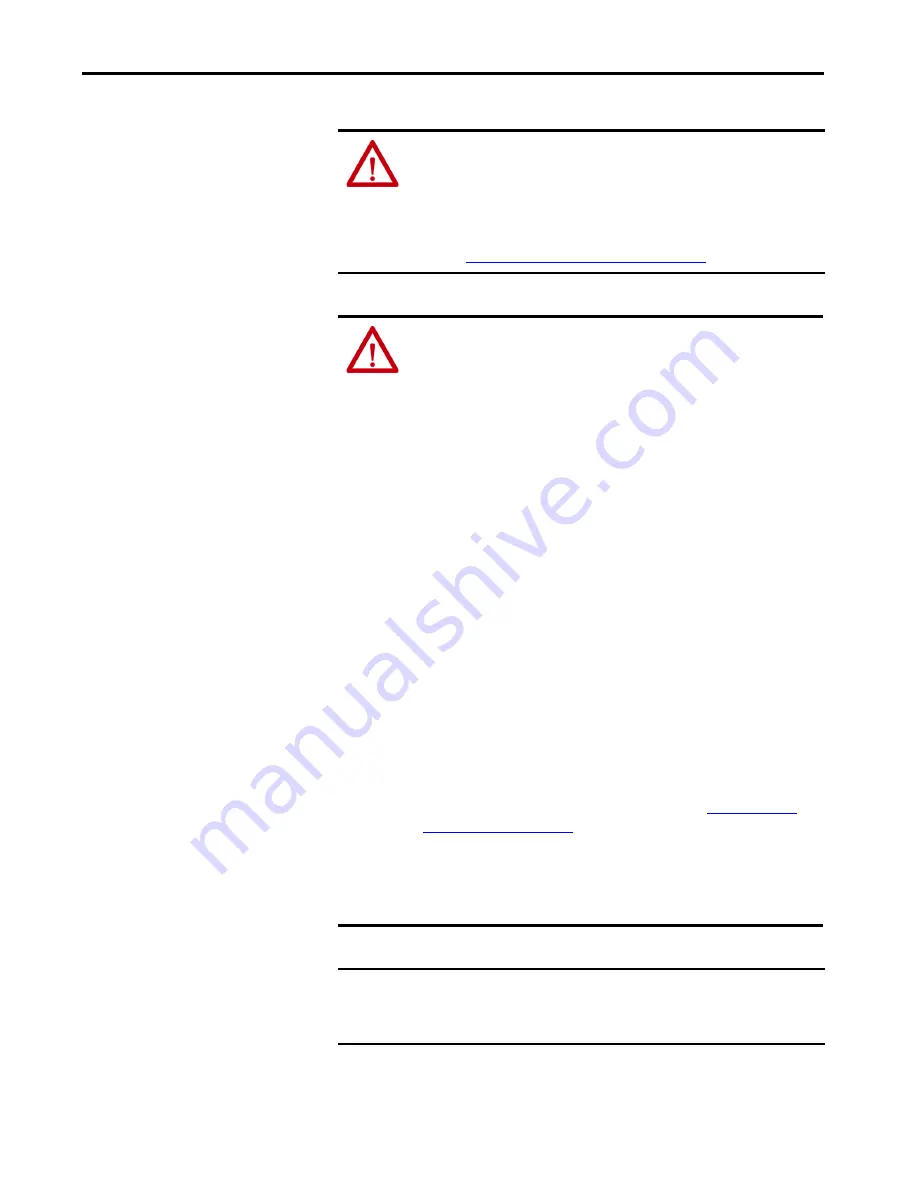
Rockwell Automation Publication 440G-UM001B-EN-P - May 2016
23
Installation and Wiring
Chapter 3
Electrical Connection
WARNING:
• To help ensure safety, both safety outputs (FO1A/FO1B) must always be
evaluated.
• Diagnostic outputs OD, OT, OL, and OI must not be used as safety outputs.
• Lay the connection cables with protection to prevent the risk of short circuits
(see
Requirements for Connection Cables on page 24
).
ATTENTION:
Incorrect electrical connections can lead to damage or
malfunction of the device.
Electrical connections must either be isolated from the main supply by a safety
transformer according to IEC 61558-2-6 with limited output voltage in the event
of a fault, or by other equivalent isolation measures.
A 24V DC Class 2 power supply is required. Alternative solutions must comply
with the following requirements:
a) Electrically isolated power supply with a maximum open-circuit voltage of
30V DC and a limited current of maximum 8 A.
b) Electrically isolated power supply in combination with fuse as per UL248. This
fuse should be designed for max. 3.3 A and should be integrated into the 30V DC
voltage section.
The mounting of conduits directly on the Access Box is not allowed. Cables are
only allowed to be connected using a suitable cable gland. Cable glands can be
used if they are UL Listed (QCRV) and are suitable for the related cable diameter
(22…17 AWG).
All electrical outputs must have an adequate protective circuit for inductive
loads. The outputs must be protected with a free-wheeling diode for this
purpose. RC interference suppression units must not be used.
Power devices, which are a powerful source of interference, must be installed in
a separate location away from the input and output circuits for signal
processing. The cable routing for safety circuits should be as far away as possible
from the cables of the power circuits.
To prevent EMC problems, it is imperative you follow the
. Follow EMC guidelines on devices in the
immediate vicinity of the Access Box system and their cables.
To avoid EMC interference, the physical environmental and operating conditions
at the installation site of the device must comply with the requirements
according to the standard DIN EN/IEC 60204-1:2006, section 4.4.2/EMC).
IMPORTANT
• To help ensure the stated degree of protection is achieved, the cover
screws must be tightened to a tightening torque of 1 Nm.
• Tighten screw for the cover for the mechanical release to 0.5 Nm.