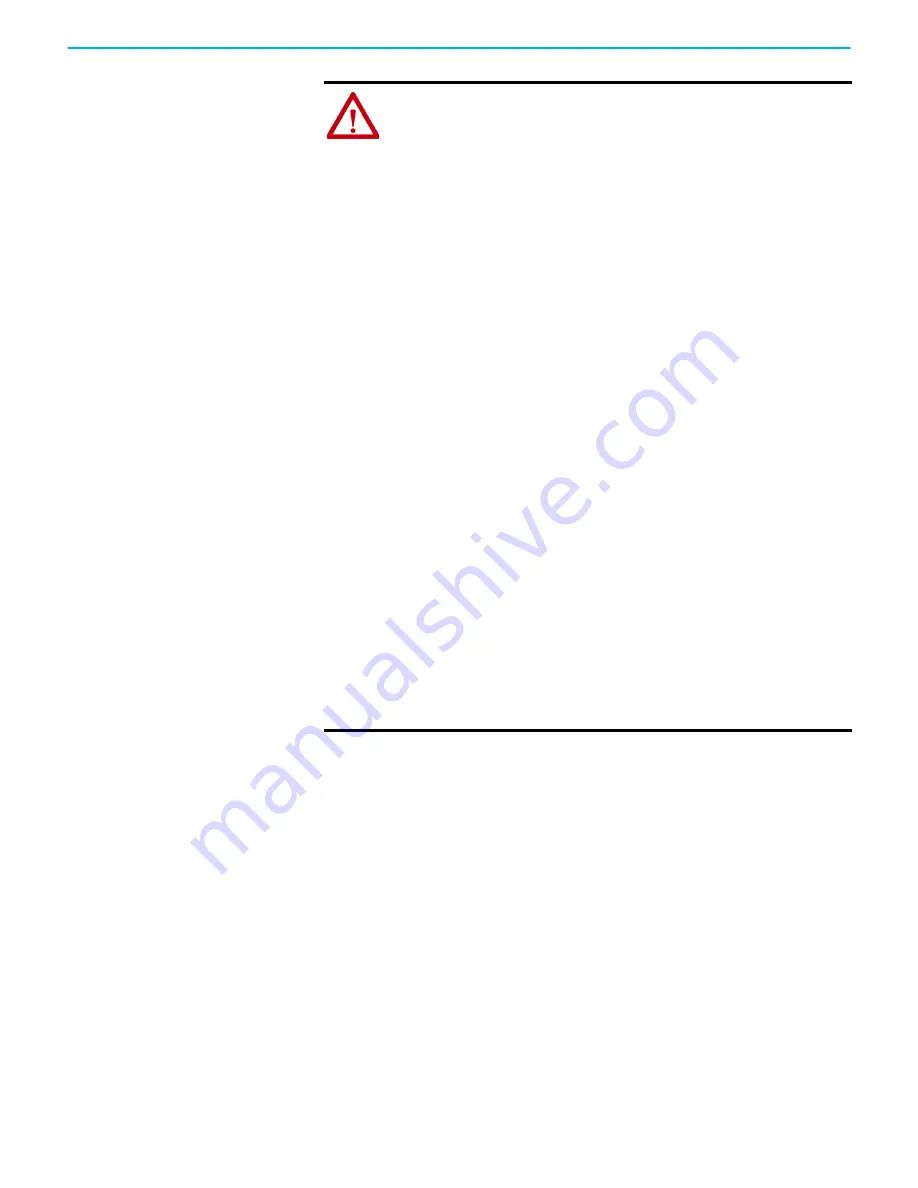
Rockwell Automation Publication 520-UM001K-EN-E - August 2021
13
Preface
General Precautions
ATTENTION:
The drive contains high voltage capacitors which take time to
discharge after removal of mains supply. After power has been removed from
the drive, wait three minutes to make sure DC bus capacitors are discharged.
After three minutes, verify AC voltage L1, L2, L3 (Line to Line and Line to Ground)
to ensure mains power has been disconnected. Measure DC voltage across DC-
and DC+ bus terminals to verify DC Bus has discharged to zero volts. Measure
DC voltage from L1, L2, L3, T1, T2, T3 DC – and DC+ terminals to ground and keep
the meter on the terminals until the voltage discharges to zero volts. The
discharge process may take several minutes to reach zero volts.
Darkened display LEDs is not an indication that capacitors have discharged to
safe voltage levels.
ATTENTION:
Only qualified personnel familiar with adjustable frequency AC
drives and associated machinery should plan or implement the installation,
start-up and subsequent maintenance of the system. Failure to comply may
result in personal injury and/or equipment damage.
ATTENTION:
This drive contains ESD (Electrostatic Discharge) sensitive parts
and assemblies. Static control precautions are required when installing, testing,
servicing or repairing this assembly. Component damage may result if ESD
control procedures are not followed. If you are not familiar with static control
procedures, reference A-B publication 8000-4.5.2, “Guarding Against
Electrostatic Damage” or any other applicable ESD protection handbook.
ATTENTION:
An incorrectly applied or installed drive can result in component
damage or a reduction in product life. Wiring or application errors, such as
undersizing the motor, incorrect or inadequate AC supply, or excessive ambient
temperatures may result in malfunction of the system.
ATTENTION:
The bus regulator function is extremely useful for preventing
nuisance overvoltage faults resulting from aggressive decelerations,
overhauling loads, and eccentric loads. However, it can also cause either of the
following two conditions to occur.
1. Fast positive changes in input voltage or imbalanced input voltages can
cause uncommanded positive speed changes;
2. Actual deceleration times can be longer than commanded deceleration times
However, a “Stall Fault” is generated if the drive remains in this state for 1
minute. If this condition is unacceptable, the bus regulator must be disabled
(see parameter A550 [Bus Reg Enable]). In addition, installing a properly sized
dynamic brake resistor will provide proper stopping requirements based on
braking resistor sizing.
ATTENTION:
Risk of injury or equipment damage exists. Drive does not contain
user-serviceable components. Do not disassemble drive chassis.
Summary of Contents for Allen-Bradley PowerFlex 520 Series
Page 8: ...8 Rockwell Automation Publication 520 UM001K EN E August 2021 Table of Contents Notes ...
Page 68: ...68 Rockwell Automation Publication 520 UM001K EN E August 2021 Chapter 2 Start Up Notes ...
Page 236: ...236 Rockwell Automation Publication 520 UM001K EN E August 2021 Appendix F PID Set Up Notes ...
Page 270: ...270 Rockwell Automation Publication 520 UM001K EN E August 2021 Index Notes ...